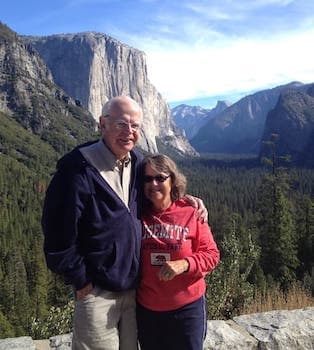
Curated with aloha by
Ted Mooney, P.E. RET
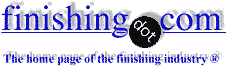
The authoritative public forum
for Metal Finishing 1989-2025
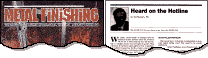
-----
Nickel Sulfamate Plating: Pitting in Bath
Q. I am doing heavy Ni plate around 0.100" in a sulfamate solution. Pitting of the sort caused by bubbles is a problem I battle constantly. I use air and flow agitation. None of the proprietary anti-pitters have done the job I want. It is requiring a tremendous amount of wetter to keep the surface tension at a low enough level for my rather unique application. The organic load becomes quite high requiring c-treatment. I have been experimenting in the lab with sodium lauryl sulphate along with some other additives. Foaming is a problem. I was hoping to find a good generic recipe I could tweak to my needs.
Patrick McLaughlin- Oil City, Pennsylvania, USA
2000
Hi Patrick,
I think it is very difficult to plate 0,100 inch in a nickel sulfamate without pitting. I suggest you to do a machining after 0,39 inch and plate additionally for 0,39 inch. Because when you plate so much inch the nickel deposit tends to make pitting when the current will change a little over the parts area and the time in the solution is so long. I suggest also you should plate with a low current to make a better results. I don't believe the pitting depends on the wetting additive or the agitation in the solution.
Best regards Anders Sundman
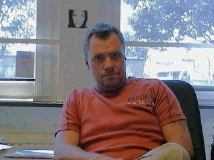
Anders Sundman
4th Generation Surface Engineering
Consultant - Arvika,
Sweden
Have you tried SNAP-AM from Macdermid? Do you constantly filter the tank? This will add to the total agitation. I normally used a 10u filter, but a 25u filter will probably work and give you a lot higher flow. This flow could probably be directed at the problem area.
By air agitation, most people mean a tube(s) on the bottom of the tank. By making a tube out of tygon or similar tubing , bending a SS rod to a desired shape, and wiring the tube to the rod, you can get the air agitation directed to the most needed place. Holes can be put in the tube with a hot piece of wire or by drilling slowly. A ss screw will plug any wrongly placed holes. I would run the tank at 120 °F. Less stress and less problem with pits.
James Watts- Navarre, Florida
Multiple threads merged: please forgive chronology errors and repetition 🙂
Q. I am have a pitting problem with my bath ( nickel Sulfamate) the pitt's are down low near the agitation of the solution. The pitt's seems to clean and slanted upwards however the surface tension is being kept down around 25 dynes/cm. There is 15 ppm of Pb in the solution and 326 ppm of mg in it. Here is the other level's of the bath
nickel sulfamate ---- 10.7 oz/gal
Add a MgCl --------- .45 oz/gal
Boric acid ----------- 5.10 oz/gal
pH ----------------- 3.9-4.0
Temp---------------- 136 F
I ran hull Cell's of 1amp no air 2 amp air, 3 amp air, 5 amp air. and there was no problem with the hull Cell's. Where can I look next.
David MorrisonQC chemist - Titusville, Pennsylvania, USA
2004
A. What sort of agitation are you using and what is your operating cathodic current density? If you are using an air sparge, your problem could be too much air causing impingement pitting. If it is agitation by pumping, you may be getting air (or some other gas) into the electrolyte and this is coming out as bubbles. Your description suggests pitting caused by air bubbles. Your bath composition, operating pH and temperature are all OK. The lead doesn't seem to be a problem as it doesn't show up in the Hull cell tests. Out of interest, why are you using magnesium chloride and not nickel chloride, surely the nickel salt is more usual, but perhaps more expensive?
