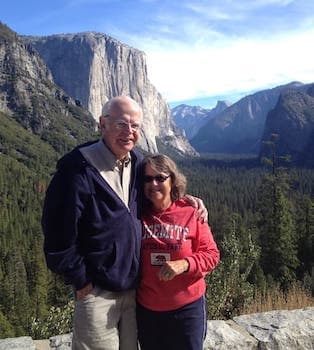
Curated with aloha by
Ted Mooney, P.E. RET
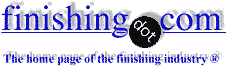
The authoritative public forum
for Metal Finishing 1989-2025
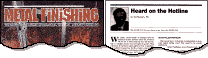
-----
EN plated parts failing salt spray. Is phosphorous level too high?
Q. Mid Electroless nickel on Brass against an 6000 series Aluminium?
I have a customer who is asking lots of questions about galvanic compatibility of mid phosphorous electroless nickel plated on a low lead brass substrate which will be in contact with a 6000 series aluminium alloy. I am not a corrosion specialist but I am a chemist and I have explained to the customer that from what I can read that aluminium and mid range EN are perfectly compatible. I am also about to explain to them that corrosion very much depends on end use environment with high alkalinity inducing failure more quickly in high P EN and high acidity inducing failure in low P EN. I have explained that mid phos 6-10% is a good compromise as the part should not see either extreme but a range - probably more on the acidic side with chlorides. Am I missing something?
Jim Mallon- Antrim N. Ireland
January 11, 2021
A. Hi Jim. If you can give us a chart or report about that galvanic compatibility of mid phosphorous EN with aluminum I'd appreciate it, because I didn't know that and it surprises me.
Meanwhile, as we await other responses, we appended your inquiry to a thread where several very sharp guys, including Ron Duncan (RIP) seem to be implying that trying to tweak phosphorous content for corrosion resistance or galvanic compatibility is unlikely to achieve much.
Luck & Regards,
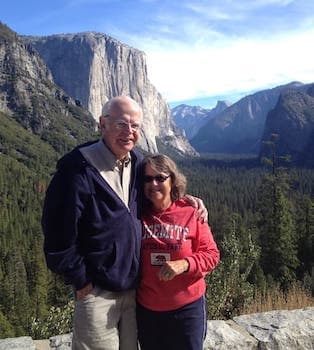
Ted Mooney, P.E. RET
Striving to live Aloha
finishing.com - Pine Beach, New Jersey
January 2021
⇩ Related postings, oldest first ⇩
Q. We used to plate nickel phosphorus between 10-12% P. What is the matter with acetic acid ⇦ this on eBay or Amazon [affil links] spray saline when the phosphorus is higher than 12%? (about 13-15%)
Roberto Capriaplating E-Nickel - Pilar, Argentina
2005
A. Why? ... is it failing a QC test? Higher Phosphorous EN solutions cost more, are harder to control and do not get as many tank turnovers as lower P. Some shops have no problem, but more do have problems with it (opinion).
James Watts- Navarre, Florida
2005
2005
A. Salt fog type tests (whether neutral or acetic acid ) are mostly porosity tests. The phosphorus content of a high phosphorus coating does not have a significant effect of its results. If you are seeing reduced performance, I would suggest that you look at other factors like bath age or substrate quality, and not whether the coating is 11% or 14% phosphorus.
Most commercial high phosphorus EN Bath will not produce coatings with more than 12% Phosphorous, unless they are plating at a very slow rate.
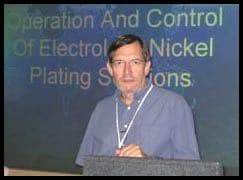
Ron Duncan [deceased]
- LaVergne, Tennessee
It is our sad duty to note Ron's passing on Dec. 15, 2006. A brief obituary opens Episode 13 of our Podcast.
Q. Always we worked about 10-12% Phos. But two months ago we discovered serious corrosion with acetic acid salt spray testing. At different laboratories, they informed us phosphorous content was 7%, 11% and 15%!
I would guess initially that 7% is a problem, but then when it appears 15%, I don't know now. So, I ask you if the 15% is a probably the cause of the corrosion.
- Pilar, Argentina
2005
2005
Not enough information, so some general suggestions for determining the problem. As noted above, the P content isn't the root cause.
