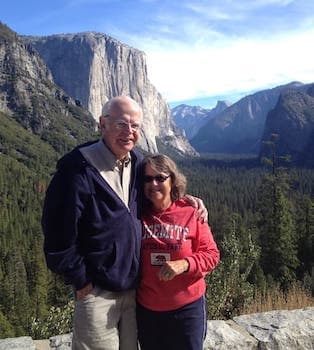
Curated with aloha by
Ted Mooney, P.E. RET
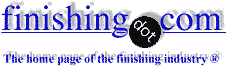
The authoritative public forum
for Metal Finishing 1989-2025
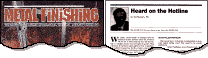
Thread 382/40
CHROMATE CONC. TO PASS 90 HOURS SALT SPRAY IN G. I. SHEET
OURS IS CONTINUOUS GALVANIZING LINE. WE MAINTAIN PASSIVATION BATH CHROMIC ACID HEXAVALENT CONCENTRATION AS 5-7.5 % . OUR CUSTOMER REQUIREMENT IS 25 mg/M2 LAYER OF HEXAVALENT CHROMIC ON EACH SIDE OF SHEET AND PASSES 60 HOURS SALT SPRAY TEST. SO, PLEASE TELL US HOW TO MEASURE CHROMIC ON SHEET IN mg/M2 AND WHAT PASSIVATION BATH CONCENTRATION WE SHOULD MAINTAIN.
NITIN BHUSANGEJAI CORP LTD. ,NANDED MAHARASHTRA, INDIA - NANDED MAHARASHTRA, INDIA
2005
publicly reply to NITIN BHUSANGE
2005
In general (batch) galvanizing a sodium chromate concentration of
200 ppm (light yellow solution at 0.02%) to 1,000 ppm (light orange solution at 0.1%) is commonly used. By adding acetic acid
⇦ this on
eBay
or
Amazon [affil links] the chromate coating is virtually colorless. Drips of chromate on the bottom of the products are a pleasant light sky blue color. The pH of the solution MUST be kept at the proper level by titration (using a pH indicating dye; pH meters and paper are useless) using 1/100 HCl. pH adjustments are made with hydrochloric acid. The resulting chromate treatment easily passes a 40 hour salt spray test. Sheet galvanizing is more difficult to pass a salt spray test because the aluminum content in the zinc is so much higher. When the conductivity
(due to zinc, ammonium, and chloride ions) reach a certain level the solution must be changed out. Chromium trioxide (CrO3)is NOT a good source of hex chrome because it badly stains the zinc coating.
Regards,
Galvanizing Consultant - Hot Springs, South Dakota, USA
publicly reply to Dr. Thomas H. Cook

Q, A, or Comment on THIS thread -or- Start a NEW Thread