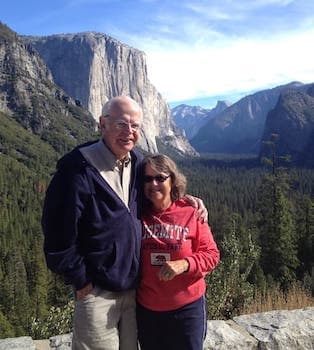
Curated with aloha by
Ted Mooney, P.E. RET
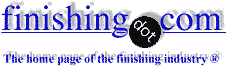
The authoritative public forum
for Metal Finishing 1989-2025
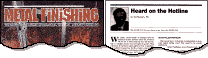
-----
Does a good surface finish make it difficult for paint to adhere
2005
Q. We are painting sheet metal chain covers for two wheelers. The painting conditions are given as under:
Material: Cold rolled steel
Surface finish: 0.5~1.0 Ra
Pre-treatment: Zinc phosphating
(Degrease-rinse-activation-phosphating)
Post-treatment: Primer, base coat (liquid paint), top coat
Recently the parts have started failing in salt spray test within 24 hrs whereas earlier these were passing 120 hrs. Some say that the surface finish of the steel sheet is very low and because of smooth finish, the paint is not having good adhesion. However, I think that this is not the reason and improper degreasing may be the reason.
Please advise if the smooth finish playing any role in low salt spray life. If not, how can I prove it.
- Gzb, UP, INDIA
A. Surface Profile plays major role in paint adhesion. Rough surfaces provide good anchoring effect to the coating film which improves adhesion and salt spray performance of the paint films. If surface is very smooth like glass there will be minimum or no anchoring of polymer molecules on the substrate, which results paint films with poor adhesion and poor salt spray resistance. In your case if you are sure of surface treatment (cleaning, pretreatment) this can be the reason. What is the surface treatment you are doing.
Chilamala- Mumbai
2005
2005
A. I agree with Chilamala. Rough surface enables good anchoring of the paint films. However, you have mentioned that you are observing an early failure in salt spray test (within 24 hours) only recently and the parts having similar finish were passing 120 hrs earlier. So it appears to me that the problem lies in cleaning and/or pretreatment and not on surface roughness.
Adhesion failure is mostly due to poor surface preparation. Check your degreasing and phosphating. Also check your rinse water quality and chloride content.
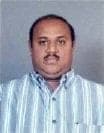
T.S.N. Sankara Narayanan
- Chennai, Tamilnadu, India
(ed.note: The good doctor offers a fascinating blog, "Advancement in Science" )
Q. Hi Guys, does high surface profile (86 microns) cause a paint failure for High Temperature Paint? The total required Thickness of the paint system is 90-115 microns. My DFT readings are 92 - 140 microns. My concern is that I think high profile will cause more paint consumption. But my client does not agree. He suggests to reblast the item.
C.T. Stanley- madurai, tamilnadu, India
March 12, 2018
March 2018
Hi C.T. First off I don't think the extra or reduced cost of paint based on the surface profile should carry any weight at all in your decisions. What you need is a coating system which protects the item from corrosion, and which looks good if the item is visible.
We don't know what the item is, whether it's exposed to the elements or not, what other factors may affect it like wear, what the substrate material is (steel?), why your customer wants to re-blast it, whether the paint actually failed or you haven't painted it yet, whether you phosphate it after blasting and before painting, what kind of paint you are using or why it must be high temperature.
But reading between the lines, can we guess that perhaps the paint has failed, and that the parts are only blasted, not phosphatized, and you want to solve the problem strictly through blasting, without phosphatizing? Please get back to us with answers to my questions, and hopefully someone will be able to help. Good luck.
Regards,
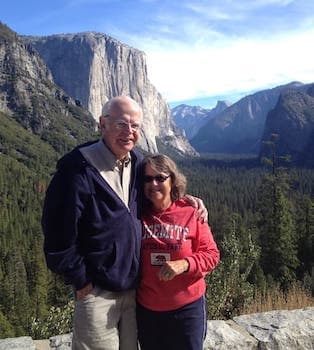
Ted Mooney, P.E. RET
Striving to live Aloha
finishing.com - Pine Beach, New Jersey
Q, A, or Comment on THIS thread -or- Start a NEW Thread