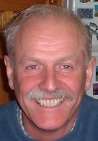
Trevor Crichton
R&D practical scientist
Chesham, Bucks, UK
Q. Also I just got back the results for a test that was ran on two tanks. It found 497 mg/L of Nitrogen ammonia ⇦ this on eBay or Amazon [affil links] in one tank and 288 mg/L of Nitrogen ammonia in the other tank. The method Source for the test was EPA 350.2 Could some one please enlighten me on these results.
Thank you,
David Morrison [returning]- Titusville, Pennsylvania, USA
A. Sounds like the sulphamate is breaking down into ammonia and sulphate. This is well known with sulphamate but normally only occurs at over 70C. I wonder if inert anodes could also cause this to occur? It would still be useful to know the answers to the previous questions.
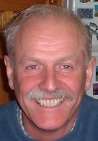
Trevor Crichton
R&D practical scientist
Chesham, Bucks, UK
A. Ref.documentation
impurity limit ppm
fe 200
cu 10
zn 10
pb 2
al 6
cr 2
- Paris, France
A. David, ammonia is the result of the sulfamic radical breaking down. IT IS A COMMON IMPURITY IN CHEAP SULFAMIC ACID. I left you the procedure for qc-ing incoming sulfamic acid. Other causes of high ammonia are: too hot, like above 140 F, time, high anode current density (so be sure you have enough anode area and be sure to flush out the sludge from the anode bags frequently - after every run in your case). ammonia does not cause pits.
Ammonia causes brittleness. You do not have high ammonia, yours is actually very low right now. Brittleness starts at about 4000 to 5000 mg/L.
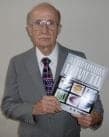
Robert H Probert
Robert H Probert Technical Services

Garner, North Carolina
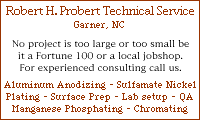
Multiple threads merged: please forgive chronology errors and repetition 🙂
Q. We have nickel sulfamate bath. My problem is pitting occurs around topside of workpiece. Worker checked, air agitation is OK. pH 4.0, solution analysis NiSO4 230 g/l, NiCl 35 g/l, Boric 34 g/l. This solution is uses about 5X per year. But we maintain always.
Now we try to add hydrogen peroxide 0.1 cc/l then agitation 30 min and continuous filtration by carbon cartridge. This problem remains. So we try it again. But this problem is not yet OK. What do we do?
Thank you.
Tawatchai Sujitranurukplating engineer - Bangkok, Thailand
2004
![]() |
A. It could be due to numerous things, but the most likely are a lack of surfactant and/or particulate contamination. What additives are in the electrolyte? ![]() Trevor Crichton R&D practical scientist Chesham, Bucks, UK A. Tawatchai, Hydrogen peroxide doesn't work with temperatures higher than 50 °C (peroxide has a short oxidizing time at this temperature). See if you have some dirty dust over the plating tank. Hydrogen peroxide is for removing of iron in the solution. If you think this pitting is from iron contamination you should do a pH treatment with hydrogen peroxide. Regards, ![]() Anders Sundman 4th Generation Surface Engineering Consultant - Arvika, Sweden |
Tawatchai, please check:
1) The air agitation.
2) The level of iron .. if the walls are yellow inside its likely to be iron. Follow the procedure outlined in another reply.
3) Pitting can also occur from excess Nickel Brightener and unbalances carrier adds.
4) Oil. Nitrates and organic impurities are other causes.
I would suggest you contact a local chemical supplier.
Regards,
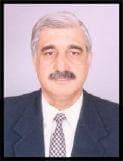
Asif Nurie [deceased] [deceased]
- New Delhi, India
With deep sadness we acknowledge the passing of Asif on Jan 24, 2016
I accept the others suggestion and also you don't have to forget current density maybe you use it high and also suggest you use sodium lauryl sulphate
goooooooood luck
Amir.
