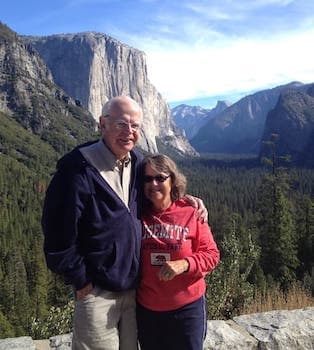
Curated with aloha by
Ted Mooney, P.E. RET
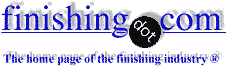
The authoritative public forum
for Metal Finishing 1989-2025
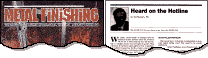
-----
Removing burrs on sheet metal components
Q. Sir,
I have one sheet metal component, length 400 mm, width 285 mm & thickness 1 mm,
it has got piercing and blanking operation.
I have difficulty in removing small burr generated during blanking & piercing operation.
At present we are removing the burr manually(buffing).
Please suggest me how to remove this burr in large scale (production) basis.
- Bangalore, Karnataka, India
2005
A. Your parts are too thin to consider anything other than an automated system with a fixture to maintain flatness.
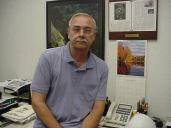
AF Kenton
retired business owner - Hatboro, Pennsylvania
2005
A. You can think of Fine blanking operations with appropriate tools/die if costs permit, for minimum burr on mass production basis.
A simple barrel tumbling with suitable media stones and alkaline barrel polishing soap can solve the problem.
It recommended to deburr when the material is in hardened condition, in tempered condition the burr tends to fold and becomes difficult to remove.
- Bangalore, India.
2005
Q. Dear Sir, we make in shims in Stainless steel in 40 mm; and we get Burrs that we clean with buffing. Please guide how to get rid of the process.
Reema Suri- Mumbai, India
July 25, 2013
A. You only gave one dimension. Need more info. Are we to assume that the strip is processed reel-to-reel so there is no length dimension, and that you offer the shim stock in various thicknesses? If so, what range of thicknesses?
While you are at it, please give me some idea of quantities.
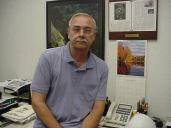
AF Kenton
retired business owner - Hatboro, Pennsylvania
July 29, 2013
Q. Dear Sir, we do blanking in SS 301. The thickness is .40 mm and the width is 40 mm and length is 60mm. After blanking we get cutting burr that does not get completely removed after putting in the vibrator (doing a dry run). We do not use the solution as black patches are visible after we remove them after a period of time.
So we buff the edges and then put in the vibrator. Please guide. Thank you
- Mumbai, India
August 7, 2013
A. OK. Because your parts are already going through a mass finishing system, it sounds as if you thickness and size are not the issue. So, if you don't have the ability to sharpen the die and you still want to do your parts in a dry process, I suggest you add some pumice to your dry mix.This will give your parts a satin or antique look and speed up burr removal.
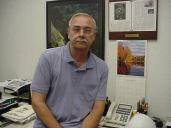
AF Kenton
retired business owner - Hatboro, Pennsylvania
August 7, 2013
Q. Do we have some industrial standards as to how much burr is allowed if I do piercing on CRC sheet of 1 mm thickness?
Debashis Mishra- Bhiwadi, India
May 31, 2016
![]() |
A. Although 1 mm is a pretty hefty part, the ultimate decision is your end customer. Bottom line is it has to fit form and function without any serious safety related problems. ![]() AF Kenton retired business owner - Hatboro, Pennsylvania May 31, 2016 A. Hi Debashis, Aerospace - Yeovil, Somerset, UK June 1, 2016 |
Q, A, or Comment on THIS thread -or- Start a NEW Thread