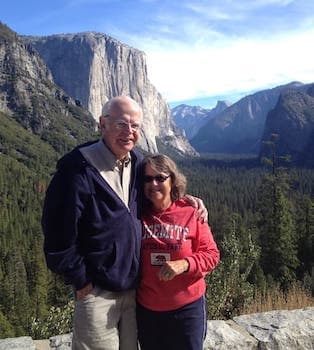
Curated with aloha by
Ted Mooney, P.E. RET
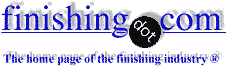
The authoritative public forum
for Metal Finishing 1989-2025
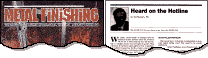
Thread 382/96
How to Polish Hot Rolled Steel Sculpture
Q. Hi,
I'm creating a sculpture out of hot rolled steel and I need a mirror finish. I know it'll rust, so I plan on coating it with clear coat (the stuff that goes on cars). I'll be sand blasting it with fine
[adv: Black Beauty on
eBay or
Amazon [affil links]
(to remove the mill scale) and then using 3M Scotch brite pads, after which I will buff with Mothers. It's a labor intensive process, I know, but is there a more effective way to obtain the finish? What products do you recommend? Thanks so much.
art student - Odenton, Maryland
2005
publicly reply to Christine Pak
A. I'm sorry to say that what you're doing is probably best for a good solid finish. The only thing I could add is get an orbital sander and use finer and finer pads, you get get up to about 600-800 grit which will approach your mirror finish and save your elbows a good bit of grief. Also I would suggest getting an angle grinder
⇦ this on
eBay
or
Amazon [affil links]
, felt buffing wheels (for a bench grinder, you can make them fit if you're careful), and jeweler's rouge
⇦ this on
eBay
or
Amazon [affil links] .
It will make polishing go much faster than buffing the entire thing (depending on size).
blacksmith - Shiloh, North Carolina
publicly reply to Marc Banks
A. After you get the surface fairly smooth as Marc suggests you could have it copper, nickel and chrome plated for a shiny, rust free finish.
Neil BellAlbuquerque, New Mexico
publicly reply to Neil Bell
A. I have some experience polishing some of the Trova sculptures. Although these are stainless steel the procedure is the same. Disc sand and orbital sand to shape.Using finer sand disc until you get to your desired finish. Then use close sown sisal buffs on angle and straight polishing hand tools to start getting the color (shine). The final step is color buffing with a soft cloth buff using a white chrome rouge. Depending on your skill level, endurance and how high of a standard you set for yourself it could take a few weeks or years.
Good Luck,
Frank
- St. Louis, Missouri, USA
publicly reply to Frank DeGuire
Q. I too am trying to achieve a mirror finish on hot rolled mild steel. Unfortunately, I don't have access to sand blasting equipment. I'm working with an 18 gauge sheet 2 feet by 3 feet. To remove heavy rust as well as mill scale I've started by using 36 grit belt sanding, followed by 80 grit, 120 etc. Trying to get rid of the striations and parallel scratches caused by the belt sanding has proven to be quite a problem. I'm switching over to an orbital sander with grits going up as high as I can find (400?). By the time I switch over the scratches appear too deep to get rid of. I would very much appreciate any suggestions.
I'm an older guy who has just recently begun welding and sculpture. Having produced a few small pieces has been extraordinarily exciting. I'm planning larger pieces to follow. Needless to say, I'm completely involved and quite passionate about finding a possible art form so late in life (79).
One further issue, apparently the heat from the belt sanding has caused the steel sheet to warp in the center. Again, I would appreciate any suggestion.
- Carmel, California
2006
publicly reply to Alan Nixen
A. First, try and do as much polishing with wet paper as possible. Don't flood it, just keep it wet, the paper will last a lot longer and cut better. Lay it flat. Start with a coarse grit, finish the entire area with the strokes all going the same direction. Flush the surface, then go to the next finer grit going perpendicular to the first strokes. Once all the cross marks are removed, go to the next finer grit. This is how you make samples to examine under a microscope, so I know it will make a mirror surface. Keep getting finer until you get to 800 grit paper (yeah, this is going to be a lot of work). Once you get that done, see if you can find some 2 micron alumina powder; Buehler and Leco sell it for metal sample preparation. Find someone that repairs pool tables and get a piece of billiard cloth. Mix some of the powder with water to make a thin paste, get a wood block that fits comfortably in your hand, wrap the block in the cloth, put some paste on it and start polishing.
Your biggest problem is going to be how fast you can do this, since steel rusts. Keep all of the surface except the area you are polishing well oiled. Wipe off the oil and clean the work area with alcohol before polishing to avoid messing up the alumina, then re-oil once you are finished. Once you do all this work, how do you plan to keep it from rusting?
- Lancaster, Texas
publicly reply to Tom Howard
A. I have a little experience with steel. In reading the procedures laid out by each, I was reminded of a procedure I used to get rid of oils and scale on pieces I was working with. I had purchased some oxalic acid
⇦ this on
eBay or
Amazon [affil links]
for cleaning cedar shakes. A metals instructor friend of mine used to use vinegar
⇦in bulk on
eBay
or
Amazon [affil links] , but it was too slow. I decided to try the oxalic acid which I determined was somewhat stronger than vinegar. To my surprise, the metal cleaned up to a bright finish almost as though it had just come from the steel mill. This prevents the cuts in the metal caused by starting with course sandpaper. It would be important to start with metal that is not pitted with rust.
Good Luck!
- Chatsworth, Georgia
2007
publicly reply to Randall Richards
A. Try using 1/ or 1/4 hard material this is a cold finished product but the rolling to get temper brings base material to a bright finish. Laphm and Hickey , precision steel are 2 that I know that handle this material.
Tony Olszewski- Palatine Illinois
May 4, 2010
publicly reply to Tony Olszewski
Q, A, or Comment on THIS thread -or- Start a NEW Thread