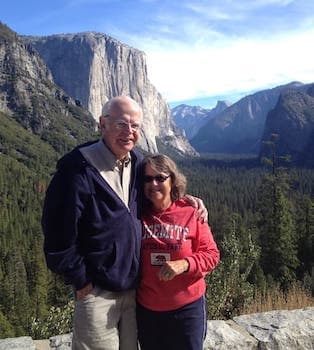
Curated with aloha by
Ted Mooney, P.E. RET
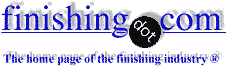
The authoritative public forum
for Metal Finishing 1989-2025
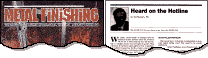
-----
Nickel Plating on Stainless Steel Electrical Connectors
The question is regarding nickel plating on stainless steel electrical connectors. These connectors go onto fuel control systems for aerospace applications. The plater subtier claims the peeling, bubbling, flaking of the nickel finish is not coming from them. Yet under a 40x microscope I can see chips of metal left behind from the fabrication process with plating on them. Our customer claims there is nothing they are doing to cause the trouble. yet we don't use a mating connector on them during our processing. I've only begun to look at the issue and have run across a couple of things.
The plating comes off if I use just a
Kimwipe with alcohol. By coming off I mean the shiny surface turns into a black surface. It is kind of like a kids toy that has chrome on it. When the plating comes off it leaves behind a black residue. What is the black residue that is left behind on the connector? The connector comes to us with this black surface finish on it right from the vendor. The Kimwipe cleaning makes it worse. Is it the surface of the metal or is a binder of some sort? Why would the plating come off with just a Kimwipe/Alcohol cleaning?
We also heat these connectors as part of stress relieving processing. Can that cause the plating to bubble or degrade the binding agent? The units are thermo cycled for about 4 hours at 200 F. The plating also has bubbles as shipped to us. When the bubbles are popped and we remove the plating material the bare metal underneath is still not exposed. It has what appears to be plating.
I cannot give the specific application of these connectors or the valves they go onto but everyone involved are getting pretty angry. Each time one of these control systems is rejected because of connector plating issues it costs the customer a lot of money.
- East Amherst, New York, US
2005
First of two simultaneous responses --
Definitely sounds like a lousy plating job to me. When properly done, a nickel plating over anything plateable (and SS is plateable) should not come off even with after a bend test or a tape-pull test.
Guillermo MarrufoMonterrey, NL, Mexico
2005
Second of two simultaneous responses --
Unless your part is made from carbon there is no way the part should be black after the chrome peels off. The manufacturer of the connector shell or the plater has committed a grievous act - we nickel plate stainless steel connector shells every day. The fact that you've had this trouble and that these are for the aerospace industry makes one think that a Nadcap-accredited plating house should have been used - that type of house has the added intellect, process control and post-plate inspection to ensure that the parts are done right. The fact that the plating house sent you visibly blistered parts makes me question the type of plater you use - hopefully they were the low bidder!
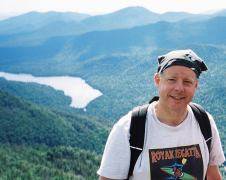
Milt Stevenson, Jr.
Syracuse, New York
2005
2005
The black residue may be a nickel oxide or sulfide.
Some stainless steels are difficult to machine cleanly. Surface material bends over and entraps cutting lubricant, which then bubbles up when heated. Dull tooling also burns some lubricants into the surface. The "chips of metal left behind from the fabrication" indicates poor finishing by the machine shop.
The plater's quality system is also derelict for not detecting this problem and in shipping the product. Certs?
Electropolishing (after proper machining) will assure a clean surface prior to plating. See also
ASTM B254 Standard Practice for Preparation of and Electroplating on Stainless Steel.
- Goleta, California

Rest in peace, Ken. Thank you for your hard work which the finishing world, and we at finishing.com, continue to benefit from.
Your description is pretty good for a poor plating job. Unfortunately you don't give much detail of your process, only what's gone wrong. I presume you have had successes in the past with the stainless steel substrate, but if it is a new job, is the stainless suitable for plating? - some types rich in sulfur are not conducive to electroplating, so make sure of that. If it is OK for plating then the next step is to make sure you sub contractor is giving the stainless a good nickel strike - you cannot get good adhesion of nickel to stainless without a strike. If they are doing a strike, then the cleaning process may not be up to scratch. I think to get a sensible answer, you need to give us the full specification and process, otherwise we are just shooting in the dark.
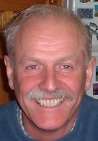
Trevor Crichton
R&D practical scientist
Chesham, Bucks, UK
2005
Sounds like a cleaning , or possibly a cleaning AND nickel strike issue....
without seeing the parts... maybe a preclean in ultrasonics? or an electroclean? more info is needed to adequately approach it...
plating equipment supplier - Bristol, Connecticut
2006
March 27, 2009
One thing you failed to mention is if you had any down time on the plater, and your rectifier is working properly (no down time during plating). That could cause bubbling few days after the part is plated. This is something that you don't see right away.
If that is not the case, then I would pay attention to the cleaners and your strike.
One thing you want to check also is your acid bath, make sure it is oil free, because you could be carrying the organic over to the acid from the cleaners if your cleaners are dirty, which in turns will give you the poor adhesion and the bubbling.
- Cleveland, Ohio
Q, A, or Comment on THIS thread -or- Start a NEW Thread