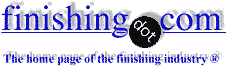
-----
RoHS Compliant Chemical Conversion Coatings
Q. SIR,
I AM LOOKING FOR NON CHROMATE COATING FOR OUR ALLOY LM-24 ALUMINUM DIE CAST PARTS. WE ARE DOING POWDER COATING AFTER PRETREATMENT.
RAKESH SHARMA- DELHI, INDIA
2003
Q. Hello,
I am an E/M Designer working in a industrial manufacturing environment. (Small mechanical parts, motors, etc.)
I currently have a requirement for a Chemical Conversion Coating Class 1A on an small Aluminum part 6061-T6 alloy. I need this part to be RoHS compliant and I understand that there are Chromates used in the Chemical Conversion Coating process.
Can you tell me if this coating is RoHS Compliant when applied?
If this AMSC5541 coating is not RoHS compliant, what coating can you suggest to replace it for effectivity and compliancy.
Any help would be greatly appreciated.
E/M Designer / MFGR. - Clearwater, Florida, USA
2005
2005
A. AMSC5541 coatings (and former MIL-C-5541) are applied using products qualified and listed per QPL-81706 [⇦ this spec on DLA]. Currently all qualified and listed products are hexavalent chromium based compounds that deposit conversion coatings containing, you guessed it - hexavalent chromium. They are all NON-RoHS Compliant. A new breed of TRIVALENT CHROMIUM products to produce conversion coatings on aluminum has been developed and patented by the US Navy and sold thru licensed manufacturers. Search the internet for TCP and you'll find manufacturers of the chemical and applicators of the coating, including my firm. These products meet all the properties of being listed just haven't as of yet been "listed."
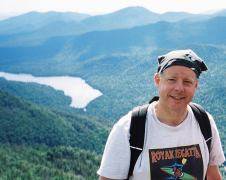
Milt Stevenson, Jr.
Syracuse, New York
A. Hi Don!
First, equipment that we're going to be selling in Europe is being designed using NavAir's TCP (Trivalent Chromium Process) formulations. Henkel, Metalast, and others have licensed the process from NavAir, and can tell you which job shops use their chemicals. We're interpreting the regulations as allowing trivalent chromate, but to be truthful to you, we're also hiding behind our big customer's skirts on this, as they have final responsibility for meeting the regs. It's also a Defense application, so using something developed by NavAir gives some political pull...
I'm not sure what Macdermid is doing about making a non-hexavalent chromate conversion coating, but I'm certain they're working on it as well. A visit to their website might tell you more.
The way we're structuring our drawing note is to call out
"Non-Hexavalent Conversion Coating per Mil-C-5541" which is really a bit self-conflicting, as the Mil spec calls out chemicals per another spec, which doesn't yet allow anything that isn't hexavalent. So our purchase order spells out the process we want our supplier to use, and our customer knows we're doing it this way, so we're all on the same page until the specification can be updated.
And speaking of that, AMSC5541 was cancelled in July 2000, and replaced by the Mil-C-5541. We (Committee B of the AMD committees of SAE, who writes AMS documents covering processes) jumped the gun and issued the AMS replacement for Mil-C-5541 without waiting for the military to cancel it. When they decided to keep that one, we cancelled the AMS to try to stop the confusion.
Hope this clears some things up!

Lee Gearhart
metallurgist - E. Aurora, New York
2005
Q. After searching the internet I came across your Q&A about the subject above. Since there was no "date stamp" on the question or answer, I wonder if anything has changed since it was posted. It was stated that the "trivalent" chemicals necessary for the RoHS compliant conversion coating were, at the time of the question, still not listed as approved chemicals to produce and certify to MIL-C-5541, and that people were "hiding" behind the primes that are requesting said process. Has anything changed and are the trivalent chemicals now listed in the spec that legitimizes processing with these new chemicals?
Tim NicholsPurchasing of Outside Processing - Paramount, California, USA
January 23, 2008
A. Sorry! The letter in question is now date stamped.
Yes, the TCP process which Lee Gearhart talks about is now MIL-DTL-5541 [⇦ this spec on DLA] approved. Remember, however, that each individual product must be on the QPL before it can be used. To our knowledge CST-Surtec, Henkel, Luster-On, and Metalast offer QPL-approved, NAVAIR-licensed, TCP processes.
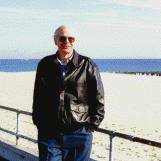
Ted Mooney, P.E.
Striving to live Aloha
finishing.com - Pine Beach, New Jersey
January 23, 2008
A. There are Type II materials fully tested and approved by NAVAIR from five companies. Henkel, Surtec, Metalast, Luster-On, and Macdermid. The QPL has not been updated, but the approval letters are available from the vendors and NAVAIR. MacDermid makes a chrome free material, and the rest are minor variations of the NAVAIR TCP formula. The TCP coating is a faint blue color. MIL-DTL-5541 [⇦ this spec on DLA] was not released until at least three of the coatings had been approved and in commercial production.
Dave Gertydefense - Minneapolis, Minnesota
April 9, 2008
Q. Is there any surface finishes other than Clear Iridite for Aluminum that is RoHS compliant?
Alan Chang- Mississauga, Ontario, CANADA
December 3, 2012
A. Hi Alan. We appended your inquiry to an existing thread which answers it, i.e., RoHS-compliant chemical conversion coatings for aluminum are now widely available, and if needed, Mil Spec compliant as well.
Iridite is a Macdermid trade name for a whole series of coatings; and while some or all of them may be RoHS-compliant, the tradename means whatever they decide it means, so you would really need to check with them.
Regards,
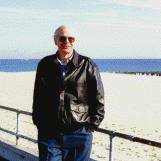
Ted Mooney, P.E.
Striving to live Aloha
finishing.com - Pine Beach, New Jersey
December 4, 2012
March 31, 2015
Q. One of my friends is doing Trivalent Chromating and his parts are turning black instead of blue. Following is the process he follows along with the details of the material he is using.
Trivalent Process Details:
Cleaning Sur Tec 133 : Temp 50 °C to 70 °C
Vol% : 50g/lit
Time : 3- 5 Mins
2 Water Rinsing
Deoxidising Nitric : 10%
Time : 2 mins
2 Water Rinsing
Passivation Surtec 650 :80%Water/20% Chrome
Temp 35 °C - 40 °C
pH : 3.7 - 3.95
Time : 120 - 240 Seconds
2 Water Rinsing
We would appreciate your valuable suggestions.
- Mumbai, India
A. Hello Hitesh. What alloy is your friend processing? It sounds possible that nitric acid is not an appropriate de-smutting agent for the parts in question. I note that the parts are not etched? Your cleaner and conversion coating chemicals are proprietary, but you are using a generic de-smut. Does Surtec offer any comment on that situation? Thanks.
Regards,
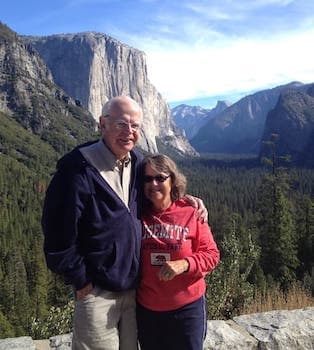
Ted Mooney, P.E. RET
Striving to live Aloha
finishing.com - Pine Beach, New Jersey
April 2015
Q, A, or Comment on THIS thread -or- Start a NEW Thread