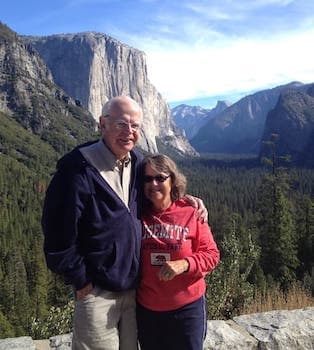
Curated with aloha by
Ted Mooney, P.E. RET
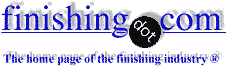
The authoritative public forum
for Metal Finishing 1989-2025
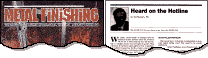
-----
Electroless nickel on aluminum (pitting problems & pinholes)
Q. A lot of our business has us doing a .002/.004" deposit of EN on aluminum substrates, which we've been doing, for decades. With that, and the understanding that pitting can occasionally be a part of the process, we have a dilemma involving heavy pitting in the EN.
Substrate material is 6061-T6 and the process is pretty much as it has always been (diamond machining substrate and cleaning and plating per standard industry specs like AMS2404, MIL-C-26074
[⇦ this spec on DLA]) yet on these particular substrates we are getting excessive pits. All others plated in this bath are fine, previous optics have been fine, just the two failures and they have been repeated, numerous times. We've chemically stripped, prepped and re-plated. We've re-machined, prepped and re-plated and we've modified in-tank fixturing but still ... pits. Any suggestions?
What surface and/or material anomalies could cause this? We've used 6061 quite often and the plating process has been in-place forever...really at a loss here.
Aerospace - Rochester Hills, Michigan, U.S.A.
2005
A. It would be helpful if you would identify your preplate processing. Also, how many turnovers do you get from you EN bath? Does the problem seem to be above 5 MTO's?
Gene Packmanprocess supplier - Great Neck, New York
2005
A. Hi,
I think your problem comes from the machining operation. If you not take wrong of what pitting or step plating in the EN deposit. To me, your problem looks like you are building a bridge over the aluminum area when you machining when you say that other things you plate are without pitting.
Regards,
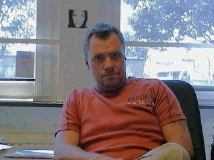
Anders Sundman
4th Generation Surface Engineering
Consultant - Arvika,
Sweden
2005
2005
A. 1. Is the machining operation imbedding iron particles into the metal? Or dull tool work hardening the surface? Can you see the pits before with a 10X loop?
2. My favorite cycle is: Clean-Etch-Deox-Dilute-Zincate- 4 oz/gal Baking Soda-Alkaline electroless strike-Heavy EN plate.
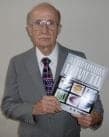
Robert H Probert
Robert H Probert Technical Services

Garner, North Carolina
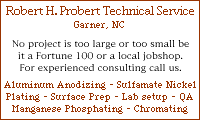
Multiple threads merged: please forgive chronology errors and repetition 🙂
2007
Q. Dear All ,
We are manufacturing parts using Extrusion Aluminium Alloy - 2014A - H15 grade / T6 WP condition material. After getting the machined aluminium housing, we do electroless nickel plating on this aluminium part. This has to withstand very hard & tough environmental conditions (-40 to +150 °C, Hot & cold temperature cycling).
The problems I face are 2 types:
1. We observe pin holes and porosity on the machined part of surface of aluminium housing.
2. Due to this, the electroless nickel plating is getting peeled off during various tests conducted to test the finished aluminium housing.
3. Even this plating is getting corroded during salt spray test conducted for very long duration.
What would have been the problem which we face now?
Please give your suggestions.
Thanks,
Electronics manufacturing - India
2007
A. Presuming that typical processes were performed between machining and EN plating, possibilities include:
Dull tooling or improper cutting fluids.
Inadequate cleaning.
Over-etching.
Inadequate desmutting.
Poor zincating (thin, double zincate is preferred).
Poor strike coating (alkaline EN?).
Inadequate EN filtration.
Inadequate EN agitation.
Excessive byproducts in EN bath.
Inadequate additives (stabilizers, anti-pitting, etc.) in EN bath.
Inadequate rinsing between any steps; DI water is necessary before the 2 EN solutions.
For pretreatment, zincating and a neutral electrolytic nickel strike (if so desired), see ASTM B253, 'Standard Guide for Preparation of Aluminum Alloys for Electroplating.' Also, many metal finishing books are available: www.finishing.com/books/
If using 'homebrew' EN solution, this is often 'penny wise and pound foolish.' Proprietary solutions produce quality coatings over a longer bath life and come with professional advice.
- Goleta, California

Rest in peace, Ken. Thank you for your hard work which the finishing world, and we at finishing.com, continue to benefit from.
A. All of what Ken said is very true. But, the best plater in the world cannot overcome cheap metal that the housing is made out of. There should be absolutely no visible pits after machining.
James Watts- Navarre, Florida
2007
A. Hi - you should give the parts an electrolytic plate. Electroless is slightly porous because of the Phosphorous. The nickel and aluminium form an electrolytic cell and then you get severe corrosion problems.
Bill Gates- milton keynes, Bucks, uk
September 30, 2010

Q, A, or Comment on THIS thread -or- Start a NEW Thread