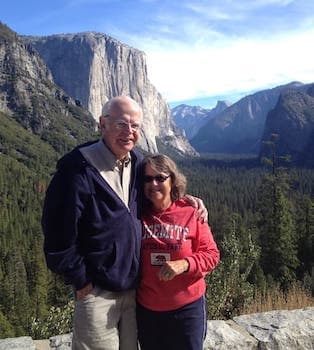
Curated with aloha by
Ted Mooney, P.E. RET
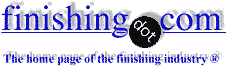
The authoritative public forum
for Metal Finishing 1989-2025
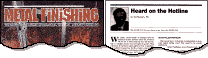
-----
Tin Pesting on Tin Plated Bussbars
2005
I am a Supplier Quality Engineer for a Rail Car Manufacturer in upstate N,Y. Currently I am witnessing tin Pesting on Copper Buss bars that are being plated TO ASTM B339 -95 Grade A at a plating house using a tin Bismuth Plating Process with Properties of (Tin -66.7 oz/gal-500g/l, Bismth-0.2 oz/gal-1.5 g/l, Density-13.9 lbs/gal-1667 g/l, & Appearance-Slightly turbid, viscous liquid. Tin Pesting is a condition brought on by subjecting pure tin to temperatures below 32 degrees F at which time the affected tin turns from a Beta Tin (Bright,Whitish in color)into an Alpha Tin (Dark and greyish in color)and flakes of into an ash like substance that crumbles into powder. We are attempting to combat this issue with Tin Sol B by Atotech which is a tin solution, 66oz's per gallon of tin that has been made impure by the addition of 2oz's per gallon of Bismuth. This combination by design should eliminate this Pesting condition However we are still experiencing Tin Pesting at an unacceptable rate when subjected to our testing freezer set at -15 degrees F. Is there a better solution to safe guard against this condition and if so what?
Jeffrey D SawczyszynAlstom Transportation - Hornell, New York
Tin pest is a fact of life with tin; it is the transformation of beta tin to alpha tin and occurs (in pure tin) at 13.2C. This temperature is suppressed by impurities, so its elimination can be achieved by using tin alloys. However, the temperature at which it starts will depend on the alloy being used. It is claimed that the presence of 0.12% bismuth in the tin can reduce the transformation temperature to -73C; I have never worked at these temperatures so cannot comment on this claim. However, I would suggest increasing the amount of bismuth in your bath and possibly adding brighteners such as trialkoxybenzaldehydes or methacrylic acid, although no doubt your supplier will have others available. You can also reduce the transformation temperature by adding antimony (up to 6%) or even copper, to put down a white bronze. There are also other metals that could form suitable alloys, such as silver and lead(!?!). I appreciate lead is a health "no-no", but sometimes legislators do not understand and take full account of their actions. One other suggestion may be to deposit the tin-bismuth alloy and then heat treat the buss bar so that some of the tin migrates into the copper, thereby enriching the outer layers with bismuth.
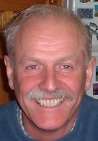
Trevor Crichton
R&D practical scientist
Chesham, Bucks, UK
2005
Tensile stress in the tin plating greatly accelerates the transformation to the more voluminous gray tin. This is due at least partly to the difference in thermal expansion coefficients; the CTE of white tin being 1.39 x that of copper. Residual plating stress may also be involved. Your temperature ( -26 C) is near that for the maximum transformation rate, -30 to -40 C, and it is also possible that the plated tin contains less than the recommended 0.3 wt.%.
Possible solutions: 1) Use unplated bus bar, 2) Nickel plating, 3) Silver plating (not applicable if much moisture or exhaust fumes are present), 4) Plating with an 80%Sn-20%Zn alloy, 5) Sn-4%Ag-4%Cu applied via hot dipping, 6) Annealing out residual plating stresses at 200 °C (may result in some alloying or intermetallic formation, possibly helpful), or 7) Aluminum bus bar (use Alcoa #2 Electrical Joint Compound at bolted connections).
An interesting paper, with photographs, "Tin Pest: A Forgotten Issue in Lead-Free. Soldering?" by Ronald Lasky, Ph.D., is available online from Indium Corporation of America: http://www.indium.com/drlasky/files/TinPestPaper0723Final.pdf
- Goleta, California

Rest in peace, Ken. Thank you for your hard work which the finishing world, and we at finishing.com, continue to benefit from.
2005
Q, A, or Comment on THIS thread -or- Start a NEW Thread