Poor corrosion results can be caused by inadequate surface preparation, insoluble impurities (inadequate filtration) or soluble impurities (buildup with metal turnovers and impure chemicals).
First, does the EN pass adhesion (bend) testing? If so, surface preparation may be OK.
Second, do a porosity test of as-plated specimens. E.g., alizarin test on aluminum, per ASTM B733. Failure would suggest better filtration is required.
Since your bath is quite old, the buildup of soluble impurities seems likely. How many metal turnovers [has it run]?
- Goleta, California

Rest in peace, Ken. Thank you for your hard work which the finishing world, and we at finishing.com, continue to benefit from.
Multiple threads merged: please forgive chronology errors and repetition 🙂
Massive corrosion of electroless nickel plated aluminum parts
Q. Aluminum parts of a radar system that were coated with 17 microns of electroless nickel 10% phosphor showed massive corrosion after about eight months service outside.
Using a SEM microscope with a EDX microanalyzer I found some very small pores in the nickel. They were were filled with chlorine type material.
There are other areas that have a gold flash over the nickel which were corroded severely even worse than those with the nickel without the gold.
What could be the mechanism?
Materials Engineer - Ashdod, Israel
2007
A. The mechanism is galvanic corrosion. Occurs wherever aluminum contacts a more noble metal in the presence of electrolyte (moisture + chloride). The voluminous Al(OH)3 corrosion product lifts off the EN plating in large pieces.
There are many details (alloy, pretreatment, zincating, strike plating, dissolved & particulate impurities in the EN bath, rinsing and post-treatments) which may be involved. Chloride is present in many EN solutions, but EN plating should be non-porous and final rinsed in hot DI water. Was the EN activated for gold plating using HCl solution? Possibly, surrounding areas can be masked off and the gold applied by brush plating.
Use adhesion and corrosion testing on EN-plated test coupons to qualify the processing. Use at least 25 microns EN for outdoors applications. Passivation in 1% chromic acid at 50 °C for 15-20 minutes will improve corrosion resistance (especially on aluminum). Restrict any post-plating adhesion baking to 190 °C max (or omit entirely). [Heating high-phos. EN above ~220 °C yields a cracked, crystalline structure cf. the as-plated metallic glass]. For critical applications, require the plater to use ~new EN solution, 2 MO's (metal turnovers) max. A porosity test using sodium alizarin sulfonate is described in ASTM B733 and on page 186 of Electroless Plating, Mallory and Hajdu .
- Goleta, California

Rest in peace, Ken. Thank you for your hard work which the finishing world, and we at finishing.com, continue to benefit from.
2007
Porosity test for EN plating on aluminum
Q. I'm trying to find a method for indicating porosity of electroless nickel plating on aluminium. I've heard about hydrochloric spot test, but can't find the standard. Are there any other methods (that are simple)?
Anyone please help me. thanks!
university student (researcher) - Malaysia
2007
A. Try the Alizarin test according to ASTM B733 -- 04 paragraph 9.6.4
"Alizarin Test for Aluminum Alloys: Wipe the plated part or specimen with 10 mass % sodium hydroxide solution. After 3 min contact, rinse, and apply a solution of alizarin sulfonate prepared by dissolving 1.5 g of methyl cellulose in 90 mL of boiling water to which, after cooling, 0.1 g sodium alizarin sulfonate, dissolved in 5 mL of ethanol is added. After 4 min contact, apply glacial acetic acid until the violet color disappears. Any red spots remaining indicate pores."
Bnei Berak, Israel
February 9, 2008
Porosity in base metal causing plating problems
February 3, 2017
Q. I am having plating problems such as visible peeling and blistering and voiding in areas. Typically we are plating small precision machined housings from 6061-T6 aluminum alloy. The plating is typically electroless nickel and then gold. We did some cross-sectioning and SEM analysis and are finding micro-pores (micro-voids) in the base metal. These voids get plated over and entrap contamination, plating fluids, rinse fluids, etc. and then bleed out or pop out during further processing of the part. Has anyone encountered this porosity problem in the base material and what can be done to mitigate it?
