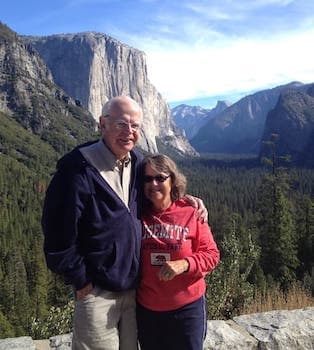
Curated with aloha by
Ted Mooney, P.E. RET
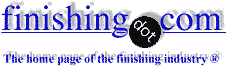
The authoritative public forum
for Metal Finishing 1989-2025
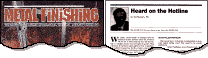
-----
NaOH stripping of chrome damage question
2005
I am an engineer in Tennessee. My company hard chrome plates our injection tools for wear resistance. Part dimensions are vitally important to our process and the injection cavity must not be damaged i.e. the need for chrome.
Out injection cavities are made from Vanadis 4 (powdered metal). This is a hardened tool steel. We electrostrip our tools with NaOH when they show wear. Our stripping process is as follows:
- Approximately 6 oz/gal NaOH
- Stripping solution is at room temperature
- Solution is changed approximately once every two months - the stripping solution becomes inactive after one to two months and needs to be changed
- Various size tools result in various times to be stripped - the largest tool may take 1 hour to fully strip
- The rectifier is usually set to 5-6 V and the tool to be stripped is approximately 20 inches from the cathodes
My main question deals with tool damage. Lets say a tool is put in the strip tank and is stripped after 15 minutes. But after the tool is completely stripped of chrome, the operator goes to lunch for 30 minutes. Is it possible to damage a hardened steel tool if left unattended in the strip tank? I didn't think it was possible especially with the short stripping times we're dealing with. Any info is appreciated.
Thanks,
William
- Morristown, TN, US
I confess that I am absolutely ignorant about that particular alloy's behavior, so please excuse me, but can you just tell the operator to cut the current and put it back when he returns after lunch or whatever? I've never dealt with that alloy but it would certainly amaze me to find out it is damaged by a 30 min. immersion in caustic. Plain carbon steel is used to contain caustic solutions for years.
Guillermo MarrufoMonterrey, NL, Mexico
2005
I agree with the above. Have you experienced any damage from the stripping operation?
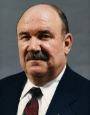
Daryl Spindler, CEF
decorative nickel-chrome plating - Greenbrier, Tennessee
2005
2005
We have a few die cavities that have experienced some "growing" over the past year or so i.e. the injected part thickness is increasing over time.
We do blast with 300 grit aluminum oxide and I'm almost sure our die cavity wear is coming from this operation. I'm trying now to rule out all other possibilities.
Thanks for the responses!
- Morristown, TN, US
Q, A, or Comment on THIS thread -or- Start a NEW Thread