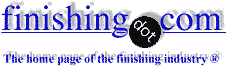
-----
Optical Black Anodize mottled finish problem
2005
For many years we have had aluminum 6061-T6 and T651 (plate) machined pieces anodized "optical black "(non-organic dye) with success but lately have run into a problem that happens irregularly with parts not taking the dye uniformly. The black becomes interspersed with a color that "appears" to be like a gold-tinted clear hard anodize. The center of material is the worst, almost uniformly streaked taking less black coloring than the rest of the material, and this is throughout the material not just on the outside surfaces, pockets will exhibit the same streaky-mottled finish at the same depth as the outside.
Our plating suppliers have double-cleaned their tanks to remove possible contamination etc. and have assured us they are closely monitoring their processes. They suggest that the un-uniform mottled black is being caused by off-shore impure material, however not all of the pieces exhibiting this characteristic comes from off-shore material suppliers. We have also made sure contaminates are not being introduced at our end, such as chemical contaminates from cutting fluids, dissimilar materials, etc.
This mottling does not happen when standard black hard anodize finish is specified on 6061 plate, only with the optical black process.
It is my understanding that some plate is re-rolled to flatten it out. Can this process induce significant material changes throughout the material to be a factor?
Does this sound like a plating, sealing, cleaning, racking, temperature, inferior dye problem? or?
We need to get a uniformly black part on these parts, they are used in laser systems in a clean room environment.
Anyone have any ideas on what is causing this and how to solve it?
Thanks,
precision machining - Sherwood, Oregon, USA
First of two simultaneous responses --
Gary
What you describe sounds like a material issue.
A couple of options to start with;
1] Send some samples to another supplier for comparison. Ideally, you would send samples you know have the flaw, such as stripped and refinished parts.
2] Have some rejected parts stripped and see if the flaw 'pattern' is still present/visible in the material. Etching in a caustic soda ⇦liquid caustic soda in bulk on
Amazon [affil link]
solution will enhance a number of material conditions.
- Colorado Springs, Colorado
2005
Second of two simultaneous responses --
And I thought it was just us! We offer a similar 2-step electrolytic blackening process that from time to time we've experienced similar condition that we call "tiger stripe." We've made up new coloring tank solution, stripped the parts and re-run them and right back they come. The next job run, nothing of the sort. As the process is dependent penetration of a metallic ion into the pore structure of the anodic cell, my theory is that something in the pore is preventing the ion from getting in there or that the power isn't sufficient to drive the reaction. To us, we've seen it but haven't been able to eliminate it.
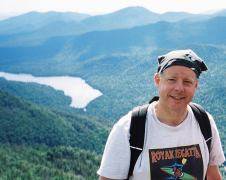
Milt Stevenson, Jr.
Syracuse, New York
2005
2005
Update on the mottled optical black anodize problem.
We've experimented with taking previously anodized mottled parts and having them stripped of the optical black anodize, in conjunction with trying a secondary source for this finish. For this experiment we also took virgin parts made from material that came from the same lot that the stripped parts were made from and sent them along for anodizing at the same time.
So far the parts we have receive back from this source have all been successfully anodized with a uniform optical black finish, even the previously mottled ones are now uniform. This leads us to believe our problem may be with the finishing process and not the material or pre-finish processes.
An additional data point follows; In the expired Martin Marietta patent 4,111,762 paragraph 35, states that the sealing temperature should be maintained between 180-200 degrees to stabilize the dye against wash out.
Possibly this is a factor that has contributed to the lack of uniform dye remaining in the finish of some parts. Possibly the position of parts in the tank and/or the ability to maintain this temperature uniformly for all parts that are racked is a contributing factor.
We are continuing to explore other possible causes or factors that may contribute to the mottled optical black anodized parts.
Thank you to all of those who responded to this forum publicly and those that responded privately. Your input is appreciated.
- Sherwood, Oregon, USA
Q, A, or Comment on THIS thread -or- Start a NEW Thread