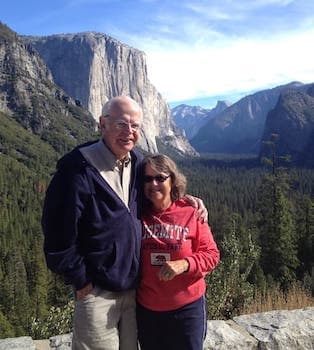
Curated with aloha by
Ted Mooney, P.E. RET
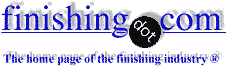
The authoritative public forum
for Metal Finishing 1989-2025
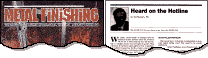
-----
Maximum Chromic Acid Anodize Thickness?
Q. Does anyone know what the maximum thickness of chromic anodize is on 6061-T6? I've always been of the opinion that the maximum thickness is .0001 inches. Recently, I was told that the coating can be .0005 inches thick. What is the correct answer? Also, if the coating can be built up to .0005 inches thick, could you provide me with the process parameters (CrO3 concentration, voltage, bath temperature, anodize time, etc.) necessary to achieve this thickness?
Blair Smithaerospace - Windsor Locks, Connecticut
1999
A. Blair, it has been our experience that a serviceable coating thickness for Chromic Acid Anodize can be .0002" to .0003" Maximum thickness. The main process parameter to be manipulated is the Chromic Acid Anodize Temperature. Raising the electrolyte temperature to 110 °F. has a substantial effect on the achievable coating thickness. Thicker Chromic Acid coatings are effective when using Chromic Acid as a mask for Hard Anodizing; but there is a fine line between a thicker Chromic Acid Coating being thick and also still serviceable. It would be important to know why you need and/or want a thick Chromic Acid coating.
Joe Hillockanodizing shop - Philadelphia, Pennsylvania
1999
Chromic acid anodizing of Al7075 T7351
December 1, 2011Q. Hello,
I'm a process engineer in a metal coating facility in Israel.
We're constantly encountering a problem when anodizing Al 7075 T7351 parts according to MIL-A-8625 / MIL-PRF-8625
[⇦ this spec on DLA] Type I. The coating thickness we get is significantly lower than required. What's curious is that exactly the same process, with identical conditions produces excellent results for a normal Al 7075 (without the T7351 part).
We tried to lower bath's temperature, increase voltage, lower voltage etc.
Lowering temperature gives slightly better results, but not by much.
Perhaps it's more a matter of pretreatment? A more aggressive etch required? What really is the difference between the normal 7075 Aluminum and Al 7075 T7351?
Thank you,
Olga
Process engineer - Israel
February 3, 2012
A. Olga,
MIL-A-8625 doesn't specify a thickness for Type I Chromic anodize except to make reference to the .000020" - .0007". More important than thickness is the coating weight (200 mg/square foot minimum) and the corrosion testing. If you meet both of those then thickness is a moot point.
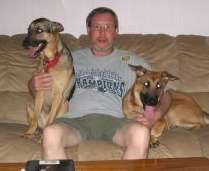
Tim Hamlett, CEF
- West Palm Beach, Florida, USA
April 4, 2014
Q. Hello,
This query is regard to the Chromic Acid Anodizing process.
When I process 10" x 3" x 0,032" panels, made of 2024-T3 UNCLAD Aluminium, I just get a coating thickness of 2'2 micrometers, which is too low.
I want to increase that thickness, but I do not know what to do for it.
Requirements:
Bath Concentration, Free Chromic Acid 51-54 gpl
Temperature 39-41 °C
Time in Minutes 35-45
Voltage 38-42
Total Hexavalent Chromate 50-127 gpl CrO3
Chlorides 0,2 gpl max
sulphates 0,5 gpl max
Aluminum in electrolyte 10 gpl max
What can I do for increasing that thickness? With this actual thickness, it would be impossible to pass the Salt Spray Chamber.
Thank you!
- Taiwan
A. Hi Mark,
2.2 microns of anodize is plenty to pass a 336 hour salt spray in accordance with ASTM B117, provided it is sealed properly.
Dependent on which specification you are working to the seal should either be hot (greater than 96C) distilled or demineralized water or dilute hot (greater than 96 °C) sodium or potassium dichromate solution.
I have successfully got 2024 through with as little as 1.3 microns, so check your sealing process out first.
Aerospace - Yeovil, Somerset, UK
April 10, 2014
Q. Dear Sir,
I have a requirement of achieving CAA thickness as minimum 3 microns for Aluminium AA2024 T3 and AA 7175 T7351. My present bath is able to achieve in between 2 to 2.5 microns. Please suggest what can be done to increase anodizing thickness.
Readings achieved in between 2 to 2.5 are by eddy current measurement (by Electrophysik & Fischer). The AA 2024 T3 specimens processed at 40 Volt cycle and AA 7175 T7351 at 20 V cycle. Suggestions requested.
guruprasad sambayyamathaerospace processing - Belgaum, Karnataka, India
March 27, 2015
Q, A, or Comment on THIS thread -or- Start a NEW Thread