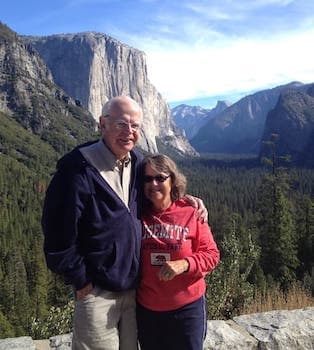
Curated with aloha by
Ted Mooney, P.E. RET
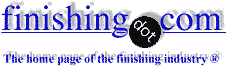
The authoritative public forum
for Metal Finishing 1989-2025
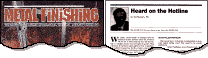
-----
Trivalent chromate color
We are assisting our connector manufacturer in becoming RoHS compliant but can't get consistent answers from platers. Is trivalent chromium clear or does it have a black color? Does the color depend upon what the plating underneath it is?
Thank you.
connector distributor - Cleveland, Ohio, USA
2005
2005
Trivalent chromate ia a new family of conversion coatings of chromate for zinc free Cr +6.
The color depends on you wish, blue, clear, iridiscent with dye or without, black.
Best regards.,
- Toluca, Mexico
2005
I imagine that you can't get consistent answers due to the fact that there is no one single answer. While I haven't done any trivalent chromating yet (still waiting for something to get on the QPL for MIL-C-5541 before switching over) I have been reading up on some of the alternatives. There are clears, golds and yellows, I believe I came across 1 that was blue... To complicate the matter further some of the trivalent options involve top coats, and I've no idea what color those dry to. And, finally, whatever is underneath the coating would almost certainly affect the final color, especially if the trivalent itself was a clear.
As a disclaimer, I've only researched the chromates for Aluminum, everything I have to say may or may not be relevant to your situation
- What are you having the chromate put on?
Ted Mooney has been saying for a while that there should be a standardized color system to allow differentiation between hex and tri coatings - so far however that has not been the case. Ultimately you either have to get everything in writing and stated clearly (and trust your suppliers) or you have to start sending stuff out for testing.
Good luck!
Compton, California, USA
The majority of trivalent chromates on zinc are clear to clear blue. One is greenish, one is yellow and many are dyed to yellow. One or two may be black. On zinc alloy plating there are more trivalent yellow and black finishes and less clear/blues.
Most trivalent blacks have a sealer to enhance color and corrosion protection. This is true of some clears and yellows. Also, dyed parts may not be UV color fast.
process supplier - Great Neck, New York
2005
2005
Now let me get this straight - you can't get straight answers from
"platers" and so you come to a finishing site typically responded to by "platers" to get a straight answer. Doesn't this sound strange to you? The only thing stranger are the myriad of responses platers are getting from their supplier community when they ask the same question. If you're not getting the "straight" answer you have two possibilities: (1) your plater is crooked or (2) your plater doesn't have the "straight" scoop from their supplier. My guess is the later!
The previous responses are pretty solid technically. My shop's trivalent chromate process for aluminum is CLEAR, however, it's really not entirely a chrome compound but a ceramic like conversion coating which happens to contain some small amount of trivalent chrome. Denser and tighter than conventional yellow chromates on aluminum, known by their trade names Alodine or Iridite, this new trivalent chrome coating (based on US Navy patents) can't be dyed and clear is all you'll get!
With trivalent chromates over zinc, the suppliers are changing their formulations to allow them to build up thicker and thus adsorb more coloration. Some are done with dye added directly to the otherwise clear chromate to get a yellow / gold coloration (very close to conventional hexavalent chromated zinc) while others go thru a separate dye stage. The blacks we've worked with are done with a black dye that only partially blackens the zinc. To get a deep black, most are given a subsequent black pigmented "sealer" which is wax or otherwise organically based.
This is as straight an answer that this plater can give you. Hope these various responses straighten out your various options!
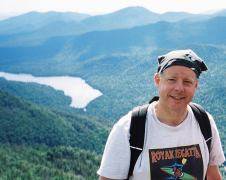
Milt Stevenson, Jr.
Syracuse, New York
You will have to pick a plater that can supply you with samples. I am on our company RoHS team and have been chasing the tail around the world. We have seen Trivalent with a clear to a blue hue over the zinc. This is for sheet metal components and I do not know what it would look like on hardware since one is plated in a tank and one in a barrel. For us, coatings are out of the question due to conductivity issues and I would assume hardware would be the same.
Suppliers for platers have their own different mixes and therefore will have different results and of course there is the salt spray to contend with. Some platers state they can achieve 100 hours until I remove the ASTM specs off our drawings and replace it with what we are looking for ie, CLEAR (or YELLOW) TRIVALENT TO WITHSTAND 100 HR SALT SPRAY,
FINISHED PART TO BE ELECTRICALLY CONDUCTIVE.
I am then told it can not be done without a coating.
For the present we have settled on clear with a 12 hr salt spray. Good luck if you can get a straight answer.
Power Supply Industry - Hackettstown, New Jersey
2005
Q, A, or Comment on THIS thread -or- Start a NEW Thread