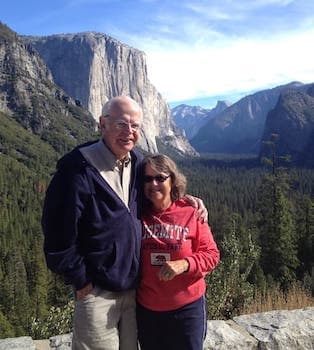
Curated with aloha by
Ted Mooney, P.E. RET
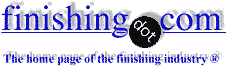
The authoritative public forum
for Metal Finishing 1989-2025
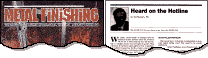
-----
Can you explain ASTM B 117-90 salt spray (fog) testing?
Q. Dear Sir,
Anybody could tell me what's " ASTM B117-90 SALT SPRAY TESTING" for zinc coating ? What's the specification for testing? Time? Coating thickness?
Thanks
Johnson Electric - Shanghai, China
2005
First of three simultaneous responses --
A. Hi Sandy,
ASTM B117 is a standard that describes all of the details on how to conduct a salt spray test. I suggest to obtain a copy of the standard; you will find the answers to your questions there.
- Naperville, Illinois
2005
Second of three simultaneous responses --
A. Hi Sandy,
ASTM B117 is a document that describes how to run a salt spray cabinet. It describes pH, specific gravity, collection rate, flow rates, temperatures, pressures, etc. -all of which are associated with the proper maintenance of a salt spray cabinet.
What it does NOT tell how long any part should last in salt spray, nor does is tell what is considered a passing test. Those parameters are set by you, if you are the company whose products are to be tested.
- Naperville, Illinois
2005
Third of three simultaneous responses --
A. Hi Sandy!
ASTM B117 is a document, available from ASTM International, (formerly the American Society for Testing and Materials) that gives 10 pages of instructions on "How To Run A Salt Spray Test". Ten pages is a lot to try to fit into a paragraph answer, so the best I can do for you is urge you to buy the document from ASTM, who can be found on the web at www.astm.org.
Now, B117 does NOT give accept/reject criteria: it merely tells how to do the testing. Hence it won't say how long to test for, nor how thick your zinc plating must be to pass, nor whether it needs to be chromated or not, etc. It is just "How To Run A Salt Spray Test", nothing more.
Good luck!

Lee Gearhart
metallurgist - E. Aurora, New York
2005
Q. Hi,everyone,
I am Sandy , the inquirer for the above question.
Thanks to all who answered concerning my question. But I am still confused about the ASTM B117. From all the answer published above, I know ASTM B117 is one standard for salt spray testing which tells how to do the test. I am wondering that "90" of this standard indicates the time for testing at salt spray is 90 hours? or any other meaning?
Any difference between B117 and B 117-90?
I really appreciate all help from all of you.
Thanks
Johnson Electric - Shanghai , China
2005
First of two simultaneous responses --
A. "-90" indicates that it was last revised in 1990.
James Watts- Navarre, Florida
2005
Second of two simultaneous responses --
A. Hi Sandy,
The "-90" indicates the year that the standard was revised. In this case, it would have been 1990.
- Naperville, Illinois
2005
Q. In reference to Bill's reply. What is typical acceptance criteria for salt spray testing. Is there qualitative methods to determine the amount of rust? Is it typically a visual inspection? Is there any visual aids on-line? Thank you.
Rodney Stringham- Orchard Park, New York
2006
A. Hi Rodney,
There really aren't many visual aids to help with this fog test (not that I know of at least). However, visual inspection is often more than enough. The end-point of the test is often user-driven. Some examples are:
a) first sign of white rust (when testing effectiveness of zinc coatings)
b) first sign of red rust (lets you know that the iron in the product is corroding which can be used as a failure limit)
c) 5% red rust which often can be considered to compromise the strength of the material in question.
It depends really.
- Vancouver, B.C, Canada
November 14, 2008
Q. Hi
As per my knowledge, SST chamber has to run for 24 HRS a day as per standard. But in case it is running for 10 HRS a day and opening at a single time only within 24 HRS a day
I would like to know
1) which will be the more severe testing 24 Hrs/ day or 10 hrs/ day
Regards,
sunil
- nashik, Maharashtra, India
August 27, 2012
Hi Sunil. I would expect 10 hours per day to be more severe because the parts will be in the test chamber for 2.4X as many days.
But regardless of what you think or I think, tests don't have any merit if they include uncontrolled variables. This is just food for thought, not a scenario I fully embrace, but consider:
We already know that salt spray testing is a poor way of comparing one type of coating against another type of coating because it doesn't take real world corrosion mechanisms into account. For example, galvanizing is the most proven of all finishes, with real-world structures that have been protected for a hundred years in bad conditions ... yet galvanizing performs poorly in salt spray testing. It performs poorly because real world protection by galvanizing depends upon the formation of tough zinc carbonate corrosion products which develop in the open air as the result of interaction with carbon dioxide, but cannot develop in a closed chamber. If we now open the chamber every day, letting carbon dioxide laced air in, what has happened? Have we given galvanized finishes the fresh air they need? Probably not, but who knows?
Regards,
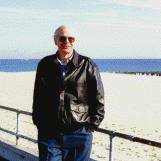
Ted Mooney, P.E.
Striving to live Aloha
finishing.com - Pine Beach, New Jersey
August 27, 2012
Q, A, or Comment on THIS thread -or- Start a NEW Thread