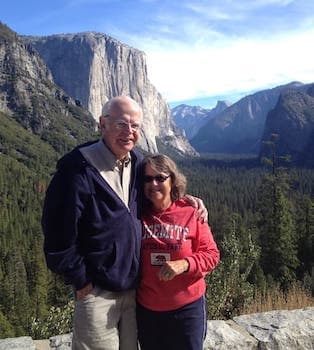
Curated with aloha by
Ted Mooney, P.E. RET
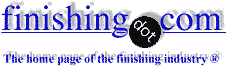
The authoritative public forum
for Metal Finishing 1989-2025
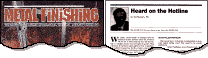
-----
Problem clear anodizing MIC-6 material
April 2, 2021
Q. MIC-6 Anodizing white splotches?
Recently, we have been manufacturing more MIC-6 Aluminum Tooling plates for our custom automation equipment and have experienced some surface issues. We rely on outside shops for our anodizing processes. For clear anodizing all aluminum alloys, we standardize on "MIL-A-8625, Type II, Class 1, Clear". The finish callout is used either directly on prints or also on Purchase Order to coater.
Issues:
White areas
Permanent staining of surface from isopropyl cleaning
Fingerprints stay more readily
We have not experienced the same issues with 6061-T6 anodized parts in past.
I have read some of the great resources on finishing.com related to anodizing MIC-6, challenges and processes recommendations to achieve satisfactory results.
https://www.finishing.com/102/40.shtml
https://www.finishing.com/14/19.shtml
https://www.finishing.com/281/28.shtml
I've attached an image of the surface appearance issues.
My question is from an Engineering firm perspective, are there some additional notes or requirements, beyond the standard callout I mention above, recommended to add to a manufacturing drawing when anodizing MIC-6 to prevent issues in the future?
While we do purchase material from reputable sources, I'm not certain if there were material certifications provided with the plates in question. Have had this issue on multiple runs now of plates for our equipment.
Thanks!
- Chandler Arizona
A. Jeff
The part looks like it is burned, meaning it was anodized too long / too high a current density, had insufficient agitation, or the solution temperature was too high.
A burned surface will look powdery (if dyed), or feel 'gritty' to the touch as compared to a surface that is normal. You might detect a thickness difference between two areas of the same part, burned vs. not burned.
If multiple parts are processed at the same time with the parts facing one another, too close spacing and poor solution movement will cause the center areas of the parts to burn.
- Green Mountain Falls, Colorado
April 15, 2021
Thanks for the education, Willie! In electroplating we would be very surprised if the center area of a part burned and not the edges, but your explanation of how the center of an anodized part can burn due to poor agitation/overheating was enlightening :-)
Luck & Regards,
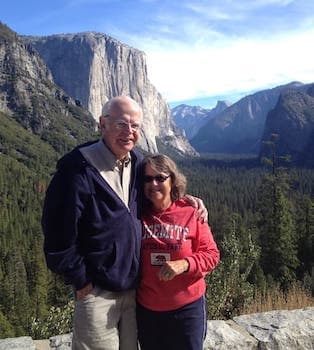
Ted Mooney, P.E. RET
Striving to live Aloha
finishing.com - Pine Beach, New Jersey
April 2021
⇩ Related postings, oldest first ⇩
Q. I need to know if clear anodizing is possible on mic 6 and get consistent looking parts or is it the same as color.
Thanks
Sam Devaiomega diamond inc. manufacturing - Loomis, California, USA
2005
A. Mic 6 is a heavily alloyed tooling plate, and won't clear anodize consistently from lot to lot (I've even had inconsistent parts from the same lot). For best results, do not etch this alloy, especially when dyeing. Me thinks for overall consistency, dyeing Mic 6 is better, as long as your coater has his process under control.
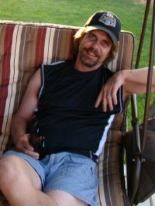
Marc Green
anodizer - Boise, Idaho
2005
A. They're right do not etch mic 6. However, I have had some mic 6 that is machined all over that comes out better with an in/out etching done to it. Also, make sure you are working with Alcoa mic 6 and not a so called "equivalent", because they are not. The easiest way to tell is Alcoa has a pvc that says Alcoa, the other has just a plain blue pvc.
Steve Tanner- Garland, Texas
2005
Q. I have to apply clear anodizing to MIC-6 material. Unfortunately, after anodizing, the surface of this material has a lot of porosity.
Any answer for the above question is greatly appreciated.
- Penang, Malaysia
2005
A. See above and letter 1419 "Neutralizing sulfuric anodizing solution with bicarbonate or nitric acid".
Ken Vlach [deceased]- Goleta, California

Rest in peace, Ken. Thank you for your hard work which the finishing world, and we at finishing.com, continue to benefit from.
January 10, 2014
A. HELLO
MIC 6 EN POROSITY.
TO REMOVE THE PORE:
- NO SHADES (NO ATTACK WITH SODA)
- AFTER DEGREASE, immerse NITRIC ACID RESIDUES TO ELIMINATE THE DEGREASE.
- MINIMUM LAYER TO REDUCE THE PORES IS 25 micron. If you apply LESS, POROUS MATERIAL SEEN.
I HOPE THIS HELPS.
GREETINGS
- GUADALAJARA, JALISCO, MEXICO
A. Mic6 will be the most difficult of the currently produced cast tool and jig plates to anodize. It is the only one that is a 7000 series base alloy. All of the others (K100s and ATP5) are a modified 5083 alloy, which should anodize much better. I have a feeling a lot of folks use the same technique on different alloys, and get middling results. This is why Steve had mentioned to not use "equivalent" products. I agree, in that Mic6 is not equivalent to the other available alloys for this type of application.
Matthew Kaye- Clinton, Ohio, USA
September 14, 2014
Q, A, or Comment on THIS thread -or- Start a NEW Thread