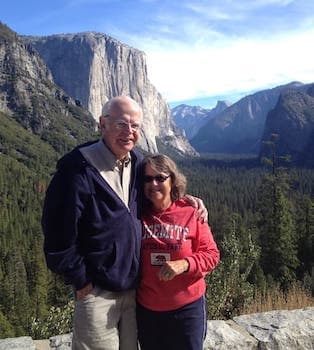
Curated with aloha by
Ted Mooney, P.E. RET
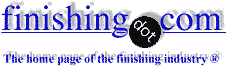
The authoritative public forum
for Metal Finishing 1989-2025
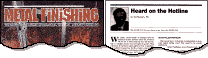
-----
Finishing aluminum with rotary brass brush - what is happening?
2005
Q. I am finishing 5 mm thick aluminum extrusion and 3 mm plate.
After machining, I work out the scratches (mostly from clamping during machining and handling) with a sisal wheel and black wax.
When I take a brass rotary wheel to the surface, it goes through various stages.
First, with light pressure, the brushes kind of skip and skid creating various incidental marks.
Second, as I lightly increase pressure to "seat" the brush in the aluminum, the brushes start to cut. With this very light pressure and constant movement (e.g., I do not let the wheel stay in one place over the metal), I get the finish I desire, which is a very finely scratched satin-y finish.
However, if I go over the area too many times (perhaps in an attempt to blend the lines), or if I stay in one area too long, the surface begins to change from a fine satin in which the scratch lines are straight to a surface covered with a very fine orange peel. Additionally, the surface is very hard.
Continuing to stay over the surface the orange peels grow and become super hard.
By super hard, I mean that to remove them, I (when I have had the initiative in the past) had to step back to 40g sandpaper.
What I ideally like is the very first fine satin.
On the other hand, I also like the surface that occurs when the orange peel is "just" starting to form. That is to say the satin is not quite so fine, but made up for by the more durable surface.
So, now the questions:
1) What is happening to the metal? A work-hardening? Small-particles sticking to the brush and at a certain localized surface temperature welding themselves back on? Little tiny green men so small I can't see?
2) How can I *creatively* control the process? Of course, the easy answer is "buy a machine on which you can control the height of the brush and the feed rate." However, I am a foreigner in Europe trying to start a business, and I need to be creative where possible (instead of throwing money at the problem). Or in other words, are there elements I can control, such as using a fluid or gel on the metal? Changing the RPMs (it seems that ultra low RPMs might solve the problem, but before going in this direction I was hoping to understand the dynamics a bit better).
So, thanks in advance for any advice.
Regards from suddenly rainy Barcelona,
Shon Shampain
Aluminum enclosures - Barcelona, Spain
A. Hello, Shon. I may be misunderstanding you, but you may be misunderstanding scratch brushing. So let me make it brief and just say that scratch brushing usually isn't done with brass brushes, despite what you might assume from the name ... but with one very quick "scritch" of sandpaper / scotchbrite on a large belt sander.
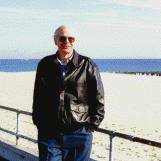
Ted Mooney, P.E.
Striving to live Aloha
finishing.com - Pine Beach, New Jersey
2005
2005
Q. Yes, I am no doubt using the wrong name for the process.
Sorry for the confusion.
However, I am still interested in the dynamics of what is happening to the aluminum. I wanted to further point out that the exact medium I use is not important, that is to say that I can generate the orange peel with:
- a rotary sanding pad with fine grit paper (120 or 150)
- a rotary disc (the type with the velcro on it) with a circular cutout of coarse or fine scotchbrite pad attached
- a brass rotary brush
When I started the first process I explored was a rotary sanding pad. Of course, the soft aluminum quickly loaded the pad and I was convinced that I was spot welding the aluminum particles back onto the workpiece. However, when I got the same results with rotary scotchbrite (the scotchbrite will become locally discolored, but certainly there is ample room for the aluminum particles to clear out) I became more convinced that some kind of work-hardening is going on.
I have searched rec.crafts.metalworking, and performed all kinds of permutations of google searches, but I haven't got any kind of useful information so far. I also saw a letter on this forum from a guy who was buffing (I think an auto) part for a customer, and the part had scratches that he had to revert to sanding them out, the piece "work hardened" and then the surface finish was not what the customer expected.
So, I suppose a more concise statement of the question would be:
Will aluminum work-harden when it is worked with a rotary tool, and if so, under what conditions? And what can be done to prevent it?
(E.g. if it is a function of heat, will fluid prevent it.)
aluminum enclosures - Barcelona, Spain
A. Not only could you be work hardening it, you could also be melting it (at localized points). Using a proper friction reducing agent will help in both directions. There are synthetic fluids but vegetable cooking lard will do a nice job and be totally safe.
Guillermo MarrufoMonterrey, NL, Mexico
2005
2005
Q. Here is some more information on the topic:
I finally took some time to purposefully create a whole panel on this "cowhide" effect I took a rotary brush and performed a number of passes on an otherwise finished panel. First, some pictures: cowhide
panel
For reference, the cap screws in the 2nd picture are M3. The pictures are reasonable representations, but not great.
1) As far as SFPM, I used a 4" diameter brush at 3000RPM. I think that a lower SFPM will yield a smaller grain.
2) The finish in and of itself is really not bad, appearance wise.
3) Between the grains, as far as I can see, it is very flat and smooth. Unfortunately, there are areas of greater grain concentration and areas of lesser grain concentration. Because the latent background is smooth, the areas of lesser concentration appear wet and the areas of greater concentration appear more opaque. Trying to blend the areas with a hand tool is a lesson in futility, because it seems there is a point in which the grains become too big to further melt, and no amount of agitation with the brush will produce a different appearance. A more systematic application, or a machine adaptation should give more consistent results.
Other than that, I would be interested if any other manufacturers use this type of treatment. I have never really seen it anywhere, and it appears pretty easy to fabricate and generally somewhat functional, for what it is, as well.
Cheers,
Shon Shampainaluminum enclosures - Barcelona, Spain
Q, A, or Comment on THIS thread -or- Start a NEW Thread