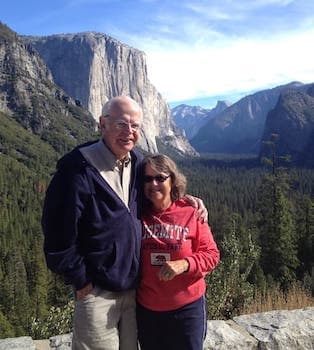
Curated with aloha by
Ted Mooney, P.E. RET
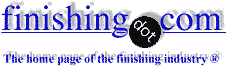
The authoritative public forum
for Metal Finishing 1989-2025
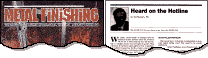
-----
Gold plating thickness required for connector
2005
Q. Dear sir,
I have some questions below:
1) We have found that our Au plated connector got corrosion like small grey/green/black spot,just after one month.(Note: Nickel thickness: 1.0 µm, Au thickness: 0.05 µm)? Is there material porosity problem? what is porosity control spec.?
2) We also found that one of Au plated connector got Copper migration from exposed base material (bronze base material) i.e., cutting point, but some of similar connector are without this problem?
3) I have noted that most of Au plated connector corrosion problem occurred on bronze type of base material, is it correct? Why?
4) How long is the shelf life for Au and Ag plated connector and relative storage conditions?
Please tell me how to solve /improve above problem
connector manufacture - SINGAPORE
A. Hi, LI
You need minimum 40-50 µ" ( Approx. 2 µm) of Nickel for Barrier between copper and Gold.
- Toronto, Ont., CANADA
2005
A. The small grey/green/black spot on gold plated connector appears to be due to pore corrosion. It could be due to the porosity in the Au and/or the Ni coating.
The AMP INCORPORATED Technical Report on ¡°Golden Rules: Guidelines for the use of gold on connector contacts¡± suggests the following points. I hope it will be of use to you.
Gold coating is applied over a high-quality underlayer such as nickel. A nickel underlayer can act as a: (i) pore corrosion inhibitor; (ii) corrosion creep inhibitor; (iii) diffusion barrier; and (iv) mechanically supporting underlayer. However, the nickel underplating must be continuous and have sufficient thickness to perform the particular function for which it is intended. As a general rule, a minimum thickness of 1.3 microns (50 µ") of nickel should be used. The choice of a suitable gold coating thickness depends on the degree of durability and environmental protection required by the application. In general, a 0.8 micron (30 µ") coating of hard gold over a minimum of 1.3 microns (50 µ") of nickel gives a degree of durability considered adequate for most connector applications. Thin coatings of 0.03 - 0.1 microns (1 - 4 µ") of hard or soft gold over nickel underplate should be used only for applications in which the risk of fretting is minimal. Increasing the thickness of a gold coating tends to decrease the porosity which reduces the contacts' vulnerability to pore corrosion. In general, a 0.8 micron (30 µ") coating of hard gold over a minimum of 1.3 microns (50 µ") of nickel provides exceptional environmental protection. Contacts coated with a thin hard or soft gold coating on the order of 0.03 - 0.1 microns (1 - 4 µ") in thickness over a nickel underlayer can be used in benign environment applications.
Increase in the thickness of the nickel and gold coatings will reduce the porosity and help avoid the problems due to pore corrosion.
I believe that the migration of Cu observed in some connectors could be due to the lack of thickness of the Ni underlayer in those contacts.
The problems due to pore corrosion and diffusion of elements from base metal are not specific to bronze and it could occur on other types copper alloys also as they depend on the coating thickness of both Ni and Au.
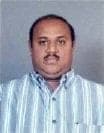
T.S.N. Sankara Narayanan
- Chennai, Tamilnadu, India
(ed.note: The good doctor offers a fascinating blog, "Advancement in Science" )
2005
Q. Dear sir,
I have received 2 replies, but following issues are still my doubt:
1) How long is the connector shelf life for different Au plating thickness, i.e., 0.03 µm, 0.05 µm min,0.1 µm min, and 0.2 µm min (Note: Ni undercoating is 1.3 µm min); how about Silver plated connectors? What is standard storage conditions, i.e., temperature, humidity?
2) Can you tell me base material porosity control spec. i.e., size, density etc. If the pore size of raw material is over 2 µm, is it causing corrosion problem? how thick of Au/Ni plating can cover this bigger pores?
3) Some of Ag plating got brown stain at scratched area after moulding under 100 °C, but the scratch did not reduce Ag/Ni thickness (Ag: 5~6 µm, Ni: over 1.4 µm),but some is okay with same scratches (use same M/C & same process, why? Even under room temperature, also got the same problem? I hope to get detailed explanation! Thanks!
Best Regards,
- Singapore
2005
A. The shelf life of the connectors depends on storage conditions.
The following specifications will be of some help to you.
