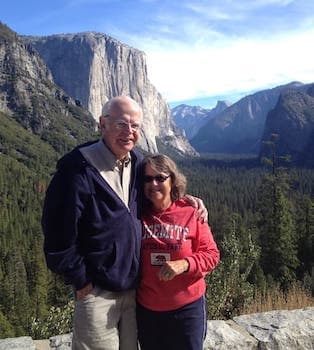
Curated with aloha by
Ted Mooney, P.E. RET
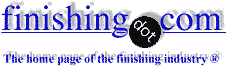
The authoritative public forum
for Metal Finishing 1989-2025
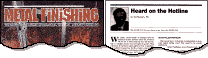
-----
Duplex nickel plating on auto part fails salt spray in LCD area
Dear Sir
We are Mumbai based Electroplaters carrying out Electroplating job works for many multi national companies in India.
We are carrying out Duplex Nickel- Chrome plating on Automobile Seat Belt Buckles for a multinational company based in India. However we are facing a typical problem in passing the 72 hour Salt Spray test for the product. The product has a small hollow notching in the centre due to which a Low current area is been developed. We are doing 30 micron duplex nickel plating on the product. During the salt Spray test rusting starts from the notching area. We are also not able to deburr or polish the inside part of the notch due to which there may be some porosity in that part. We feel the rusting is due to the porosity inside the notch. Rest all the sides of the product do not show any signs of rusting in the Salt Spray test.
We request you to help us in solving the problem and suggest ways to avoid the rusting.
Awaiting for soloutions from all the experts.
Best regards,
ELECTROPLATERS - Mumbai, MAHARASHTRA , INDIA
2005
2005
Hemal
Try the following.
1) The notch should be cut with a tool that leaves a clean cut as opposed to a rough Burred cut. This cut must be smoothed mechanically in the hand polish operation / Vibratory finisher.
2) The Plating current density must be lower than 20 asf so that adequate Nickel eventually deposits in the Notch.
15 asf might lower production levels but will get more Nickel in the Notch. In a given time.
3) maintain Chloride above 55 gpl and carrier at optimum levels. Both these techniques ensure good LCD performance.
Check present levels of Nickel in the notch and work to increase the thickness in the Notch.
Switch to a High Throw Chrome process that will ensure good Chrome thickness all over and in the Notch.
Using Conventional or High speed Chrome is all right BUT timings of
90 seconds and above are essential at 120 asf for good thickness.
Better more recent Chrome processes offer higher efficiencies for lower current levels.
And then there is Trivalent Chrome that is user friendly.
And works in recesses.
Regards,
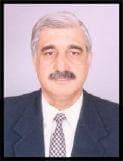
Asif Nurie [deceased]
- New Delhi, India
With deep regret we sadly advise that Asif passed away on Jan 24, 2016
Q, A, or Comment on THIS thread -or- Start a NEW Thread