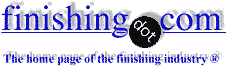
-----
Current distribution across an anodizing tank
I am involved in reducing the variation that we are seeing from an sulfuric-based anodizing process at a supplier which also involves subsequent dyeing/sealing. The most critical measure is what is called the "a" value after dyeing, a measure of red-green shift in colorimetry. In measuring this "a" value, we have found that the "a" value is highest (most red) near the perimeter of the tank (buss bar holds 10 racks of parts; rack #10 and rack #1 are consistently the highest, with the center racks lower. There is also some difference top to bottom, with the top & bottom nearly identical and the middle lower. Picture this as an elongated "bull's eye" with red shift towards the outer rings...) Work so far has lead us to the anodizing tank, as we have found that there is a distribution in current cross the buss bar that follows the rack-to-rack "a" distribution. Cables for the anodes are positioned on both ends, cathodes are on the long sides of the tank. Is this a fairly common phenomena? Are there some guidelines on cathode placement, design, etc. that could be considered? We've thought about placing "dummy" racks on the outside if there is some electrical gradient/edge effect that can be changed, or removing the outside racks, but this then reduces throughput. Also, are there other factors that should be considered? Thanks.
Electronics Mfgr. - Deer Park, Illinois, USA
2005
Although I'm frankly surprised that this could cause a noticeable color shift, we do see a "classic" current density distribution in your graph. Edges and corners tend to receive a higher current density because they are not surrounded by other metal with which to share the current coming from the cathode. The first and simplest way to improve the current distribution is to make the cathode smaller than the anode. For example if your anodizing rack is 4 ft x 4 ft, the cathode could be made 3 ft x 3 ft and centered on the rack (exactly how much smaller would depend on the anode to cathode spacing).
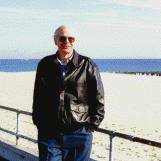
Ted Mooney, P.E.
Striving to live Aloha
finishing.com - Pine Beach, New Jersey
2005
First of two simultaneous responses --
1st as an old plater tossed into this anodizing game, anodes are the parts, (+) and the cathodes are the things haning into the solution, (-). We do not have very much varition in thickness as long as we are "starving the anodes (Parts), As the coating builds it also builds resistance, so the deposit tends to level out.
Chris Snyderplater - Charlotte, North Carolina
2005
Second of two simultaneous responses --
Jeff
You might want to look a the free acid content of the anodizing solution. You will get better throwing power and distribution in a solution with a higher acid concentration. Solution agitation may also have an effect on your 'a' factor as localized overheating will affect film characteristics.
- Colorado Springs, Colorado
2005
Q, A, or Comment on THIS thread -or- Start a NEW Thread