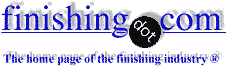
-----
2nd coats for powder coating system
I have been using an inexpensive powder coating rig to apply a finish to golf clubs. I have noticed that powder coating inherently has an orange-peel type of finish. Which is pretty much unacceptable on a golf club head.
I have had great success by coating, wet sanding, then polishing the head. But.........it only works on basic colors. Apparently, whenever you use a metallic color, all the metal flake floats to the top during the flow out period, and when you sand it, you just snd it right off. Leaving a black finish.
So, as a result, I need to apply a clear coat of powder. One that I can sand and polish.
Now, here's the problem. All my attempts at applying a second coat are not working. There seems to not be enough juice to ground out throught the first coat. So the second coat is sparce and uneven.
My question is this. Is this because I have an inferior rig? Would buying a rig that uses more voltage solve this problem? Right now, I think it uses 9kV.
Thank you for your time and insight.
- Austin, ,Texas, United States
2005
2005
Dear Nicholas,
Industrial powder coating is carried out at 50-80Kv resulting in 2-3 mls film weight. Applying a second coat requires the Kv to be lowered
(40Kv) to overcome application problems. One trick you may wish to investigate prior to purchasing alternative equipment is heating the powder-coated item and then applying your second coat. The powder will melt onto the items already coated and reasonable film weights can be achieved.
Birmingham, United Kingdom
2005
Thank you, Terry, for your advice. I will give it a shot.
You know, I have had some success by simply not charging the powder, and letting gravity do the work. The powder comes out at such a low pressure that it makes a suitable cloud that covers the part pretty well. And way better than if I were to charge the gun.
I know it sounds unusual, and probably never something you would do with a professional rig, and I end up having to do a bit more sanding, but at least it makes for a professional looking end-product.
Thank you again for your time and advice.
- Austin, Texas, United States
Q, A, or Comment on THIS thread -or- Start a NEW Thread