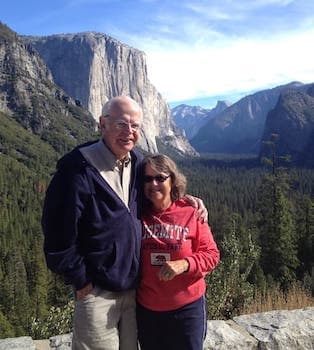
Curated with aloha by
Ted Mooney, P.E. RET
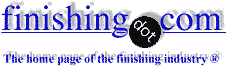
The authoritative public forum
for Metal Finishing 1989-2025
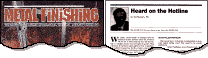
-----
Pin holes on plated zinc diecastings surface
2005
I work in a bathroom ware company as technical engineer in Hong Kong. We have several types of bathroom ware plated with Copper, Nickel and then Chrome. We always found pin holes on the same area. Initially, we think that pinholes is due to diecasting defect. However, from metallurgy, its looks like a plating problem.
-figure a. Pin holes always found at V-shape area as showed in pics.
-figure b. Micro photo cut through the defect showed the zinc substrate and copper layer is perfect but the nickel layer have rough surface finish.(etched 0.5% nital, original mag 500x)
-figure c-f. electroplating defects including a rough nickel layer(c)
and regions where the electroplating had lifted from the zinc surface or formed a blister(d-f)
Please kindly give advice and suggestions.
Alan ChanBathroom ware factory - Hong Kong
Ed. note: Sorry about the plating difficulty, but the upside is that your metallography department got a chance to show off their work. Fabulous micrographs!
Alan, in my opinion if the substrate does not have holes that Ni develops, at first sight appears the bath. Could be a filtration problem but also something with leveling additives.
Dan L. Rujan- Romania
2005
2005
Yes the photographs are amazingly vivid.
The pitting is on two counts, and there are various ways to overcome pitting. Antipitting agents are aplenty.
The plating of castings leads to a build up of impurity in the nickel baths, and firstly this nickel bath needs to be dummied and treated to reduce the pits in the inside regions.
The pits in the picture however seem to be products of a hydrogen bubble sticking to the part; this is on account of wetter/ additive being far less than the brightener in the bath, this normally shows up in all the areas, especially the recesses, so secondly the Additive:brightener ratio has to be changed to 3:1, irrespective of which chemistry you are using.
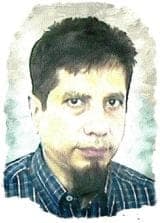
Khozem Vahaanwala
Saify Ind

Bengaluru, Karnataka, India
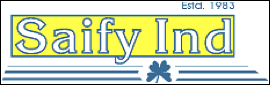
Hello,
I would suggest to concentrate on the base metal more to check with the casting process to reduce the porosity and also heat the component before the cleaning and plating process for 200 deg , 1 hour , and then clean ultrasonic , followed by soak cleaning no cathodic cleaning , and plate cyanide copper for higher thickness with very low current density.........hope you can reduce the pinholes.
thanks regards
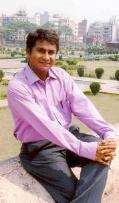
Praveen Kumar
plating process supplier
Mumbai, India
2005
2005
I think you have a dicasting problem. Try to heat treat them before plating in a oven at 200 °C for 2 hours and then plate them.
Regards,
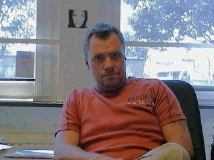
Anders Sundman
4th Generation Surface Engineering
Consultant - Arvika,
Sweden
Change Nickel Strike bath, all alkalines and acids, Low current density in copper and nickel tank, but before carbon treatment on nickel tank, check temperatures.
Carlos Carrera- Miami, Florida, USA
2005
I think you have a couple of problems that are not necessarily related. Firstly, the pitting in the nickel is probably due to insufficient wetter in the nickel bath and the effect is magnified by being in a quite inaccessible spot on the casting; alternatively, there could be insufficient movement of the electrolyte in this area, so increase the agitation. The second problem could well be in the quality of your diecasting. The excellent micrographs do not show this, but it does show detachment of the plating from the zinc. I would therefore go along with Anders' suggestion of a prebake. I would also ensure that the cleaning cycle is fully controlled with very good rinsing. I would also suggest a cyanide copper layer onto the zinc. I would advocate copper plating immediately after the cleaning stages and do not allow the diecastings to dwell in any rinses. Image d shows classical pitting of zinc resulting in adhesion failure; this implies the coating is porous or the cleaning is not very good. Image e is a bit more interesting - it looks like there may have been two attempts to plate the overlayers and that there has been loss of adhesion. This suggests that the initial problem MAY arise during the copper plating and therefore may be attributable to inadequate preparation and rinsing. Finally image f shows classical interfacial corrosion, almost certainly due to entrapment of a zinc-incompatible liquid such as a strong acid or alkali; this could be from the cleaning cycle and solution entrapment in pores.
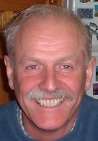
Trevor Crichton
R&D practical scientist
Chesham, Bucks, UK
2005
July 8, 2010
Hi All,
I am facing the same your problem about the pitting defect.
After the Copper Cyanide Strike & Bright Copper Pyrophosphate plating, we can see some pitting on the copper plating film.
However, we cannot find the pin hole of Zinc die cast substrate in x-section image. It look like the figure c, we saw the pitting at copper layer.
It's really make us difficult.
Do you have any comment for this problem. How to solve the pitting at copper layer.
Regards,
- HCM city, Vietnam

Q, A, or Comment on THIS thread -or- Start a NEW Thread