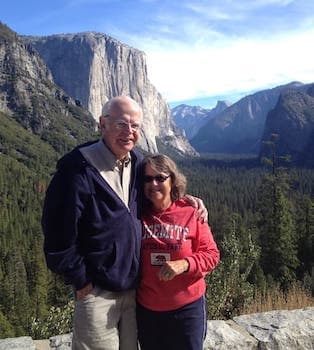
Curated with aloha by
Ted Mooney, P.E. RET
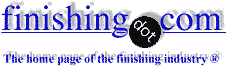
The authoritative public forum
for Metal Finishing 1989-2025
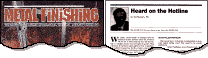
Thread 382/12
Cyanide Zinc Electroplating Problems

Q. I have a small cyanide zinc plant of 100 ltrs, non barrel process ... but now I want to convert it to 300 ltrs with barrel processing, is it possible that a barrel can run in cyanide zinc plant? Or acid zinc and cyanide zinc both plant can set barrel?
Rajib mondalSelf employee - KOLKATA
July 20, 2023
publicly reply to Rajib mondal
A. Hi Rajib,
a few decades ago cyanide zinc was the only practical zinc plating method, so barrel plating is certainly possible with cyanide zinc. These days acid zinc and alkaline non-cyanide processes are very practical as well.
300 liters is still rather small, but can certainly be done. But if you are considering 'commodity' plating/pricing you would find yourself not being competitive with barrels of that size. About 800 liter tanks would be required for 14" x 30" barrels, which are about the smallest practical size for commodity plating; but if you can stay in the 'specialty plating' zone, you'd probably be better off :-)
Luck & Regards,
Ted Mooney, P.E. RET
Striving to live Aloha
finishing.com - Pine Beach, New Jersey
publicly reply to Ted Mooney
Hello, Rajib,
I've been barrel plating small door lock parts for a few years now with cyanide zinc without problems.
There are some points that i've learned with practice that I think you should pay attention to:
-since the current density is usually lower in barrel plating, depending on the shape of your parts you may have problems plating in recesses and sharp edges. Raising the zinc content of the bath has solved this problem for me.
-anodic efficiency is considerably higher than the cathodic efficiency, therefore the zinc content of the bath tends to rise if you are working with only zinc anodes. Alternating between steel and zinc anodes helps controlling this variable (does this happen with rack baths too?).
Kind regards,
- Nova Friburgo, Rio de Janeiro, Brasil
publicly reply to Pedro Franco
A. Thank you for answering, Pedro.
Yes, increasing zinc concentration can happen in rack plating as well. In alkaline non-cyanide plating, "generation" tanks are pretty common (inert anodes are used in the plating tank and a side tank is employed where zinc anodes dissolve into the caustic, and a limited amount of this concentrated zinc solution is metered into the plating tank). I don't know if generation tanks are ever used in cyanide zinc plating.
Luck & Regards,
Ted Mooney, P.E. RET
Striving to live Aloha
finishing.com - Pine Beach, New Jersey
publicly reply to Ted Mooney
⇩ Related postings, oldest first ⇩
Q. I am a metallurgical engineer. I am going to have a cyanide zinc electroplating industry.my process stages is:
Oil cleaning-acid washing (hydrochloric acid )-cold rinse-zinc bath-cold rinse-chromating bath (black)
My bath composition: zinc cyanide-sodium cyanide-NaOH-sodium sulfide and brightener.the anode is zinc (99.995%).
My problem: current density is .05-.3 and time of zinc coating process is 40 min, but in whole of this range, colour of steel specimens convert to grey and in black chromating thats colour convert to brown stains. Now my question is: whether current density and time is suitable for this process?
- Tehran, Iran
2005
publicly reply to Hashem Mehrabanian
A. Dear Hashem
Try your Zinc Plating process like this
Degreasing - acid (HCl) pickling - Cyanide (NaCN)dip - Zinc plating - Cold rinse - 1% HNO3 dip- Passivation - dry
Hope this will eliminate your problem.
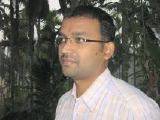
Jose George
Cochin, Kerala, India
publicly reply to Jose George
A. Dear Mr Hashem;
Apart from decreasing, acid pickling, in zinc plating metal to cyanide ratio and metal to caustic ratio is most important. ideal composition are metal 34 gm/lit cyanide 90 gm/lit total caustic 75 gm/lit. Also use of good brighteners and purifier will increase the quality of deposit and good brightness. Use good quality anodes, i.e., zinc 99.999% special high grade is must. Regulated current density 25 to 30 amp per square feet is required. To achieve good bright finish plate 20 to 30 minutes at the above current density to achieve 10 micron thickness in rack plating.
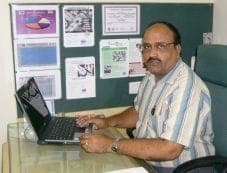
P. Gurumoorthi
electroplating process chemicals - Chennai, Tamilnadu, India
publicly reply to P. Gurumoorthi
A. Hi,
Give a activated zinc dust
⇦ this on
eBay or
Amazon [affil links]
treatment to cyanide zinc bath, also put some purifier in the bath, maintain a medium cyanide bath with little high caustic soda ⇦liquid caustic soda in bulk on
Amazon [affil link]
, for black passivation you need to build up a good thickness around 7 - 8 microns, use double dip for passivation, I mean dip in passivation made of lower concentration, then a final passivation dip , increase the additive containing silver content, maintain the pH given by your supplier specs.
