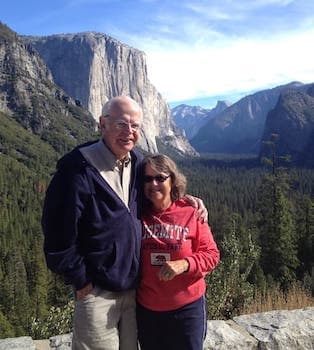
Curated with aloha by
Ted Mooney, P.E. RET
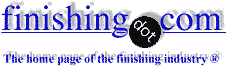
The authoritative public forum
for Metal Finishing 1989-2025
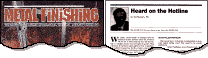
-----
Preventing copper contamination from bus bars on process tanks

Q. I HAVE A C110 COPPER BUS BAR. IT HAS TIN PLATING PER ASTM B545 CLASS C. - AFTER TIME, DISCOLORATION TAKES PLACE.
WILL AN ELECTROLESS FLASH NICKEL COATING, MEDIUM PHOSPHATE, PROVIDE EXTRA PROTECTION FROM DISCOLORATION?
- SUWANEE, Georgia
March 7, 2022
A. Hi Eric. Electroless nickel plating is often used on the anode rods on plating tanks to protect them from quite aggressive exposure like drips of plating solution. So it will certainly help a great deal in resisting corrosion and deterring discoloration, but the copper bus bar will then no longer comply with the spec ... which raises the question of why tin plate it then?
Please tell us more about this situation -- are you doing this plating for a customer or is this a plant engineering project for your own shop, or what? Where is the bus used: open, in bus duct, etc. Thanks.
Luck & Regards,
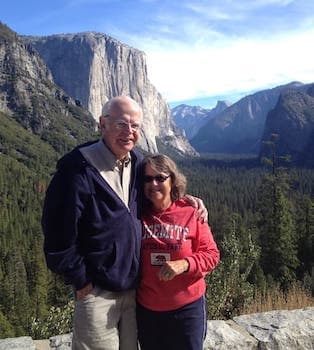
Ted Mooney, P.E. RET
Striving to live Aloha
finishing.com - Pine Beach, New Jersey
March 2022
March 9, 2022
Q. Aloha Ted,
Thank you for responding.
FYI I am plating challenged.
History of the Busbar:
The busbars are used in an electronic storage rack for 19" wide equipment. They are installed somewhere in Singapore with close proximity to the bay. We are told they are installed in a closed environment but have to survive shipping overseas and we can't monitor what they are exposed to.
Our Customer didn't like the copper busbar tarnishing so they asked us to use a Tin plating on the surface. We use a reputable Busbar manufacturer that makes and plates the bars.
Some busbars from time to time tarnish and turn dark which the customer views as faulty plating but I've come to understand now that Tin and Silver plating can tarnish and is normal (your opinion?)
Problem:
Material: C110 Copper, Finish: ASTM B545 Class C
Some plater I found online says that they use : Electroless nickel Medium Phosphorous per AMSC26074 (flash) 100 micro inches maximum for their customers' Tin Plated Bars with good results. YOU STATED THE BUS BAR WILL NO LONDER COMPLY WITH SPEC ... Is that because the the Tin plating gets altered (can you elaborate a little)?
Bottom Line:
I have Material: C110 Copper, Finish: ASTM B545 Class C
That I'm trying to prevent from tarnishing as long as possible. Would Class D or E be better or does the outer exposed surface still tarnish?
Is there a passivation process that can be used to help with the aesthetics and seal in the Tin
Electroless nickel Medium Phosphorous per AMSC26074 (flash) 100 micro inches maximum? (still conductive and prevents tarnishing?)
It seems all bus bar manufacturers either use tin or silver with some flash nickel undercoating but I can't find anyone who says this process or that process will prevent tarnishing ...
Thanks for your feedback
I wonder if I should just use an Electroless Nickel Medium Phosphorous coating. Is this a legitimate coating for copper bus bar?
Would provide the best protection and aesthetics on the copper bus bar instead of trying to coat over Tin be better? Again the customer would like to avoid any tarnishing and discoloration over time.
Most bus bar web sites seem to only talk about Tin and Silver ?
