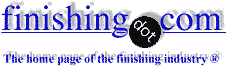
-----
Passivating stainless to remove iron after shot peening?
Q. I am the manufacturer of stainless steel furniture, grade 304.
Our products use stainless shot peening to do the surface finish, it's look perfectly nice.
But the problem is after the products have been exposed to the environment for 6 months (normal outdoor environment)..It appear to have rust on it..on the surface (tea stain or pitting ,I'm not sure what it's called)..But nothing on the welding area..All the welding area are pickled with commercial pickling gel..and we clean it before go to the peening chamber..
After the chair has been shot peened.We clean them with distilled water ,alkaline cleaning..I have followed the ASTM A967 for the passivation process ..All the process is carefully managed...
so I was wondering..Is the passivation with nitric enough?..Do I need to do the Pickling with the commercial pickling gel for the whole chair or table ..Or should I use the pickling bath instead of doing the passivation?
Need help,
Stainless Furniture - Thailand
2005
A. I assume that the weld material is purchased locally, and with pickling it and passivating it you should get good results. Passivation correctly with nitric acid according to ASTM A967 should give you good results unless it is exposed to salt spray or other chloride environment in the field. Pickling the entire unit is not likely to help you.
I assume that you are using clean, non-ferrous media for grit blasting, and you change it fairly often.
There is a lot of questionable grade 304SS available on the market these days due to the shortage. This does not mean your supplier is intentionally giving you bad steel, just giving you what is available from the sources.
adv.
If you want to talk about other things you can try give us a call.
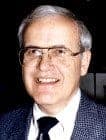

Lee Kremer
Stellar Solutions, Inc.

McHenry, Illinois
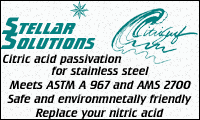
Really appreciate your response.
Yes, we were using the new Stainless steel shot (round ball not grit)..
It's just confusing me whether after shot peening what process do we really need -- Pickling or Passivation..
- Thailand
A. Normally, the reason that you blast the surface is to clean off any scale, so you should only need to passivate after the peening.
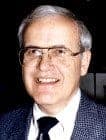

Lee Kremer
Stellar Solutions, Inc.

McHenry, Illinois
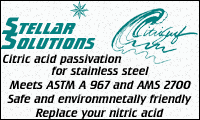
Multiple threads merged: please forgive chronology errors and repetition 🙂
Q. Hello,
I'm working in an aeronautic company, in the quality department. For some time we have a problem when we have to remove residual iron left on the surface of the aluminum piece after we made shot peening process. Our sequence decontamination of shot peening is to introduce the pieces in a bath of HNO3 50% with agitation for 15 minutes. This sequence, in principle, should be sufficient to eliminate the iron but is not the case. We don't know which may be the causes, contamination of shot, concentration of inadequate decontamination bath, whether we should have some intermediate step ... In addition we are unable to make any treatment as in the case of aeronautic many restrictions. What are the solutions for our problem ? And where it may be our fault? PLEASE
THANK YOU VERY MUCH
(EXCUSE MY ENGLISH)
QUALITY ENGINEER - ITALY
January 17, 2008
![]() |
A. Cut down your blast pressure and replace the shot more often. You are probably driving iron fines - tiny partials- into the aluminum. James Watts- Navarre, Florida A. Contamination is always a problem when shot peening. Boeing company use to dedicate a specific blast cabinet for this purpose, but even they use to have to purge it periodically to clean up problems and prevent contamination. ![]() AF Kenton retired business owner - Hatboro, Pennsylvania |
A. Sheila,
50% Nitric acid should be sufficient to decontaminate parts after shot peening. If 15 minutes is not sufficient time then simply extend the immersion time if it is practical to do so.
You may need to look at the analysis of the solution. If the solution is low in nitric acid that will explain why the process has slowed. You may also want to check the level of dissolved iron in the bath. If the bath is too heavily loaded this will prevent further iron from being dissolved. If this is the case the solution is to dump the tank and make up a fresh one.
Finally, check with your shot peeners about what sort of shot they are using and whether nitric acid is a suitable material to use for decontamination.
Aerospace - Yeovil, Somerset, UK
A. Another option would be to use a ceramic media like glass beads instead of steel. This would obviously entail different shot velocity, duration, etc. There is a lot of information available on shot peening in general, and glass bead peening of aluminum in specific.
Toby PadfieldAutomotive module supplier - Michigan
![]() |
A. If you cannot switch to a non-ferrous shot, citric acid based passivation solutions will remove the surface iron contamination. Let us know if we can help. ![]() Ray Kremer Stellar Solutions, Inc. ![]() McHenry, Illinois ![]() A. Shelia, North Tonawanda, New York |
A. CHANGE your sandblast media. Use plastic or glass particles to blast. With your actual sandblasting system use only 3 sec blasting.
Good luck
- Minneapolis, Minnesota, USA
A. I am not quite sure. But I think grit blasting can be used for decontamination.
Alan King- Kuala Lumpur
September 20, 2010

this text gets replaced with bannerText
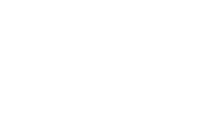
Q, A, or Comment on THIS thread -or- Start a NEW Thread