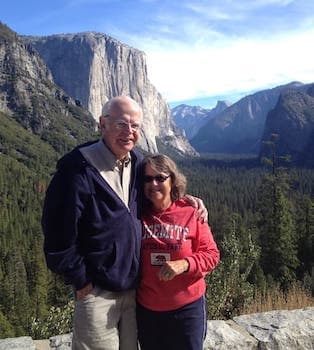
Curated with aloha by
Ted Mooney, P.E. RET
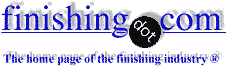
The authoritative public forum
for Metal Finishing 1989-2025
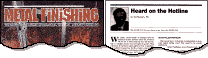
-----
Very Long Copper Plating Time
2005
I am with a medical device company. We copper plate 2 to 3 mil of copper on a relatively small ABS piece that has been copper struck. We use a copper sulphate/sulfuric acid copper plating solution in conjunction with a proprietary brightener.
The copper bath hadn't been used for about 1 month. I dummy plated the bath for about 12 hours for 3 days, adjusted the chemistry (CuSO4
= 220 g/L, H2SO4 = 58 g/L, Chlorides = 62 ppm, pH ~ 1) and added brightener per Hull Cell results.
Our problem is that the thickness we normally achieved in 4 hours is taking up to 10 hours! The bath wiring is good with very little resistance and the rectifier checks out with a multimeter (V and A). I suspect that not enough voltage is being pushed through the system, but have no data to prove.
Are there any other chemistry parameters I'm missing?
Are there any rules of thumb for bringing up a dormant plating bath?
Any advice would be greatly appreciated!
Thanks in advance,
medical devices - West Chester, Ohio
Faraday's Law of Electrolysis tells us that, if we ignore the inefficiency of liberating hydrogen, the amount of copper deposited is always directly proportional to the ampere-hours applied. If the efficiency had plummeted to 40 percent of its former value, I think you would be observing a ludicrous amount of gassing. So my theory has to be that either the rectifier is putting out only 40 percent of the previous amperage, or the item you are plating is 250 percent bigger, or you are (or were) mismeasuring the thickness.
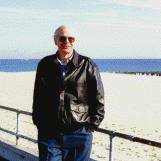
Ted Mooney, P.E.
Striving to live Aloha
finishing.com - Pine Beach, New Jersey
2005
Another possibility is that your connections and contacts are corroded and you are wasting a great amount of electricity that is going to heat before it ever gets to the parts.
After cleaning everthing possible, put a load on and check the voltage frequently from the powersupply lugs to the actual parts. Bet you fin a big voltage drop somewhere or a lot of little voltage drops.
- Navarre, Florida
2005
First of two simultaneous responses -- 2005
First, take the meter you are using and make sure that no shorts exist in the wiring,or that cooling or heating coils are not in the circuit, that there is good conductivity between connections (check resistance) and that the output on the rectifier is what it says. Next, check that the temperature is within the manufacturers specifications. Now, if we assume that you are using bagged anodes, did the bags harden and "crust up" during your downtime? If so, change them out following your suppliers recommendations. Stiff bags block the flow of solution at the anode and, to put it simply, slow down plating rate by inhibiting the "reaction" from taking place.
If all of the above are correct, get a D.C. Amprobe.
With a load in the tank, turn on the rectifier to the regular range. Using the amprobe check first near the rectifier to see if output is the same as indicated on the rectifier instrumentation. Second, check the buss/cable near the attachment to the anode bars (add up total of readings to equal that at the rectifier, a significant difference requires that you look for a break or bad connection in between. Next check the current at the anode bar and go to multiple locations on the bar. Total of mean reading of all bars should equal that of rectifier output. Again, if not as said, check connections. If large drop in current at various points on anode bar, check anode connections. I could go on.
A serviceman from your chemical supplier might be able to assist you in doing the above checks. BTW, have you checked with your supplier?
process supplier - Great Neck, New York
Second of two simultaneous responses --
My guess, after all the other suggestions, would be the anodes. If they've filmed up or the bags are plugged with sludge, salts, etc. the efficiency goes to hell and your plating time goes up. One way to confirm that it's not the solution would be a Hull Cell - it tests the chemistry and takes equipment concerns such as rectification, cabling, and anodes out of the equation. Another area that might be worthy of exploring are the condition of the racks - often the rack tip to spline connection (beneath the plastisol) becomes corroded but since it's hidden from view, it's often overlooked or forgotten.
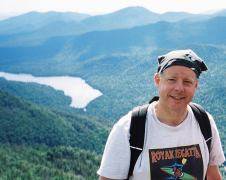
Milt Stevenson, Jr.
Syracuse, New York
2005
With the Hull Cell check bath efficiency with/without brightener.
It may be simple case of too much brightener.
- Mays Landing, New Jersey, USA
2005
All,
Thanks for all the great advice. One by one, I tried the suggestions.
New anode bags seem to have done the trick. My plating time is back down to ~4 hours and my voltage output at the rectifier doubled after changing the bags.
Nothing really popped at me upon examining the old anode bags. They were crusty at the tops with copper sulphate
⇦ this on
eBay or
Amazon [affil links] and black on the inside from the anodes, all typical though. I'm guessing that the bath level fell below the anode bags, which then dried out.
Thanks!
- West Chester, Ohio, USA
2005
Q, A, or Comment on THIS thread -or- Start a NEW Thread