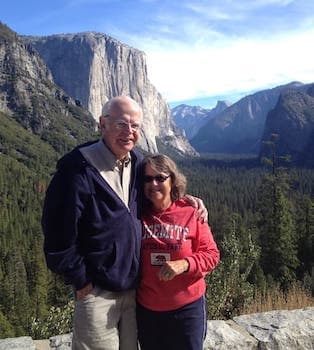
Curated with aloha by
Ted Mooney, P.E. RET
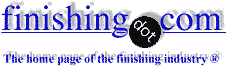
The authoritative public forum
for Metal Finishing 1989-2025
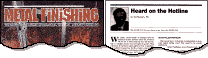
Thread 382/49
Internal Plating of Mild Steel 35 mm Tube
2005
I work for a company manufacturing tubular components for the automotive industry, specifically fuel filler assemblies. We currently have a new project with a major global manufacturer. The part in question is a 1 m long, 35 mm diameter, 1.2 mm wall, mild steel fuel filler with a Hexavalent Chromium free Zinc Nickel Alloy coating both internal and externally.
Our plating process involves the tube being mounted on a hanging jig with an internal nickel anode connected to the jig and passing through the bore of the fuel filler. Our anode resembles a 1.1 meter long tightly coiled spring approx. 10mm diameter. This spring is then shielded in a rubber sheath to prevent shorting between anode and part. This sheath has holes drilled in it approx. 1/2" apart. This jig and part is then run through our process of tanks to achieve the required plating thicknesses, which it does.
The problem we have is that due to the nature of the part which has very tight bends and turns, the anode is contacting the inside wall at a very high pressure. At this point of contact the rubber sheath is compressing and forming a footprint that prevents plating from occurring. When one of the parts is sectioned 4-5 of these footprints are visible along the length of this 1m long tube.
Does anyone have any suggestions on alternate anode designs, or any assistance that would be helpful in eradicating these footprints as they are unacceptable to our customer.
Tubular Component Manufacturer (Primarily Automotive) - Avonmouth, Bristol, United Kingdom
publicly reply to Alex Mines
Although you provided quite a bit of information, most people would have to see the part to really understand the problem and thus the options.
Possibly you could put a number of plastic X or cross spacers on the anode that were say 25 mm. these would have a small contact point with the part and might be enough to prevent the contact or bad anode spacing IF enough of them were placed at critical points. I have used star shaped spacers, but crosses should work fine, especially if the ends were concave so they actually had 2 tiny contact points per cross leg.
- Navarre, Florida
2005
publicly reply to James Watts
I'd go for electroless nickel.
Then you don't need the auxiliary anode.
polishing/plating - Belfast, Maine
2005
publicly reply to Steve Clark
Q, A, or Comment on THIS thread -or- Start a NEW Thread