Bob DiamondMechanical Engineering - Hauppauge, New York, USA
February 6, 2017
A. Bob,
Yes, this is a common problem, unfortunately. There are many possibilities but I will just mention one. First, a few questions. You mention problem "areas". Part to part, are the pits located in random areas on the part or are the pits always in the same places on each pitted part? Are the pits located on a common face or diameter? The reason I ask is that if in fact, for example, the pits are only on an OD and an outer dimension, there is a chance that specifying a machined surface in a given area will require the machinist to order an oversized blank or oversized stock then mill away the pores to achieve the requirements. Or one can specify blank size or stock size to be used. In my experience, it's best to inspect for pores prior to plating.
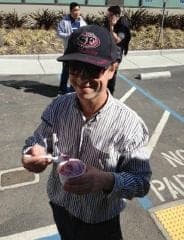
Blake Kneedler
Feather Hollow Eng. - Stockton, California
Q. Blake,
Thanks for your response to my aluminum 6061-T6 porosity question. The porosity appears in random areas of the machined parts. These parts are typically machined from rectangular bar stock and consist of machined troughs, holes, etc. It appears that the deeper the machined cut the less porosity indicating that the porosity is closer to the exterior surfaces of the raw stock.
Mechanical Engineering - Hauppauge, New York, USA
February 7, 2017
Hello, Blake has some very worthwhile info here. I was curious if you do any bead or sand blasting on the parts prior to pre clean? Nice cross section by the way.
Mark BakerProcess Engineering - Phoenix, Arizona USA
February 7, 2017
![]() |
Q. Thank you for all of your responses... I can answer the following: - Hauppauge, New York, USA February 8, 2017 A. A while ago I encountered a similar problem with a specific batch of cnc turned and then milled parts sent to me to be anodized, after dying the parts porosity was observed near some outer edges of a dish-plate sort of shaped part where sulfuric would leach out and eat up the dye, material was 6082, the pores are barely noticeable at 20x magnification before anything was done to the parts. - Riga, Latvia February 8, 2017 |
Q. Hi,
We currently have a problem with some aluminium 6082 T6 electroless nickel coated components.
They've been in storage for roughly a month wrapped in tissue paper and covered by bubble wrap. When unwrapped the parts seem to have corroded leaving a greenish white residue on the surface. Could this be because of poor plating or another possible issue?
Many Thanks.
Dave
- Uk
February 10, 2018
Q. Hello
We have an electroless Nickel-Coated (20 µm) gas cell (10-12% Phosphor) with Alu 6061 as base material, having an inner machined surface roughness of Ra~0.7µm. We have the problem that the surface seems to adsorb or even absorb small molecules. E.g., we fill in 20 ppm methanol
[affil links] in N2-mixture up to ambient pressure and monitor the Methanol concentration.
Within the first 10 minutes a decrease of concentration of ~5%. In the first hour it is about 25%. Larger molecules such as Hexane or Xylene do not show this effect that strong. Is it possible, that the Nickel coating has a significant porosity, so that the molecules get trapped there?
Does anyone have an idea what to do about it?
Thanks
Mike
- Munich, Bavaria, Germany
March 29, 2018
Electroless nickel process
Q. My situation: Hi ~ can anyone share to me step by step for electroless nickel plating process on aluminium?
Eddy TanEN process treatment - malaysia
June 28, 2018
June 2018
A. Hi Eddy. You may be highly experienced in plating on aluminum or in electroless nickel plating but not the combination, but we're don't know until you tell us :-)
One potential step-by-step is:
Non-etch alkaline cleaner
Alkaline etch
De-smut
Zincate
Nitric acid stripping
Zincate
Alkaline copper plating
Electroless nickel plating
Tarnish inhibitor
(Rinsing between each of those steps)
We have about 2 dozen threads specifically about the combination of electroless nickel plating on aluminum.
Regards,
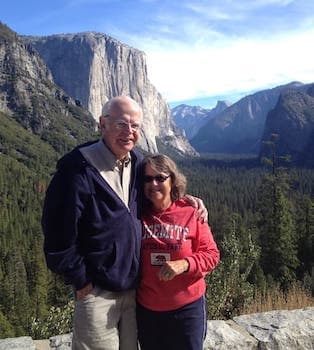
Ted Mooney, P.E. RET
Striving to live Aloha
finishing.com - Pine Beach, New Jersey
Q, A, or Comment on THIS thread -or- Start a NEW Thread