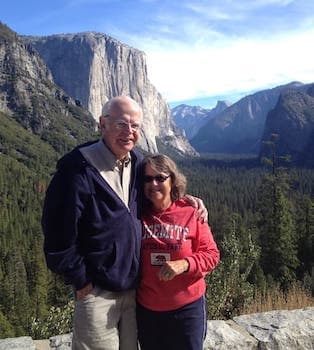
Curated with aloha by
Ted Mooney, P.E. RET
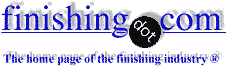
The authoritative public forum
for Metal Finishing 1989-2025
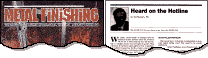
-----
Trike Replacement
2005
Good morning,
I am working for an aerospace company where the quality of product is a priority. Currently my company is facing Solvent Emissions Directive requirements. One of the requirements we worry a lot is the replacement of solvents with R45 phrase (Trike).
We are using trichloroethylene in most of our open-top degreasers. In order to comply with legislation we are intensively looking for some alternatives. There are plenty of them available on the market. But we cannot find anything as cheap, effective and fast removed from the surface as Trike.
I would be really grateful for any suggestions. Thank you.
aerospace - United Kingdom
You have accurately described the situation, Mr. Zygan; there is nothing as cheap, effective, and fast removed. But, as you say, there are plenty of alternatives in the market. Probably the first step is to decide whether you can go to aqueous cleaning or must stay with solvents.
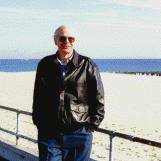
Ted Mooney, P.E.
Striving to live Aloha
finishing.com - Pine Beach, New Jersey
2005
We have used trichloroethylene for years, however, since 1998 it has been used in a "closed" vapor tight degreaser manufactured by Finishing Equipment. Our unaccounted for vapor (i.e. "emissions") went from over 20,000 pounds per year to less than 2,000 pounds. There are other systems, some even vacuum based such as SEREC in the US and others in Italy that do similar. The key word you used in your description of your operating condition is "open top"; in my youth growing up in snowy central New York region, my mom always yelled at me as I was going out the door "wear a hat!". If you simply put a hat on, your emissions would be dramatically reduced. Putting a double door breeze way over the degreaser where only one of the 2 doors can be open at any one time, would cut them even more. Look at simple engineering controls prior to throwing out the solvent.
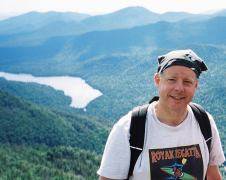
Milt Stevenson, Jr.
Syracuse, New York
2005
We used Trike. in our degreasers for over thirty years, but is was of course reclassified some years ago as a carcinogen and we were obliged to seek alternatives.
It is unlikely that any product will match Trike for efficiency and price.
We are now using an nPropyl Bromide product for the past three years which is proving to be successful in removing our various soils and of course our masking wax residue.
It is expensive and has a lower boiling point than Trike.but to date it is not considered carcinogenic and has been approved by our EPA.
What we have noticed is we are using less solvent per annum, so whether this has to do with the product or the installation of a chiller unit on the plant is not clear at this point.
Aerospace - Dublin, Ireland
2006
First of two simultaneous responses -- 2006
A commonly suggested substitute for trike is n-propyl bromide, but it is more expensive. Unfortunately it is a fact of life that alternatives to trike are more expensive and not necessarily as good, that is why trike was used! We all know that trike is becoming more difficult to use and that emissions are one major concern; this is connected to the desire to eliminate the discharge of greenhouse gases,ozone depleters etc etc. Using better degreasers with reduced emissions is one short term step, but there is a restriction on the use of the materials to begin with, so that will not be a long term solution. You really need to seek an alternative process. I believe the aerospace industry is tightly regulated, as it should be, to prevent potentially harmful procedures being used in critical processing steps. Changing cleaners may be considered a critical step, so make sure you remain within spec for the product. There are numerous alternative cleaning processes available, such as aqueous systems with or without ultrasonics. There are also a range of organic systems available. I would talk to the supply houses and tell them straight that the job is for aerospace and all processes must be "aerospace compatible". You may even be able to use lasers (excimer) or CO2 technologies to clean the products.
