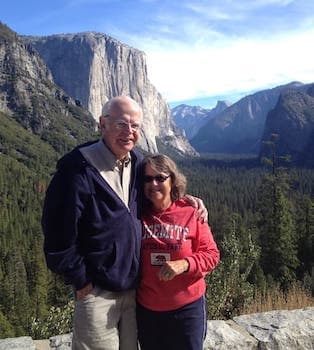
Curated with aloha by
Ted Mooney, P.E. RET
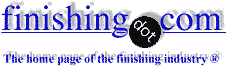
The authoritative public forum
for Metal Finishing 1989-2025
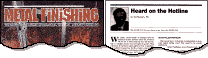
-----
Need reference info on calcium treatments to aluminum
2005
We have an old (40+ years) finishing specification for small instrument components made of aluminum. It was developed by Westinghouse a long time ago and remarkably, we still use it. It is supposed to impart a non-conductive finish on the parts, but it is not very scratch resistant, nor is it very effective at insulating the surface. It is a calcium "lime" finish. We etch the parts (NaOH), bright dip them (nitric or a nitric, sulfuric and salt solution), then boil them in Calcium oxide and plaster of paris for 15 to 45 minutes. Then we ultrsonically clean the excess lime off the part.
I am trying to convince my boss to switch to a sulfuric anodized surface, but he is ever reluctant to change the old Westinghouse specs. He also thinks the lime finish is as good as anodizing. Finally the question: Is there any reference info on the AlCa- hydride or oxide or hydroxide finish where could learn more about its properties. I do plan on proving the anodizing is better with simple testing of scratch resistance and dielectric strengths, but would like some background info also.
Regards,
instruments - Coral Springs, Florida
I can't imagine why you would want to open the Pandora's Box of anodizing when you have a process that works for you.
The lime finish may be an easy way to remove residual acid from the bright dipping, thus preventing problems of leaching of the acid after the parts are shipped out of the finishing department. This process may allow you to use aluminum with a porosity and finish that is cost effective.
Changing to anodizing will introduce many problems that will not improve your product or your operation.


Tom Pullizzi
Falls Township, Pennsylvania
2005
Q, A, or Comment on THIS thread -or- Start a NEW Thread