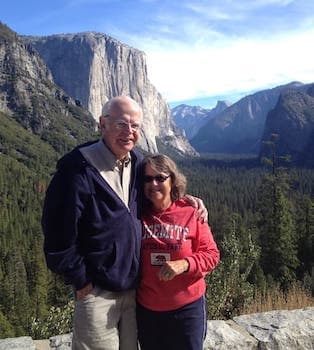
Curated with aloha by
Ted Mooney, P.E. RET
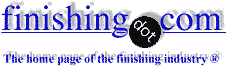
The authoritative public forum
for Metal Finishing 1989-2025
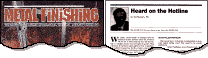
-----
NiOH2 from Watts Ni Bath
We are plating C1100 in a standard watts Ni bath for an electronics application.
Using XPS analysis, we are finding peaks of NiOH2, which the customer is attributing Adhesive failures during assembly too. Our PH is constant @ 3.8-4, we have carefully reviewed all line parameters numerous time and still can not located the cause of the Nickel hydroxide deposition.
metal stamping/plating - Phoenix, Arizona, USA
2005
We have some wonderful instrumentation these days that platers didn't have a few decades ago. Yet sometimes their availability can lead us away from a solution, as we try to understand the forest by looking at a tree under ever greater magnification. Good luck, Brad, but I find it unlikely that the observed NiOH2 has much to do with the adhesion problem. What is the nature of this C1100 substrate; is it electropolished; mechanically polished; no mechanical prep work done on it?
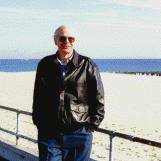
Ted Mooney, P.E.
Striving to live Aloha
finishing.com - Pine Beach, New Jersey
2005
First of three simultaneous responses --
The tank is 3.8 - 4.0, but the surface will have a higher pH. do you use boric acid? If so, is it at a good level. Possibly the simplest reduction in the NiOH is to increase agitation in the vicinity of the part. The greater solution flow over the part will sweep away the higher pH before it can go even higher and precipitate out.
James Watts- Navarre, Florida
2005
Second of three simultaneous responses --
I agree with Ted & think you should investigate the preparation of the surface before plating. Also check for stress in the nickel solution with hull cell testing.
But Ted must be right! cause he answered the question before you even asked it :)
- Melbourne, Vic, Australia
2005
Third of three simultaneous responses -- 2005
Dear Thomas,
During electrodeposition of nickel, reduction of protons and/or water is a competing reaction for the reduction of nickel ions at the cathode. These completing reactions could change the pH near the cathode due to consumption of protons or production of hydroxyl ions, respectively. The extent of the pH change depends on applied current density, mass transport conditions and dissociation equilibria in solution. This could result in the co-deposition of nickel hydroxides along with the metallic nickel.
The presence of boric acid in Watt's nickel plating bath is capable of preventing large variations in the pH of the bath due to its buffering action.
Different views exist on how boric acid influences electrodeposition of nickel. Boric acid extends the useful current density range for nickel deposition and improves the appearance of the nickel deposits which are brighter and less brittle. Though it is generally agreed that boric acid acts as a buffer in the plating bath, some studies reveals that the buffering capacity is increased by complex formation with nickel. The preferential complexing of nickel with borate ions than with hydroxyl ions reduce the chances of nickel hydroxide precipitation. Some studies proposed that nickel borate complex could act as a catalyst for metal deposition.
If you are observing nickel hydroxide precipitation in the nickel coating, then it could be due to the increase in interfacial pH.
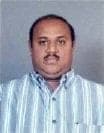
T.S.N. Sankara Narayanan
- Chennai, Tamilnadu, India
(ed.note: The good doctor offers a fascinating blog, "Advancement in Science" )
I'm not sure if I agree with Ted this time or didn't fully understood the problem. Anyway, there should be no nickel hydroxide forming. When there is, it usually comes from boric or temperature too low, or current too high at certain areas. These factors push the pH of the solution near the surface up.
Guillermo MarrufoMonterrey, NL, Mexico
2005
I'm only saying that adhesion failures are usually due to something being wrong before the parts get to the nickel tank, rather than something wrong with the nickel plating chemistry, Guillermo. But you could be right that a nickel plating solution imbalance is the problem in this particlar case. Hopefully Brad will get back to us when the problem is solved.
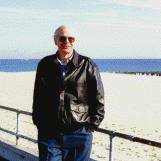
Ted Mooney, P.E.
Striving to live Aloha
finishing.com - Pine Beach, New Jersey
2005
XPS is strictly a surface analysis tool working at the atomic level and its data should be treated with extreme care. I am not surprised you detect Ni(OH)2 by XPS as I would expect all exposed nickel to have a very thin layer of corrosion material on it. You do not say where the hydroxide was detected and by what XPS technique. By that I mean XPS, being a surface technique, can give a profile through the depth of a layer if the layer is eroded away by a spherical workpiece such as a ball. This will give a longitudinal view of a transverse section and XPS can scan across the section telling you exactly weqht is where and in what quantities. I suggest you ask your customer for further details of the XPS results and their intepretation. It is quite possible that your customer has got a little knowledge and has extrapolated it beyond their abilities. I suspect, like Ted, that the failures are due to something else.
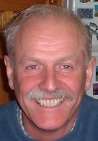
Trevor Crichton
R&D practical scientist
Chesham, Bucks, UK
2005
Q, A, or Comment on THIS thread -or- Start a NEW Thread