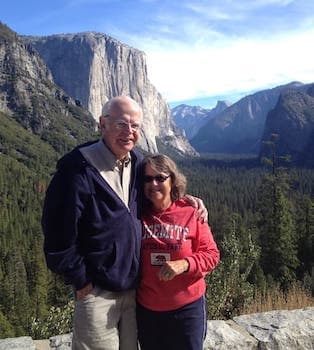
Curated with aloha by
Ted Mooney, P.E. RET
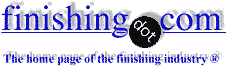
The authoritative public forum
for Metal Finishing 1989-2025
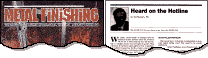
-----
White rust under the painted galvanised coils
2005
We are a big producer of galvanised & painted coils in Iran (Mobarakeh Steel Co.).
in some cases has been observed that the painted galvanised coils has been white rust.
what is the reson of this case?
Mobarakeh Steel Co. - Esfahan
Although the problem could have several causes, Masoud, it sounds like a simple case of "wet storage stain". Galvanized surfaces are quite corrosion resistant when exposed to the open air, but when they are wet and not open to the air the corrosion process proceeds differently, resulting in white rust.
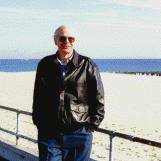
Ted Mooney, P.E.
Striving to live Aloha
finishing.com - Pine Beach, New Jersey
2005
2005
Sir: There are many causes of white rust including: (1)Too high of aluminum in the zinc. (2)Tin (Sn) in the zinc. (3)Dirty quench water.
(4)Incorrect pH of chromate quench. (5) Using "hard" quench water.
(6)Using paint that is not compatible with zinc. (7)Allowing the galvanized product to get rained on before the two days required for the zinc to attain its protective coating. (8)Stacking the product too tightly together which does not allow the product to dry (of quench water) properly after galvanizing. (9)Using quench water that is contaminated with chlorides from the flux. (10) Lead (Pb) in the zinc. (11)Copper in the Zinc. (12)Exposure of the galvanized product to HCl fumes in the plant.
Regards,
Galvanizing Consultant - Hot Springs, South Dakota, USA
2006
The same problem happens in Skopje also. The reason was storage of the Zn coils on olpen space. Those coils were Cr +6 passivated we also increase the concentration of Cr acid up to 5%. White rust cannot be eliminated in a process of PPG (Scotch bridles, alkaline and acid treatment) the paint protection in that case is for a very short time. The material is with bad quality. If you use Cr+6 passivization you should check the concentration of Cr+6 ions in a tank.
If is necessary to remove the solution and prepare a new one.
Use a cols very fast from Zn to PPG line.
Mittal Steel Skopje - Skopje, Macedonia
2006
Sirs:
I wish to comment on Zarko's advise to use 5% hex chromium to passivate the zinc. I have worked for many general galvanizers and done substantial research on hex chrome passivation on galvanized steel. Using correct methods a 500 ppm (0.05%) hex chrome solution properly maintained can easily pass a 40 hour salt spray test and the solution can easily be used for more than five years in a high production plant. This coating is not visible.
In the USA hex chrome is very limited in use on only a few products. Many general galvanizers use special methods that require only
0.0005% Aluminum to 0.001% Aluminum to produce a very bright product.
Such a high concentration of hex chrome as suggested by Zarko would likely leave dangerous amounts of hex chrome on the galvanized surface and could be a cancer problem.
Regards,
Galvanizing Consultant - Hot Springs, South Dakota, USA
Dear Mr.Thomas
Because of our problems with white rust on Zn coils (using Cr+6) passivization we contact our chem. supplier, very famous company in Europe.
They ask for a higher concentration of Cr+6 treatment up to 5% and we don't have problems with yellow edges.
I now about the medical problems with Cr+6 and we will replace him with Cr free treatment with Ti.
But the difference between 5% and 0.5% is very big I will check again with chem. eng. in our labs.
Mittal Steel Skopje - Skopje, Macedonia
2006
2006
Dear Zarko:
In 1978 I measured airborne hex chrome from a 0.1% hex chrome solution. One meter from the solution or the hot galv. surface the results for hex chrome were:
97 °C slow boil (above beaker) 0.066 mg/cu m.
150 °C. galv. steel (dripped solution) 19 mg/cu m.
300 °C. galv. steel (dripped solution) 119 mg/cu. m.
The USA NIOSH Pocket Guide to Chemical Hazards 1994 ed. gives max. exposure limit for hex chrome of 0.001 mg/cu m.
It also states that the major hazard is [lung cancer].
In order to be effective, a 0.1% hex chrome quench in a high production plant requires simple daily maintenance. What does your European company recommend for maintenance?
Regards,
Galvanizing Consultant - Hot Springs, South Dakota, USA
We are using Galva Passivator, Cr free passivating system with excellent performance.
Wilfred Sprang- The Netherlands
2006

Q, A, or Comment on THIS thread -or- Start a NEW Thread