April 26, 2009
student - Tehran
Multiple threads merged: please forgive chronology errors and repetition 🙂
Q. I am a chemical engineer at a defense and space company working mainly in circuit fabrication. We have been having a lot of problems with pitting in our nickel sulfamate bath. I was wondering if you guys had any additional advice that you could give me.
Here's the scoop. I have tried many of the common solutions to pitting problems. Adding boric acid, providing additional agitation, checking the pH, checking the connections from the rectifier, and adding some hydrogen peroxide. These modifications didn't help, thus, we have replaced the nickel bath twice, since the first replacement didn't provide any difference either. We seem to be having most of the pitting on smaller surface areas.
I am thinking of replacing the anodes or cleaning the anodes that we currently have. What is the best way to clean the nickel s-round anodes? HCl and water?
Any other suggestions that could help solve this mystery?
Thank you very much for your help and advice.
Warm Regards,
Defense & Space - San Diego, California, USA
2005
A. Does your process use proprietary additives? If so check the levels of brightener and wetting agent (you may need to ask your supplier for advice about how to do this).
Check the surface tension of the solution. If the chemistry of the bath is correct there could be two problems:
1. Pre-cleaning. You haven't told us what the pre-clean cycle is. Any contamination left on the surface will affect the quality of plating (check for water-breaks before you nickel strike).
2. The parts are not wetting out in the plating bath. By checking the surface tension of the solution you should be able to determine if you have sufficient wetting agent present.
If you are still not getting anywhere you could consider asking your chemical supplier for assistance, they usually have a reasonable idea about the process.
Aerospace - Yeovil, Somerset, UK
![]() |
A. Check rectifier, electrical contact, Voltage on rectifier and compare with the voltage in anodes and cathode, check water quality, it should be D.I. water. Carlos Carrera- Miami, Florida, USA A. Dear Ghee, - Mexico City, Mexico |
![]() |
A. I note from your information that you have changed the nickel bath without solving the problem. I presume you have done a Hull cell test to make sure your bath is working correctly; if not, this should be your first test before changing anything else. You say you've checked everything, but I see there is no mention of a wetting agent. You will need one that is compatible with your process. Wetting agents are essential to most plating as it reduces the propensity of hydrogen bubbles adhering to the cathodic surface during plating and thereby making pits in the deposit. Nickel deposition is not 100% efficient, so there will always be some hydrogen deposited, but the trick is to prevent it sticking - hence wetting agents. You also do not mention whether the process is proprietary or in-house; if the latter, ask the supplier and if the former, then it's down to you....Other causes of pitting can be operating at too higher current density, inadequate agitation or the wrong pH. The current density is in part connected to the nickel ion concentration, so make sure the two are compatible. Inadequate agitation will allow gas bubble to adhere and the wrong pH will allow excessive hydrogen (too low pH) or nickel hydroxide inclusions (too high pH). I would suggest about 6-8 tank turnovers per hour for common nickel plating and sulphamate nickel should operate at pH 3.6-4.3. It should NEVER operate at over 70 °C as the sulphamate breaks down to sulphate and ammonium ions, causing an increase in stress. If the bath chemistry and operating conditions are OK, then in must be either the plated part (porous substrate?) or the cleaning cycle. Is it possible that the substrate is still contaminated with photoresist materials? It is possible that there is solution contamination due to drag-in, but this is not a common problem in a well run shop. Hope this helps - good luck. ![]() Trevor Crichton R&D practical scientist Chesham, Bucks, UK
- San Diego, California A. It sounds like you are plating at a high CD for the given Chemistry and plating parameters. cut back on current Density say at 50%, see what happen. - Mays Landing, New Jersey, USA |
Q. The bath we are using is at a pH of about 3.4 because the technical data sheet from the vendor states that it should be between 2.75-4.5, with an optimal pH of 3.25. The operating temperature is at 50 °C. We use an in-tank filter pump that is connected to a couple of spargers for agitation.
