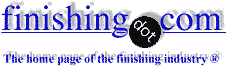
-----
Over additives in Alkaline Zinc bath?

Q. Hello,
Alkaline Non Cyanide Zinc tank with Zinc oxide or other material at bottom of tank?
Zinc is replenished via zinc balls in metal baskets that get immersed in the solution when replenishment is needed, when not they stay in a slightly alkaline rinse tank (1st rinse) to avoid rust buildup on the metal basket.
Yes, zinc level replenishment via this method is no issue, I can maintain the level.
The issue and question is: I am getting a sandy substance building up at the bottom of the tank, I can only assume this is zinc oxide which is having a hard time dissolving. Potentially it's the zinc oxide layer on the zinc balls that falls off and fails to dissolve. I do not know if this will be detrimental to the plating process, so long as it stays at the bottom and doesn't get lifted up during plating.
Is there any tips to minimize this zinc oxide buildup, I have considered immersing the zinc balls in a solution of Nitric or Hydrochloric acid to clean the white zinc oxide layer off before introducing the baskets to the plating tank, however I have been warned to not do this in fear residual acid will be stuck on the zinc balls and eventually get introduced into the plating bath.
- Perth, Australia
January 26, 2024
⇩ Related postings, oldest first ⇩
Q. In our alkaline zinc bath there is an over additives due to bad control, it is over 3-4 times than the standard additives level. And because of this, the plating efficiency dropped 30-40% below the normal efficiency, usually with 2 ASD, Zn level 10 g/L , caustic soda ⇦liquid caustic soda in bulk on
Amazon [affil link]
120 g/L, we could get 10 micron in 30 minutes (Rack plating) ...
But now the plating speed is reduced a lot. Carbonate level is 80 g/L. Please suggest the treatment to do for this problem. We've tried to dilute, adjust & do the plating in the lab scale but still can't get the good result.
metals - Jakarta, Indonesia
2005
![]() |
A. You don't say whether it's an overdose of a specific additive or of all additives. The method of correction will vary depending on what additives are overdosed. - Wales A. Carbonate level of over 45 g/l reduces efficiently of alkaline zinc. Efim Ruchman- Israel |
Q. I have the same problem as you. May I know where the carbonate comes from because my carbonate concentration is high. How to reduce it? (and handle it to avoid carbonation reaction). Thank you.
Anggraenipolimetal - Indonesia
2006
A. Hi, Iwan
If you want to reduce the additives, you have to do carbon treatment to the bath. If you want to reduce the carbonate, take out the top solution and clean the tank, remove all sludge. Change the filters more often.
Best of luck.
- Toronto, ON, Canada
![]() |
A. Dear Susanto/Anggraeni, ![]() T.K. Mohan plating process supplier - Mumbai, India A. The most common method of removing the carbonate from the solution is to 'freeze' it out. At temperatures below 6/7 °C the carbonate will drop out of solution. As Patel states you then need to remove the solution and and clean out the tank. Another method is to install a machine to remove the carbonate. Try a search on 'carbonate removal'. If you are unable to carry out either of these methods then you can always remove a quantity of plating solution and replace it with new solution. It's not a satisfactory method for a variety of reasons but quite commonplace. - Wales |
A. You have been given two methods to overcome the low efficiency problem, use both of them!
Reduce the carbonate level by freezing and increase the zinc metal content.
10 g/l of zinc is not enough for good efficiency.


Sara Michaeli
Tel-Aviv-Yafo, Israel
Thank you for all suggestions from you.
In the last 1 month I've done a lot of trial at lab. Now the Carbonate is on level 60 g/L after we did freeze it out from the tank. so, I think Carbonate now is not the issue for the efficiency. The over additives happened in this case is over Make up (for thickness layer distribution) & Additive (for LCD), brightener & Water softener is consumed in properly.
Q. I did the plating in the Hull Cell using 1.5 A for 3 hours to remove the over additives, adjust again the additives to get the good Hull cell performance, it worked well. The efficiency increase again to almost normal like the new make up solution. then I did this trial in 5 liter bath volume, but after plating again with parts for several Ah with the additives replenishment, the efficiency become drop again, around 30-40%, back to the condition before. It is strange & really troublesome, any other suggestion how to keep the efficiency stable after bring back the additives level to the normal concentration?
- Jakarta, Indonesia
A. Firstly I think that you should place a heavy carbon pack on the solution to remove those organic additives that are in excess that are amenable to carbon. Secondly, I have found that oxidizing other organics and additives used in LCD boosters by treating with 0.1% by volume of sodium hypochlorite solution (commercial bleach)
⇦ bleach/sodium hypochlorite in bulk on
eBay
or
Amazon [affil links]
. If you use "household" bleach, use 1.0% by volume.
Of course, treat sample lots using Hull Cell. Always use 50% of the maximum used in the Hull Cell in the plating bath. More can be added later, but as you have learned removing excess is more difficult.
process supplier - Great Neck, New York
As additional data, now we are running the Zn content at 12-13 g/L, NaOH 140-150 g/L with ratio 1:12-13. (In the new make up solution Zn:NaOH is 10:120 g/L. With 2 ASD I could get 10 Micron in 30 minutes).
- Jakarta, Indonesia
A. You need to check your additive addition rate.If the solution plates well with lower addition rates of the make up additive then you need to lower how much you're putting in. A lower carbonate concentration will generally mean you need slightly lower additive additions to maintain the solution. Keep the zinc concentration at 12 g/l or higher. You may need to experiment with different concentrations and addition rates of the various additives to find the optimum figures. Does the problem get worse as the temperature increases? Is the temperature too low?
John Martin- Wales
Hi John, thank you for your suggestions. The additive content in the working solution is now being sent to the chemical maker & checked the concentration by them. So we are waiting the result. For the temperature because we use the chiller, so it is running at 24-25 °C as the TDS of the chemicals mention 24-28 °C. So the temperature is not the issue. Once our chiller is in trouble & the bath is running at 30 °C (that is our room temp.here) and it needs more brightener than normal -- 20-30% higher than the normal consumption.
Cahaya Metal - Indonesia
A. Dear Mr. Susanto,
I would like to give some suggestions as follow:
1. Since the cost to do new make up is rather cheap for Alkaline NCN Zinc, I think better don't waste your time. Why don't you try to do new make up and keep the old one for you and your supplier to do more evaluation work, if you wish.
With this new make-up just evaluate whether the carbonate rises so quick or not and how about the cathode efficiency, whether it can be maintain or not.
2. If the problem also comes back I think better call another supplier to try in your bath :-)
I believe that your current product is not stable or suitable for a climate like this.
Hope that you can make up your mind and you will find another solution for your problem.
Good luck,
Best regards,
- Semarang, Indonesia
Q, A, or Comment on THIS thread -or- Start a NEW Thread