I hope I'm not burdening you with all these questions.....answer if you are able.... GOD BLESS
![]() |
PS going to Yellowstone and Tetons in May. |
Eric
Eric Radosevich [returning]Designer - SUWANEE, Georgia
March 2022
A. Hi again. Sorry, I did not mean to imply that electroless nickel would ruin your tin plating, just that the finish is no longer compliant with ASTM B545. By way of a silly parallel, if a customer orders a black car, the dealership can't decide to put a coat of white paint on top so the AC will work better, and claim that it is still the black car the customer ordered even though the black paint is still there below the white. But the dealership can get permission from the customer to put the white paint on ... and you can probably get permission to do ASTM B545 followed by AMC C-26074.
There are some tarnish deterrents like Tarniban. I think most were based on hexavalent chromates in bygone days but may be based on zirconium and/or silicate compounds these days. The plan of using a thin electroless nickel plating sounds feasible to me, and it seems like you know a shop claiming success with it, and I wouldn't want to discourage that. But whether it's a flash of electroless nickel on top of the tin, or replacement of the tin with electroless nickel someone has to make sure that whatever finish is supplied does not violate code requirements for the product in question.
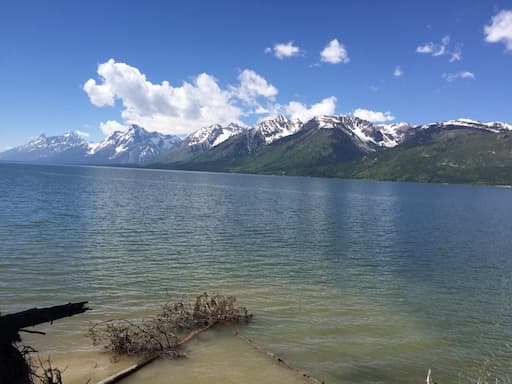
![]() |
The portrait of my wife & I is from Yosemite. I've been to Yellowstone and it's a beautiful park! We hadn't thought about the Tetons in our vacation planning, didn't even knew where they were. To our embarrassment but happy surprise, right there on our drive from Yellowstone to the Jackson Hole airport stood the magnificent Grand Tetons :-) |
Luck & Regards,
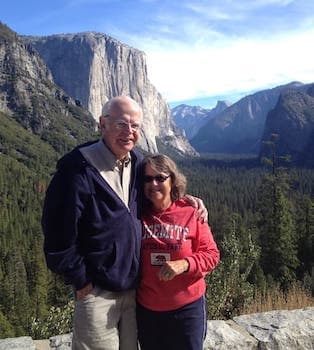
Ted Mooney, P.E. RET
Striving to live Aloha
finishing.com - Pine Beach, New Jersey
A. Eric: Try to dip in a slightly alkaline solution.
Ted: Of course a chromate passivation is the best solution, but hexchrome is a big NO NO.


Sara Michaeli
Tel-Aviv-Yafo, Israel
April 4, 2022
⇩ Related postings, oldest first ⇩
Q. Dear Sir
Ours is a Zinc producing plant by Hydrometallurgy route. ZnSO4 solution(Electrolyte) is electrolysed to deposit Zinc on Aluminum cathode. We are having a problem of High Copper 0.8-1 Mgpl in the ZnSo4 solution which is decreasing our current efficiency. Copper is getting enriched because of the Copper dissolving from the Copper Busbars used for power supply and contaminating the electrolyte. Copper is not even getting deposited on the cathode along with the Zinc so that it can removed from the system.So I would like to know from you How the Copper can decreased from the Electrolyte either it can be depositing along with Zinc or is there any protective paint that can protect Copper busbar from acid and stop dissolving copper from the Busbars.
Regards,
Hindustan Zinc Limited - India
2005
A. Hi Satyanarayana. Two things I've commonly seen are electroless nickel plating of such anode, cathode, and bus material, which is a trouble-free solution; and, if you can do it without interfering with workability too much, building PVC shields of some sort so drips don't land on the bars.
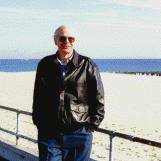
Ted Mooney, P.E.
Striving to live Aloha
finishing.com - Pine Beach, New Jersey
2005
Q, A, or Comment on THIS thread -or- Start a NEW Thread