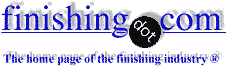
-----
Susceptibility of Cyanide Copper Plated Parts to Hydrogen Embrittlement
Is it possible to induce hydrogen into a high strength carbon alloy steel (such as 9310 or 8620) as a result of cyanide copper bath plating? If so, how does the gaseous hydrogen in the bath get converted into atomic hydrogen which would be responsible for hydrogen embrittlement. I have scanned all the literature and have yet to find anything where hydrogen embrittlement was involved as a result of copper plating. I know that parts that are chrome or silver plated or more susceptible to hydrogen embrittlement because the plating processes produce excess hydrogen gas. Additionally, would you expect more hydrogen gas to be produced in copper plating when higher than normal current densities are invoked.
Stanford O Clemens- Phoenix Arizona
1999
1999
Dear Mr Stanford.
I am treading cautiously because I have every conviction that I may be wrong !
My layman's opinion says that the amount of Hydrogen occluded in the plating process is directly proportional to the efficiency of the plating bath. All cyanide baths have a relatively poorer efficiency than acid baths where you face hydrogen over evolution in preference to metal deposition.
Acid Zinc or Nickel baths have above 95% efficiency and embrittlement is minimal in such baths. Chrome has only 20 -25 % efficiency hence high embrittlement. My thumb rule is that if you see gassing during plating, you are witnessing embrittlement taking place along with metal deposition. According to me , maximum embrittlement takes place in the first few minutes in the plating baths, when you witness maximum gassing which subsides once some thickness of coating has deposited.
We regularly plate very porous cold forgings for 20 minutes, remove and complete Hydrogen Deimbrittlement, then plate for another 20 minutes . The entire coating damage on account of the deimbrittlement gets covered by the fresh coat which does not embrittle the substrate again on account of little or no gassing in the second stage plating.
I hope this mini thesis helps , but I wish someone could explain in Technical Jargon what I have just said !
with best wishes,
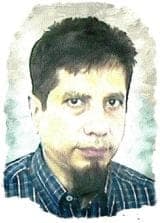
Khozem Vahaanwala
Saify Ind

Bengaluru, Karnataka, India
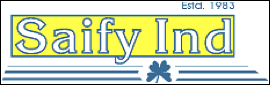
Dear Mr. Clemens:
I agree with Mr. Vahanwala. Hydrogen gas is always evolved at the cathode, the degree of percentage depends on the efficiency of the bath. For example; If your copper bath is running at 55% efficiency the other 45% theoretically is hydrogen gas. Now once you turn up the current to over come the hydrogen overvoltage of the high carbon steel your efficiency drops even more, creating more hydrogen gas. As far as the conversion of hydrogen gas to atomic hydrogen I'm not sure, all I know is that blisters are created by the absorption of the hydrogen, I am assuming it would be hydrogen gas being absorbed.
KH
Ken Hutchinson- Minneapolis, Minnesota
1999
Q, A, or Comment on THIS thread -or- Start a NEW Thread