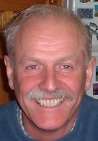
Trevor Crichton
R&D practical scientist
Chesham, Bucks, UK
Second of two simultaneous responses -- 2006
The replacement of Trike as a degreaser in the UK has an increasing priority due to the enforcement of the Solvent Emissions Directive (SED). This puts severe limitations on the allowable emissions of any solvent classified with the R-45, 46, 60 or 61 phrases (not just the R-45 May cause cancer). There are less stringent restrictions on solvents classified as R-40 or 68, but restrictions none the same.
When it comes to replacing the solvents you have to look at exactly what you need to do. Are you cleaning steels, aluminium, magnesium, copper etc? What are you cleaning from the surface? Are we talking heavy oils, greases, light oils or are we using it because we always have?
Once you have determined what you want to clean and what you want it to do you can then move onto the next stage, product type selection
(note I didn't say product selection). Ask yourself "Do I need to solvent degrease?" If the answer is no then look at alkaline washing technologies. If it is yes then does it have to be chlorinated or brominated? If not there are various solvents on the market (they are quite expensive at the moment) that you may consider.
If it needs to be chlorinated then can you use either methylene chloride or perchloroethylene? Under current UK classification these both have the R-40 phrase (ref EH40/2005) and are not quite as tightly restricted as the R-45 etc materials. You will have to look at the properties of these solvents before you make a decision
(methylene chloride has a lower boiling point than trike, perchloroethylene is higher).
If, after all that, you need to use trike (or one of the other solvents classified as R-45, 46, 60 or 61) then you will need to look at fully enclosed, zero emissions plant (and they definitely are not cheap).
Be careful about jumping in with n-Propyl bromide yet. There is a Chemical Hazard Alert Notice (CHAN) issued by the Health and Safety Executive (HSE) provisionally classifying it as R-61. This would bring it under the same requirements as trike. I understand that this is being challenged by the manufacturers and suppliers of n-Propyl bromide based degreasers. I haven't seen any progress on this subject for a while. So if any marketers of n-Propyl bromide could let us all know the state of play it would be nice and possibly prevent some very expensive mistakes.
Once you have done all the above you now know roughly what you want. It is now time to talk to all those wonderful chemical suppliers out there, the majority of which will be more than pleased to give you a helping hand.
Having selected your product, tested that it works and that it meets all the health, safety and environmental requirements, you can now talk to all of your customers and ask them if it is acceptable (make sure you have all your test data to hand, it tends to give the customer a warm glow and will reduce the amount of testing required by the customer for approval to use the new cleaning method).
The selection of new degreasing solvents and methods is a long and expensive one. Aerospace companies have not been of the greatest help in the world (the cogs in the Aerospace world turn very slowly) and I don't envision us getting and faster. So, having selected your solvent don't expect an immediate answer.
Aerospace - Yeovil, Somerset, UK
2006
We stumbled into the Trike replacement market by accident having been requested to supply alternatives to one of the UK's largest stainless steel plants. They use heavy lubricants to draw materials that only Trike cleaned successfully. We've developed environmentally friendly alternatives now on extended trials. No easy task. The key was not only to clean the components, but also offer recycling by distillation or ultra filtration. We've just signed up a big chemical producer to supply engineering companies so that the products can reach a wider audience than our small company can ever hope to reach.
I'm sorry but this is not supposed to be a commercial article. Just know that there are alternatives available, not halogen containing, are more expensive than trike but which in-situ ultra-filtration has cleaned up in a big plant and which we believe will be cost neutral overall when you consider the investment required to put in sealed plant to handle trike.
As a formulator, I am amazed at the number of companies still using Trike.
- Chexbres, Switzerland
Q, A, or Comment on THIS thread -or- Start a NEW Thread