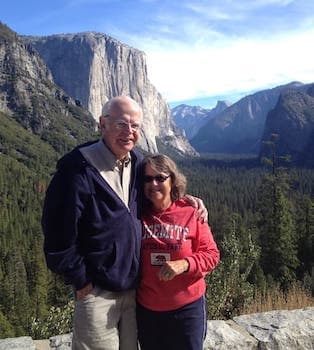
Curated with aloha by
Ted Mooney, P.E. RET
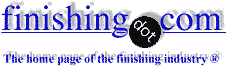
The authoritative public forum
for Metal Finishing 1989-2025
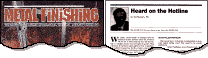
-----
Zinc plating: De-embrittlement and passivation
1999
We are about to specify Zinc plating specifications for various components. Firstly on the Zinc plating, what advantages does passivation (clear or gold) offer other than looks, and can this be combined with de-embrittlement treatments for screws or other highly stressed parts etc? i.e should the spec be: Zinc plate 5 microns thickness, de-embrittlement treat, clear passivate?
Or is this the wrong order for these processes?
I would be grateful for any help.
Wayne Ward- England
Hi Wayne, In answer to your first question the purpose of your clear or Gold passivates could be to give better corrosion protection.With a 5 micro thickness you can expect approx. 24 hours to red rust for a clear chromate and 96 hours to red rust for gold (or yellow) chromate.
In regards to de-embrittlement (baking) Many platers do clear chromate first, then bake to eliminate an extra operation, check with your customer for their specifications.This does not however work for gold chromate, you have to bake first or the parts will not only look bad but will lose the corrosion protection. Hope this helps. sincerely
Mike Adamsdecorative hardware - Rockford, il.
1999
Dear Mr Wayne,
Am in total agreement with Mr Mike Adams. However if you insist on your Vendor to bake in between the plating and passivation, the final finish would be much much better.
For Zinc blue passivation, try to only neutralize the Zinc plating in 2% Nitric acid swill, bake, then Passivate.
regards
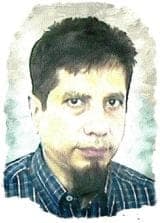
Khozem Vahaanwala
Saify Ind

Bengaluru, Karnataka, India
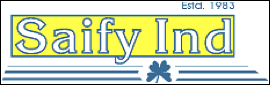
1999
September 29, 2008
Dear Wayne
The purpose of passivation is to prevent oxidation for instance if you consider Zinc Plating the passivation is done to prevent formation of Zinc oxide (White Rust).
It is not advisable not to go for electroplating for high tensile component like Fasteners as risk of hydrogen embrittlement increase if the hardness goes beyond 350 HV hence a special process of Dacrocoat or Geomet coating or any other organic coating is recommended.
With Regards
- Chennai,Tamil Nadu, India
Q, A, or Comment on THIS thread -or- Start a NEW Thread