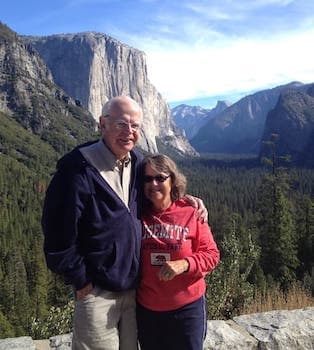
Curated with aloha by
Ted Mooney, P.E. RET
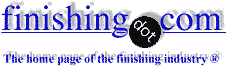
The authoritative public forum
for Metal Finishing 1989-2025
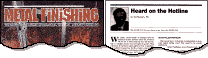
-----
EARLY TOOL FAILURE
WE USE H-13 ION NITRIDE COATED PUNCHES IN A WARM FORGING OPERATION. ONE PUNCH MAY RUN 9k pieces. AND THE NEXT ONE RUN 47k pieces. DOCUMENTATION SHOWS THE PARTS WERE MANUFACTURED FROM THE SAME STEEL BUT MACHINED AND COATED AT DIFFERENT TIMES. IT APPEARS SOME OF THE PUNCHES WERE COATED WITH PARTS THAT WERE A MUCH LARGER MASS, ( 1 1/2 O.D. VS 3 1/4 O.D. ). WOULD THIS DIFFERENCE IN SIZE DURING THE COATING PROCESS CAUSE A PUNCH TO FAIL EARLY?
JIM GARDNER- ASHLAND, Ohio
2005
2005
TiN is very sensitive to deposition temperature. If the temperature is too low, the coating will either lose hardness or be overstressed and not function as well. Changing the load in the chamber could affect the deposition temperature, depending on the system design. It is also possible that the coating thickness was affected, i.e., the larger parts reduced the deposition rate for your tools, so you wound up with a thinner coating. Of course, the coating could have been contaminated.
Color is a pretty good measure of TiN quality. It should be a nice bright gold, a little to the yellow in tint. If the coating was put down at a low temperature, the TiN would tend to be darker, more toward a brownish hue. If it was contaminated, it would also be darker, but toward a blue or black tint.
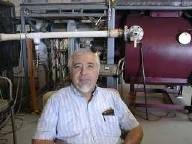
Jim Treglio - scwineryreview.com
PVD Consultant & Wine Lover
San Diego, California
Q, A, or Comment on THIS thread -or- Start a NEW Thread