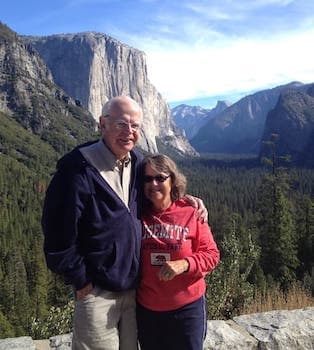
Curated with aloha by
Ted Mooney, P.E. RET
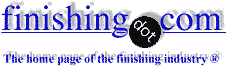
The authoritative public forum
for Metal Finishing 1989-2025
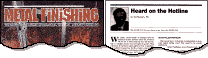
-----
Can anodizing be used to roughen a surface to a given finish surface finish?
Q. I have a sheet of 6061-T6 .032" aluminum. The surface finish as it comes from the metal supplier is too smooth for my application and I would like to apply a surface texture of about Ra 80-100. I have contemplated shot blasting but the sheet warps really bad during that process. I am now considering anodizing the sheet.
What can I do to ensure that I get a surface finish within my desired range by anodizing? I know anodizing tends to increase the surface finish from its original finish, but I am looking to apply a specific finish and what I need to do to ensure that happens.
Also, will my sheet behave any differently when applied to heat. Part of the usage of this sheet, it will go into an oven at 350 °F and I would like to know if the sheet will warp significantly under these environmental conditions.
aerospace - Sunnyvale, California, USA
2005
![]() |
A. The safest way to apply a roughness to a plate like yours is to texture or chemically etch it. There are several texture houses in the west coast that can apply any of the several thousand different patterns available (dots, bumps, striations, splines, etc.) in almost any depth you may desire. Regarding warpage I don't think it could be a problem. In most kitchens there are hot plates for stoves and ovens that show no warpage after years exposed to direct flame. Guillermo MarrufoMonterrey, NL, Mexico 2005 A. I would be against anodize as a means of achieving a controlled surface finish in that there is too much variability during pretreatment and anodizing to ensure a consistent 80-100 RA after anodize. For instance, alkaline etching vs. non-etch cleaning vs. acid etching will give varying surface condition prior to anodizing. Anodizing alone will vary given temperature, applied voltage, electrolyte temperature, etc. I would be more in favor of mechanical finish via Timesaver or brush finishing - akin to blasting but without associated bending of sheet. ![]() Milt Stevenson, Jr. Syracuse, New York 2005 |
![]() |
A. A finish spec of 80-100 (pretty darned tight spec for such an arbitrary measurement as Ra) should be achievable with anodizing, but it will involve either a heavy etch prior to coating, or a rough sanding (perhaps with 220 grit, or rougher, AL203 sandpaper) prior to coating. This will take a little R&D on yours, and your coaters part. You didn't mention the type of anodizing you are trying to apply, or the thickness, both of which have a bearing on the final Ra data. If I were you, I would start off sanding sample pieces to different Ra's, and send to your coater, have him process all the parts at once, and see what works, or see if tweaks need to be made. I would provide your coater with a wide range of samples, both above, and below your finished RA spec. Typically you will double the original (uncoated part) Ra on a 2 mil hardcoat, this will lessen as the coating gets thinner. However, when starting with a rough surface, the typical anodizing process tends to have the opposite effect, and can actually will smooth the surface, due to etching, and the substrate dissolving during the anodizing step. Make sure you are using a coater that has very tight quality control, if you want a repeatable process. ![]() Marc Green anodizer - Boise, Idaho 2005 A. In addition to what Milt said, you must know that under heat the aluminum substrate expands 5 times that of the aluminum oxide on top, and cracks occur. ![]() Robert H Probert Robert H Probert Technical Services ![]() Garner, North Carolina ![]() 2005 |
A. Derrick
You should be able to find a supplier in the South Bay who can abrasive blast your sheet without warping it. If both sides require texturing, it will be even easier. A firm that reworks/reconditions semi-con tools will know what to do.
- Colorado Springs, Colorado
2005
Any real-world experience with anodized components failing from thermal cycling?
Q. Does anyone have any real world experience with "cracking" of an anodize on aluminum due to thermal cycling which was the root cause of a part failure? If so, what was the application and thermal conditions?
(Some readers continue to suggest that anodizing is unsuitable for thermal applications. I do not want a general perception to develop among potential users that anodizing should not be considered for these types of applications.)
Luke Engineering & Mfg. Co. Inc.

Wadsworth, Ohio
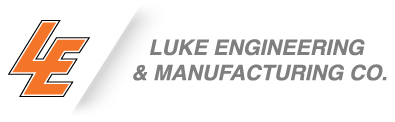
2005
A. I, too, would like to hear specifics about any failure so that we can put that concern into a real-world context instead of it just vaguely hanging over us! It is no doubt true that anodized coatings are somewhat brittle and do not expand as fast as aluminum and this could cause variations in surface roughness which the original inquirer was concerned about ... but, it addition to numerous engine parts and other hot industrial applications that I am familiar with, I will be a broken record and continue to talk about how happy I am with our Calphalon hard-anodized frying pans. They perform with remarkable reliability and absolutely no concern about just popping them down on a gas fired stove top, day after day, year after year. So if thermal cracking occurs, it's also possible that in most cases it is of no consequence.
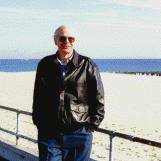
Ted Mooney, P.E.
Striving to live Aloha
finishing.com - Pine Beach, New Jersey
2005
A. To Chris Jurey:
NASA Technical Memorandum 104622, "Preventing Cracking of Anodized Coatings", August-----. Available from NASA Technical Reports Server.
Government-Industry Data Exchange Program Problem Advisory F3-P-99-02, 3 February 1999. Available from GIDEP.
- Beltsville, Maryland, USA
2005
A. Re: high temp applications with hard anodizing: Consider racing pistons; in Top Fuel virtually all the teams run type III coated pistons.
Leonard Warren- Murrieta, California, USA
December 17, 2010
Q, A, or Comment on THIS thread -or- Start a NEW Thread