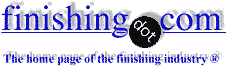
-----
Aluminum question
Just did a batch of motorcycle fender spacers. They are about 2" wide, 4" long and 1" thick with rounded ends. The 2" wide sides and the rounded ends are exposed in use, and that is what I polished. Sort of.
They had fairly deep machining scratches on them. I worked my way back thru greaseless compound grits, 'til I found that I had to start with 80 grit to get rid of the existing scratches in a reasonable time. It worked fine for this purpose.
BUT, as I finished up with my 320-grit, it became apparent that the surface I had been working on has an orangpeeled-lookng surface. I couldn't get ahold of my customer so I went ahead and polished them, but did not drop back and try to sand them flat to get the ornagepeel out - I had enough time in them already and was not about to completely do them over for the same (small) price I quoted him.
He's disappointed but paid for the work. If I had known this would happen, of course I would have used another tool and sanded them flat before anything else. But, my question is, how could the orangepeel appear after I did all that with the greaseless to remove the heavy scratches?
I'm no metallugist but it almost seems as though the aluminum had areas of lesser and greater density; the greaseless took more out of the softer areas, hence leaving the orangepeel effect. Anybody else ever see this? If my theory is true, then if I had started with a flat sanding (belt or whatever) it probably would not have happened.
Any thoughts?
Plating - Hackett, Arkansas
2005
First of two simultaneous responses --
I'm not an expert in metal polishing by any means. But I know that I personally with my lacking skills was able to accomplish the same thing as you I believe.
I think it resulted from my leaving the buffing wheel in an area for too extensive of a time in an effort to get that "perfect shine". Instead it ended up with a crinkled semi-warped surface appearance. You describe it as a orange peel, what I looked at was more like when you take a dropper and put a few drops into a glass of water. Its that spreading wavy effect on the surface.
Did it feel smooth, but varying in surface height, in other words you had a lot of dips and valleys?
Now, mind you, I'm not a polisher, I'm not an expert in polishing techniques, but what you describe sounds exactly like what I did, and maybe my relating to you, can help draw some conclusions for you to find a possible solution
If so then I think what the solution might be would be to stay away from an area to such a extreme that the heat build up from the buffing causes such a thing to occur.
Of the top of my head, maybe attaching a secondary heatsink to the part to help distribute some heat away from the "hot spots" would suffice?
plating company - Toledo, Ohio
2005
Second of two simultaneous responses --
Sounds like a badly mixed alloy.
Either Zinc or magnesium mostlikely.
Sand it slowly or hand finish it.
Slightest heat will probably make it grow pores.
Seen it many times on motorcycle pieces.
polishing - Belfast, Maine, U.S.A.
2005
Question your question. Did you make/machine these parts from raw material or did you try to polish already made parts? If parts were already made, it is common for fastener companies to tumblast these parts in which case they very well take on shot peen characteristics.
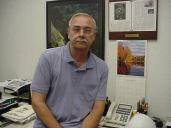
AF Kenton
retired business owner - Hatboro, Pennsylvania
2005
Q, A, or Comment on THIS thread -or- Start a NEW Thread