When racking the part using copper wire with two connections to the substrate, the plating comes out pretty good. However, when I try to use the standard rack that we use, which is comprised with a polypro shell with one copper connection, we seem to continue to get pits. Could the rack be adding to the problem? (FYI, the substrates we plate do have photoresist material on them)
Thanks for your help and advice.
Sincerely,
- San Diego, California, USA
? How about some pictures of the parts and the racks? It may help....
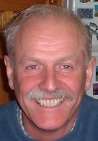
Trevor Crichton
R&D practical scientist
Chesham, Bucks, UK
A. IF YOU ARE GETTING PITTING YOU MIGHT WANT TO TRY TWO THINGS REPLACED YOUR ANODE BAGS WITH FRESH ONES A HEAVY POLY NAP IS REAL GOOD IT IS A LITTLE MORE EXPENSIVE BUT THEY WILL LAST ABOUT 10 TIMES LONGER AND BE CHEAPER IN THE LONG RUN ALSO YOU MIGHT WANT TO TRY SNAP L WETTER WE USE THIS AND IT SEEMS TO CLEAR UP THE PITTING WE HAVE. IF THAT DOES NOT WORK YOU MAY NEED TO FILTER YOUR NICKEL BATH OR CHECK IT FOR POSSIBLE CONTAMINATION.
DOUG THOMPSON- ERIE, PENNSYLVANIA, USA
2006
Multiple threads merged: please forgive chronology errors and repetition 🙂
Q. Our customer is experiencing pitted nickel deposits from a proprietary nickel sulfamate bath. The bath is a new make up. The parameters are as follows: Nickel metal- 15.5 oz. per gallon, nickel chloride 0.1 oz. per gallon, boric acid 5.5 oz. per gallon and pH 4.1, temperature 140 °F. The plating line is reel to reel plating on carbon steel wire using S round nickel anodes in titanium anode baskets. The cd is approx. 60 asd. The plating tank has air agitation and gravity overflow from the wire passes on each end of the tank. The pits have no visible tail and are concentric circles. There is no wetting agent in the tank since earlier testing using a beta cell indicated it was not necessary. The pre-treatment is an alkaline soak clean, alkaline electroclean and sulfamic acid salt with appropriate rinses. The line speed is 18 meters/minute and the wire is about 3/4" from the anodes on both sides. We increased the boric acid 0.5 oz. per gallon and lowered the pH to 3.9 and the problem got worse. Does anyone have suggestions besides the obvious adding wetting agent? We can do the WA test in a Hull Cell. Thanks.
Doug Trageser- Chattanooga, Tennessee USA
February 6, 2010
![]() |
Doug, ![]() Pat Mentone St Paul, Minnesota A. Hi Doug. Commercial nickel sulfamate in the last 15 years has not been dummied and carbon treated to the extent that the old popular trade name had been treated. Even with perfect sulfamate concentrate with use at your higher temps and higher c.d., breakdown product from the SN and from the S-rounds lower the efficiency and then the hydrogen starts to cling to the cathode. In the real world without continuous dummying and continuous sulfur free carbon it is virtually impossible to operate without a surfactant. ![]() Robert H Probert Robert H Probert Technical Services ![]() Garner, North Carolina ![]() |
Q. I'm having major pitting problems in a new nickel sulfamate bath. The tank was remade a few months back before I started at this facility. This tank is not continuously used and sometimes a week or two will pass between use. The pitting is inconsistent and sometimes one side of a part will have it and the other comes out good. Here is what I have done to fix the problem:
1.) Analysis of bath each time it is used and weekly if not.
pH: 4.3 Range: 3.6-4.5
Nickel: 12.2 oz/gal Range: 9-12 oz/gal
Additive "A" .76 oz/gal Range: .4-1.2 oz/gal this is a chloride salt corrosion aid
Boric Acid: 5.2 oz/gal Range: 5.0-6.5 oz/gal
Snap A/M: .32%/V Range: .1 -.4 %/V Surface tension adjuster
Outside Analysis confirms that metal contaminates are below 1 PPM.
