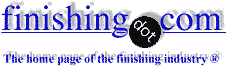
-----
E-coat racking designs to compensate for un-uniform coating across a rack
2005
We are an e-coat jobshop and are experiencing thickness variations on the same rack. We are aware that this is an issue inherent to the e-coat process, but we are also aware of the fact that some e-coaters design their racks to compensate for this issue. If anyone has any expertise in racking large quantities of small stamped parts on large racks and achieving a uniform coating, I would appreciate any information exchange you could afford.
Would raising the middle of the rack to create a downhill slope increase the amount of direct current hitting each part?
Are there any variables on our machine that can be adjusted to compensate for this issue? Our easily changeable variables are; slope, high/low input ranges, amount of voltage/amperes and time painted.
Any help would be greatly appreciated. Thanks
- McAllen, Texas
2005
What are the dimensions of your racks and what is the current way of loading them on conveyer? Is it hoist dip conveyer or a continuous running conveyer.
In my opinion you can change the slop of loading of racks on to the conveyer.
Design the loading pattern in such a way that whatever side of the rack dips first in the e-coat bath must come our first from the bath so that the residence time in the bath for whole rack's areas (bottom and top) remains same.
UL - New Delhi, India
Q, A, or Comment on THIS thread -or- Start a NEW Thread