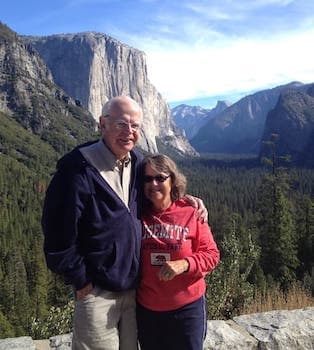
Curated with aloha by
Ted Mooney, P.E. RET
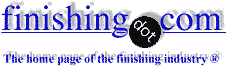
The authoritative public forum
for Metal Finishing 1989-2025
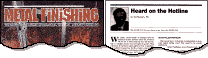
-----
Effect of SS316L metallurgy on electropolishing
Q. Greetings,
I've been working on SS316 electropolishing (EP) for some time. One of the interesting features is that the raw material can have some effect on the process, even if the material is routinely analyzed and certified by the supplier (A world class and renowned supplier by the way). I have seen that different stocks of raw materiel can behave quite different when electropolishing, even if they are processed exactly the same way (I have included extensive hot acid/alkaline rinsing in the process, it helps a little to avoid pitting, but it is not enough). For example, during manufacturing, parts running through EP from one specific heat number of raw material, electropolish beautifully having a very stable process. After a few weeks, when we switch to another lot (heat) of raw material, I know that I will have to adjust the process to yield desired results, otherwise I would have pitting. This wouldn't be much of a problem if adjustments were reasonably small, but in some cases, changes in the process would call for an official DEVIATION, which is very undesirable, practically unacceptable. What I normally do is work with the materials department to avoid that raw material and use it on manufacturing other products which are not so critical; all materials are high quality and certified anyway, but this is quite difficult to achieve sometimes, as raw material is very valuable and I doubt anyone can afford to buy many stocks just to have by chance the right one for electropolishing.
Now, the first thing I will try do is to explain what is the cause for this behaviour. I have read in this website and elsewhere that stock bars of raw material can show metallurgical differences regarding the orientation it was rolled in the mill (grains elongate in the rolling direction). I know the heat treatment supposedly will homogenize the grain size and shape, but in some cases, pitting is observed right in the direction of bar rolling. I am not the first to report this behaviour, See letters 15893 and 34414 on this website. Perhaps as someone said, annealing failed to reconfigure the morphology of the grains or precipitated carbides remained. In other cases the pitting is general and no directional appearance is observed, but in most cases (not all cases) it can be corrected by increasing current density and lowering EP time respect to the
'standard procedure'.
Right now I have samples of 6 different heat numbers of raw material, I have documented how is their behaviour during EP, and I plan to make polished sections of the three rolling axis (namely X-Y-Z) of each sample and take it to a metallurgical laboratory for metallography. I wish to observe grain size and shape, grain boundaries, carbide inclusions, sulfide and other impurities inclusions if existent. You may think this is just a small R&D project, but it is going to consume a lot of time, effort and maybe some resources. If we are able to determine what stockbar characteristics influence the EP process, maybe we can work with the supplier so we can always have the best material for electropolishing.
So, Peers, I would very much like to hear your comments on this matter and advice would be extensively appreciated, specially whether this effort is justifiable or not or maybe someone else has already done this study. Maybe I am being too naive, but some people regard the reason for this behaviour is not known and accept it just like that (See letter 34414).
TCM - Hermosillo, Sonora, Mexico
2005
A. The electropolishing of stainless steel can be batch dependent due to differences in the surface condition of the steel. This includes the ratio of metallic components actually on the surface of the metal; this can be significantly different to the bulk composition because of different processing conditions. Furthermore, there will be differences in the metal oxide layer covering the stainless steel. This can be due to how it has been processed, stored and how old it is. The process of electropolishing is an attempt to create a uniform electrochemical surface (aka equipotential) so that there is a reduced opportunity for a galvanic cell to be created and hence reducing the chance of promoting localised corrosion.
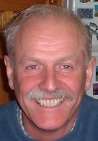
Trevor Crichton
R&D practical scientist
Chesham, Bucks, UK
2005
A. Manuel, lets divide the possible variations into two parts- those variations dealing with surface finish (as suggested by Trevor) and those due to bulk properties of the material. Are you electropolishing machined parts, or as received forgings or castings? If you are doing EP on machined parts and getting lot related variation, then any difference among your material lots would not be due to anything the processor did to the surface, such as burnishing.
There certainly can be variations among different lots of 316. It would be far more likely to be a material lot problem if the different lots were supplied by different mills (the firm that melted it, not the one that rolled it into bars or the one that warehoused the material- they are often different.) (When you say "supplier", whom do you mean?) Carbon content and inclusion content can vary among mills, as can ingot solidification and homogenization practice, which can have great effects on the amount of micro-segregation.
So, I believe your study to be worthwhile, if you are electropolishing machined parts. If you are electropolishing as-received surfaces, then I believe you need to examine the surfaces for the cause of variations.

Lee Gearhart
metallurgist - E. Aurora, New York
2005
Q. The parts I electropolish are first machined, then mechanically polished with 400 grit abrasive, Then prepared for EP and finally EP'd.
Manuek Sández [returning]TCM - Hermosillo, Son. Mexico
2005
Effect of electropolishing on SS316L metallurgy
Q. We have an instance where Machined and Fabricated Davit Bases manufactured to Grade 316L have had a change in the metallurgical structure away from the Specification to now suffering a reduction in the Nickel Content of over 2% and the Molybdenum down from 2% to 0.18%
Is this possible as a direct result of Electro Polishing or any other Factors
- Seven Hills NSW Australia
Q, A, or Comment on THIS thread -or- Start a NEW Thread