The bath is Barret SN. The ranges come from Macdermid.
2.) Checked agitation. The tank is 1100 gallons and the air agitation is moderately vigorous.
3.) Changed Anode Bags.
4.) Verified pre-cleaning procedures. Aluminium 80 grit blast. Then we use a wax to cover areas that don't require plating and use solvents to remove its residue followed by scrubbing and rinsing.
I have pictures I can post but I'm not sure how to. Any help would be greatly appreciated.
Plating Manager - US
February 3, 2017
Ed. note: This is one of several threads about "nickel sulfamate pitting"; use that term in the search engine to read the others.
Q. When the part was ground down it was found the pitting started about 10 thousands into the deposit. This makes me believe I am having an issue with hydrogen bubbles or pH related. So I have done the following:
1.) Increased to boric acid to stay between 6.0-6.5 oz/gal
2.) Enforced a strict pH range of 3.9-4.1
3.) Changed the placement of the air lines to get better agitation through out the tank.
I'll give another update after our next run.
- Cleveland, Ohio USA
A. You did not mention temperature, regardless of the data sheet, the boric acid solubility is a function of temp. If the temp drops during the plating process, then the boric acid comes down, if it lays on the horizontal surface, the pits form right there and grow with the thickness build. Over the weekend the boric acid drops into the corners of the tank and will not go back in unless stirred and heated. Low boric acid causes random pitting. You did not mention filtering, but a teny tiny leak in the filter pipping/hosing will make an air bubble that causes pitting (different from normal blower air agitation), so tighten down all the hose clamps and look for where the filter might be sucking air. You did not mention electrolytic purification (dummying), the S-rounds are loaded with copper which must be dummied out, if not the copper contamination lowers the efficiency and causes hydrogen bubbles to start. And how about organic contamination, a real blaster to efficiency and guaranteed to start the hydrogen bubbles - so carbon treat a small batch, maybe in the Hull Cell, and see if you get less pitting. I do not charge for "homework", call me
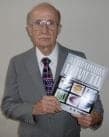
Robert H Probert
Robert H Probert Technical Services

Garner, North Carolina
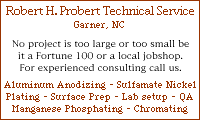
Q. The tank is maintained at 130 °F. I have verified it is fully calibrated. The heater is not turned off over the weekend so the boric should not be dropping out. After some research I found that the boric is supposed to be around 6.25 oz/gallon for 130 °F.
Filtration is accomplished by an over the side Flo King pump so no air should be getting into the solution from there. I'm used to much stronger pumps with multiple turn overs per hour but for now its all we have. The filters at 15 micro 20" depth wound cartridges. There is no present continuous carbon treatment so I have changed our filters to carbon 20" cartridges and have been keeping a close eye on the Snap-AM wetter we use in case (not sure if the carbon will mess with it but I've seen other products have issues)
I have started dummying the tank on a regular basis before parts are ran to remove any possible metallic contamination.
The last collar we ran came out without any pitting. Hopefully I can keep it that way. Here are the things I think that helped the most:
1.) Higher boric acid concentration up to 6.25-6.5 oz/gal
2.) Stricter pH range (3.8-4.2)
3.) Increased and adjusted the air agitation placement
4.) Regular carbon treatment and dummying of tank
5.) Soaking the nickel S-rounds in 2-4% sulfamate acid to clean before use in our home made anodes for these collars
- Cleveland, Ohio USA
Q, A, or Comment on THIS thread -or- Start a NEW Thread