ASTM B488: Electrodeposited gold coatings for engineering use
MIL-STD-1344: Test methods for electrical connectors
- Method 2016- Durability
- Method 1005.1- Temperature life
- Method 1002.2- Humidity
- Method 1001.1- Salt spray
ECA EIA 364-09: Durability test procedures for electrical connectors
ECA EIA 364-31: Humidity test procedure for electrical connectors
ECA EIA 364-26: Salt spray test procedure for electrical connectors
ECA EIA 364-17: Temperature life with or without electrical load procedure for electrical connectors
The copies of MIL Standards can be obtained from:
DODSSP Standardization Document Order Desk
700 Robbins Avenue, Building 4D
Philadelphia, PA 19111-5094
Web site: http://astimage.daps.dla.mil/online/ ^ https://quicksearch.dla.mil/
Electronic Industries Alliance (EIA) standards can be obtained from:
Electronic Industries Alliance (EIA)
2500 Wilson Boulevard
Arlington, VA 22201-3834
Website: http://www.eia.org/
ASTM specifications:
Website www.astm.org
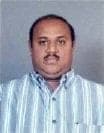
T.S.N. Sankara Narayanan
- Chennai, Tamilnadu, India
(ed.note: The good doctor offers a fascinating blog, "Advancement in Science" )
Q. I am having the exact same problem as Li but with one exception, I am plating Ni at 2 µm and above, Au at 0.5 µm and above but I am seeing the black/green spots just after 3-4 days of plating.
The parts are kept at room ambient.
Another question that I have is that what actually happens at the green/black spots? Is that the base metal (mainly Cu) creeping out towards the Ni and Au layers?
Kindly advise. Thanks!
- Penang, Malaysia
2007
Q. On a Gold plated electronic connectors with 2.5 µm Ni layer and 0.76 micron of gold if you find two three brown spots [not visible to unaided eye] after one week or ten days or at the customers end:, What decision you take:
1.On acceptance of the connectors in house or at customer end
2.If not acceptable what is the criterion for acceptance on the present scenario
3.What the standard says
plating shop employee - Chennai, India
April 12, 2009
Optimized thickness of Gold on copper to avoid corrosion in fuel cell
Q. Hi,
I am an young researcher in India on Fuel cells. I am an Electronics Engineer. I am designing current collector plate which is basically copper. But bare copper is prone to rusting. So I need to coat it with a layer which has high conductivity but also corrosion resistance. In this way, I have chosen gold plating. Now my question is, what is the minimum thickness of gold plating required to avoid corrosion.
Kindly help me.
Thanks in advance
Research Assistant - India
April 5, 2016
A. Hi Bharathi. Assuming there is no wear, then you need a thickness sufficient to have no porosity or pinholes, and to not diffuse into the copper too quickly. This is probably best met by nickel plating followed by gold plating as described by TSN Sankara above.
Regards,
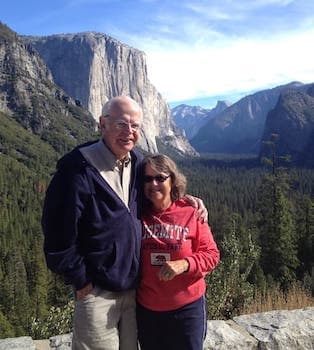
Ted Mooney, P.E. RET
Striving to live Aloha
finishing.com - Pine Beach, New Jersey
April 2016
A. Hi Barathi
There is plenty of good advice and precedent for gold on electronic connector, etc., but you have a special application and will have to determine the best thickness for yourself. To prevent migration of the gold, 2 microns of nickel undercoat is reasonably standard.
I would expect the gold to be about 5 microns but, as Ted says, porosity is the main criterion. This is not always easy to achieve on a regular basis. Your quality control should include a porosity test ( dimethylglyoxime )
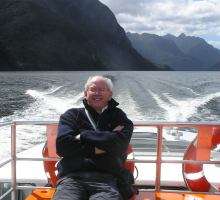
Geoff Smith
Hampshire, England
April 9, 2016
Q. Need to choose the optimum gold plating thickness for SS 304 material that is used as coin battery contact connector of watch.
Narasimha NarasimhaConzumex - Bengaluru, Karnataka, India
June 28, 2018
? Hi Narasimha. It's hard for me to suggest how thick the gold needs to be for functionality, when I don't understand why you even need it gold plated rather than nickel plated anyway :-)
I could be wrong, but I thought nickel was adequate for battery contacts, and the more so if sealed inside a watch. Can you explain or comment?
Regards,
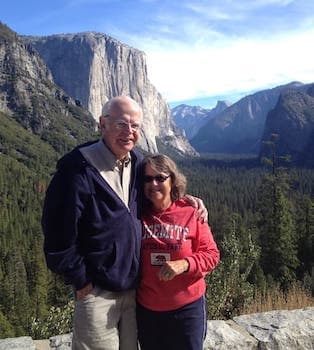
Ted Mooney, P.E. RET
Striving to live Aloha
finishing.com - Pine Beach, New Jersey
September 2019
Q, A, or Comment on THIS thread -or- Start a NEW Thread