Regards,
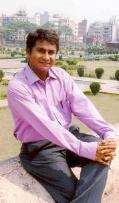
Praveen Kumar
plating process supplier
Mumbai, India
publicly reply to Praveen Kumar
Q. Hello!
I am a metallurgy engineer. I have a cyanide zinc electroplating industry.my process stages is:
Oil cleaning-acid washing (sulfuric acid)-cold rinse-zinc bath-cold rinse-chromating bath(blue-yellow-green-black). My bath brightener I buy from Canning Company.
My bath composition: zinc cyanide-sodium cyanide-NAOH.the anode is zinc(99.99%)
1. the problem is:my specimens is very good after cyanide zinc bath but in the rinse stage the pieces is dark and the brightening is lost. What is reason?
2. the problem is:the anode color in the bath change to brown or black blue.what is this.
3. the problem is:the specimens is very good in zinc bath and in the chromating bath but after one or two weeks the adherent of the coating is lost and separate from surface and cause blistering in the coating surface.
Amir Khakzad- Tehran, Iran
2005
publicly reply to Amir Khakzad
A. Canning is now a part of Macdermid who have an extensive network of technicians. As the brightener supplier they should be able to help you, and should be your starting point.
John Martin- Cardiff
publicly reply to John Martin
A. 1. Use a dip of 1% HNO3 after zinc plating and before chromating, rinse before and after.
2. That's normal.
3. Blistering is caused by bad cleaning before zinc plating or too much brightener in zinc-bath, check if you are inside spec.
Good luck,
- Lucerne, Switzerland
publicly reply to Marcus Hahn
Q. Dear all ...
My name is Sutry. I'm a technical engineer for zinc electroplating in Indonesia, and I have a little problem:
I have customers who use cyanide zinc barrel plating.
They have a problem of cloudiness in the plating.
If I add brightener in Hull Cell 1A 10 minutes, black stripes will appear in low current density area.
If I don't add brightener, black stripes do not appear, but plating is not bright.
Can you give me some recommendation?
chemical supplier - Jakarta, Indonesia
April 1, 2011
publicly reply to Sutry Rockstar
Delayed black spots/color change to cyanide zinc trivalent plating 48 to 96 hours later
Q. We are taking the Zinc trivalent plating parts with iridescent passivation. We face an issue of colour change of the plated parts after one week ... in many cases even after two days.
If we check the salt spray life which is required 72 hrs NSS, that always comes okay but our parts get rejected aesthetically. Our parts are Zinc pressure die cast parts with the base material of Zamak 3/Zamak 5 (zinc composition). We are doing cyanide plating. Please suggest how we can come out from this issue.
If required any additional information I can provide you.
Pankaj Tyagi
Buyer to Zinc trivalent plating - Noida, UP, India
August 13, 2014
publicly reply to Pankaj Tyagi
A. Hi cousin Pankaj. Black spots and color change in zinc plating are such a common problem that we have almost countless threads here about it. Cyanide "bleedout" is a very common cause of spotting and discoloration. But one issue is that "black spots" may mean pits, barrel printout, cyanide bleed-out stains, areas where chromate didn't take, spots in the plating, spots in the passivation, etc. I think a good next step would be to send us pictures of the defective parts to try to reduce the confusion of readers inferring a different meaning from black spots and discoloration than you intended.
Also: are these parts rack or barrel plated? Are the plating and passivation processes proprietaries or home brew? Do you inspect the castings before plating, and have rejection criteria for cold shuts, pits, porosity and other defects? Could packaging materials play a part, or does the defect appear before packaging? Thanks!
Regards,
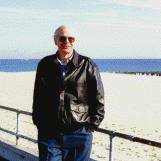
Ted Mooney, P.E.
Striving to live Aloha
finishing.com - Pine Beach, New Jersey
publicly reply to Ted Mooney
Q. I am starting a 15 kg barrel cyanide zinc plating. Problem is sometimes material comes Okay and sometimes material comes Not okay. Which process to use, please suggest.
Power is 5 to 8 v.
NaCN 38 kg. NaOh 40 kg. Zinc oxide 18 kg.
Bath capacity 380 liters.
heat engineering - Surat, Gujarat, India
April 24, 2015
publicly reply to Gosai Jaydip
Trivalent blue passivation over cyanide-zinc: Need 96 hours Salt Spray
Q. I have an issue with consistently achieving 96 hours of SST to white rust using a trivalent blue passivate over cyanide-zinc (8-12 microns). I have used multiple trivalent blues from multiple suppliers who have all guaranteed I should get 96+ hours. I have tested each passivate using panels and have not consistently achieved 96 hours. Is there something I need to consider since the deposited metal is cyanide-zinc? I ask that because when I run trivalent black over cyanide-zinc, I use a caustic-bleach solution before the nitric acid pre-drip. This helps breakdown the cyanide and results in a more blacker finish. Any thoughts on how to achieve better corrosion protection in this scenario?
Thank you.
- Cleveland, Ohio, United States
June 23, 2017
publicly reply to Dustin Shoaf
Q. I have a 12 barrel zinc cyanide plating line. My problem is every hour I can only get 8-9 barrels of good production. What seems to be the problem?
Jon cardenas- manila, philippines
July 11, 2018
publicly reply to Jon cardenas
A. Dear Jon,
If you want to improve your productivity in your line. Improve process cycle time to meet your customer specifications.
If you need to get more output add up one more section in your zinc plating tank. It will reduce the process time.
Example
One Cell Plating cycle time: 30
Two cell plating cycle time: 15
three cell plating cycle time: 10
To achieve 12 barrel per hour your cycle time should be 5 minutes.
It requires 6 cell plating.
Thanks
- Electronics City, Bangalore, India
publicly reply to P Karthikeyan
Q, A, or Comment on THIS thread -or- Start a NEW Thread