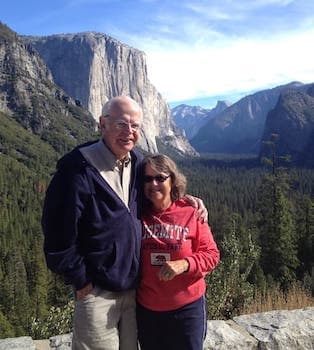
Curated with aloha by
Ted Mooney, P.E. RET
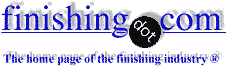
The authoritative public forum
for Metal Finishing 1989-2025
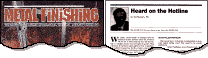
-----
Powder coat adhesion issue on aluminum
2005
The issue is paint adhesion on aluminum. I am hoping someone can help me with this. Here is what is going on.
Three stage washer: Cleaner Phosphate, rinse, rinse
Phosphate stage specs
pH running at 4.1 ù 4.2
Fluoride level at 285 ppm
Temp = 140°F
Time = Uncertain but I estimate 30 seconds.
Rinses are overflowing with second rinse cascading into the first.
The main part in question is an aluminum diecast office chair base. The part has five legs coming out from a hollow circular mount. The legs are curved on the top and flat on the sides. Another part in question is an arm rest mount for the same chair. These are also aluminum diecast. They are essentially solid round pieces of aluminum rod that are bent into a wide "U"-shape. Other die cast parts from the same customer have no adhesion issues. As a matter of fact there are no adhesion issues on any other aluminum part from any customer other than these two parts.
The paint being used is IVC Freedom Graphite Gray 84230H35K. The paint manufacturer recommends a 20 minute cure at 350°F but the customer is running his oven at 385°F and the line speed is such that the cure time is 10 minutes.
Their customer requires a minimum 2 mil thickness for the paint. Flat areas typically have 3 to 6 mils while curved areas have anywhere from 8 to 14 mils.
The customer performs a standard crosshatch test for adhesion using a
2mm crosshatch scribe tool. Adhesion testing on the flat areas is generally excellent but on the curved areas the paint seems to peel right off the aluminum as the customer makes his scribe.
Questions:
Is the fluoride concentration high enough and if we should go higher, how high could I reasonably go before no added benefit is seen?
Should the customer lower his cure temperature and slow his line speed down or does the higher cure temperature make up for the shorter than recommended cure time?
Should the customer back off on the amount of powder being applied to the parts? My unproven theory is the heavy thickness of paint on the curved areas along with the higher cure temperature and shorter cure time is not providing for well cured paint on the curved areas. Could this be the issue?
Any help would be a benefit to me. I am posting this on a couple other forums just in case someone that can help me reads that forum but not this one. Apologies for the repeats.
- Grand Rapids, Michigan
2005
Morning,
I guess it would be best to go line by line:
1) pH is low, should be 5.0 to 5.5.
2) Temps too high-try 120-125 degrees.
3) Parts should be in front of spray nozzles for 1 minute
4) Best suspect: undercure.
You can have cured and undercured paint on the same product, check with MEK / methyl ethyl ketone in unseen area so you don't damage the paint. If it's undercured all you have to do is cycle it through the oven again. The 385 is fine, but
10 minutes isn't long enough. Don't forget the ramp-up time, the cure time means the amount of time the PART is at the cure temp, not the paint. If it takes 10 minutes for the part to reach 385, then ten minutes to cure the paint, that would mean that you need 20 min. in the oven. You'll probably need over 400 degrees if you want to try and keep the 10 min cure time.
The paint thickness is a P&L question, you lose money any time the paint is over 2 mils.
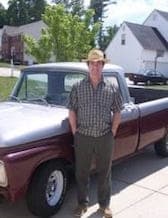
Sheldon Taylor
supply chain electronics
Wake Forest, North Carolina
2005
Thanks Sheldon,
In regard to pH it is set where it is due to the fact that the customer runs steel on the same line and our product phosphates best in the current pH range of 4.0 to 4.5.
Time in the bath or even rinses for that matter are not an issue.
As for the temperature, it is mainly dictated by the soil on the incoming steel. 140 to 145 deg F is the lowest we can go. This is the lowest temperature where the soil softens sufficiently for the cleaner/phosphate to effectively remove the current soils. We do operate at lower temperatures at other facilities where the soils are not so difficult.
Your suspecting undercure is confirmed by two other sources and is something I have been trying to get across to the customer. He has slowed his line speed by 40% to get 14 minutes in the oven instead of
10 and he has boosted the oven temperature from 385F to 400F. These changes have helped some but not completely. The thing is wherever the paint on these parts is within the paint maufacturers spec, the adhesion is excellent.
In front of me I have two goals. The first is to get the customer to reduce the amount of paint he is using and realize an improved bottom line as a result. The second is to get the customer to properly cure the parts. As you and others have said cure time is time at temperature not time in the oven. The second goal will be most difficult as the customer would most likely have to cut his line speed in half from the current speed. That would severely back him up in his production but I will need to make him realize that not doing this may cause him to lose a customer. That would be more costly in the end.
Wish me luck.
- Grand Rapids, Michigan
Good Luck. Don't let him try and raise his price in agreement to lowering his conveyor speed, that would be downright silly!
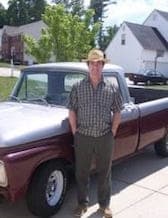
Sheldon Taylor
supply chain electronics
Wake Forest, North Carolina
2005
Thanks for the education on this thread (and others) Sheldon, but I can't agree on that part. You know much more about powder coating than I do, but I thought that being realistic about costs and payments was the bedrock of today's "partner alliance" style of business. The shop will be producing less in order to raise the quality of the product.
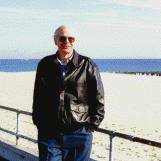
Ted Mooney, P.E.
Striving to live Aloha
finishing.com - Pine Beach, New Jersey
2005
If I were paying for a paint job, I would go into the agreement with the expectation that the work would be processed properly. If you buy a hamburger at BK they don't give it to you raw, that's because all of the expectations are there that the base product is going to be what it is supposed to be. If you want to improve it by adding extra lettuce, then they have every right to charge you more. But telling you that they will charge you extra if you want the meat cooked would be silly!
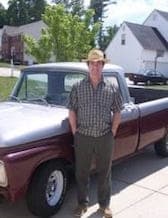
Sheldon Taylor
supply chain electronics
Wake Forest, North Carolina
2005
While that is certainly true, Sheldon, erecting roadblocks that make successful resolutions highly improbable will prove counterproductive. No shop, regardless of whose fault it was or how it happened, can halve their production and hold the price.
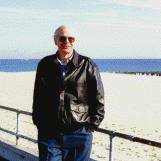
Ted Mooney, P.E.
Striving to live Aloha
finishing.com - Pine Beach, New Jersey
+++++
2005
Update.
It appears that adhesion issues may be stemming from a process at the die casting facility. We are currently undertaking a study to determine whether or not a portion of their process could be the root cause of the adhesion issue.
This could get very interesting here in the near future. It may prove my mom's old saying about not pointing fingers.
- Grand Rapids, Michigan
Q, A, or Comment on THIS thread -or- Start a NEW Thread