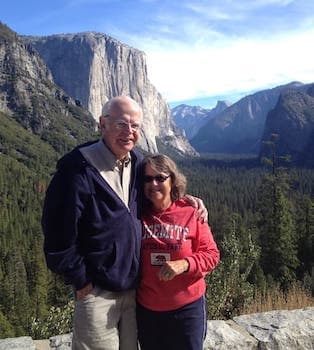
Curated with aloha by
Ted Mooney, P.E. RET
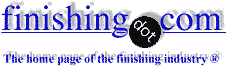
The authoritative public forum
for Metal Finishing 1989-2025
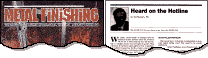
-----
Calculation of Cascade rinse water consumption
We want to calculate rinse water consumption and flow rate for alkaline zinc and silver passivation plating unit , plating tank 3 cub m , plating area /h =0,8 sqm /h
H.Yenigün- Turkey
2005
Unfortunately there are still two unknowns after you provide all of the information that is available. The first is the dragout rate, and it's virtually pointless to even attempt an estimate based solely on surface area, as is explained in Kushner's "Water and Waste Control for the Plating Shop" ⇦[this on eBay, Amazon, AbeBooks affil links].
The second unknown is what contamination level in the final rinse tank will prove satisfactory. Again, it's hard to say, and can depend on other things, but the ratio 1000:1 is occasionally mentioned. In a cascade rinse tank this can be achieved with 33 parts of water. (If you dilute the dragout 33:1 in the first rinse, and dilute the dragout from the first rinse by 33:1 in the second rinse, you've got 1000:1; and in a cascade rinse you use the same 33 parts of water in both rinses). So, if you take a stab at the dragout rate, based on shape and production rate, and multiply by 33 you will have a rough (ROUGH!) estimate of rinse water requirements. Good luck!
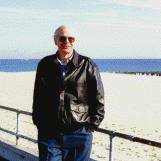
Ted Mooney, P.E.
Striving to live Aloha
finishing.com - Pine Beach, New Jersey
2005
2005
Sir: I have published 2 or 3 articles on rinsing and draining in
Metal Finishing that would be useful to you. I know factually that in Hot Dip Galvanizing that for two counter-current rinses and an off-line storage tank that 0.5% sulphate is equilibrated in the flux solution from sulfuric acid pickle containing 28% sulphate. Thus about each week all of the more contaminated rinse (R1) is put into the off-line storage tank; the cleaner second rinse (R2) is put into the now empty R1 tank and new water is put into the now empty R2 tank. During the week, rinse water in the storage tank is used up due to evaporation in the hot sulfuric acid tanks (usually 3 acid tanks at 150F). Also the steel product is dipped twice in each rinse tank to remove "adheared" acid adjacent to the steel and to help remove "bridged" and "cupped" acid on the product. This process is repeated again and again to equilibrium. My articles explain this with drawings and diagrams.
Regards,
Galvanizing Consultant - Hot Springs, South Dakota, USA
----
Ed. note: One of Dr. Cook's articles is referenced in our on-line article "20 Ways to Reduce Water Usage in Plating Shops".
What I want to know is what is the recommended maximum TDS/PPM/Conductivity for processing tank rinses? Right now I am teetering somewhere between 1000 & 2500 PPM before recharging my drag-out rinses. What DO the experts say?
Bill Coxplating shop- Compton, California, USA
September 24, 2008
Hi, Bill. We appended your letter to a previous thread which somewhat addresses it. There is no right answer for what TDS or PPM is acceptable, it's all empirical, but shooting for a dilution ratio of about 1000:1 between the concentration in the process tank and the final rinse would be a good starting point. The term 'drag out rinse' often implies a first rinse which will be returned to the process tank; this must be allowed to grow high enough in concentration that you can get at least some of it back into the process tank.
Regards,
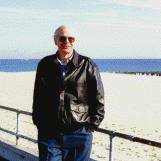
Ted Mooney, P.E.
Striving to live Aloha
finishing.com - Pine Beach, New Jersey
September 26, 2008
Q, A, or Comment on THIS thread -or- Start a NEW Thread