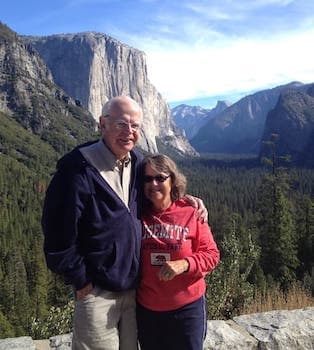
Curated with aloha by
Ted Mooney, P.E. RET
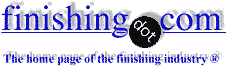
The authoritative public forum
for Metal Finishing 1989-2025
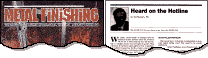
-----
Tank suitable for sulfuric, nitric and phosporic acid for anodizing
We are manufacturers of Hardware items and we do anodizing in our unit, we have a problem that the chemical contains sulfuric , nitric and phosphoric acids and it will be heated at 100°C, the tank we use now is an SS tank and we have to change the tank every 6months as the tank is getting spoiled due to holes as the chemical is eating the tank, can I get a suitable tank which I can use it permanently.
Jeevan PrashanthYesses Anodizing Industries P Ltd., - Anantapur, Andhra Pradesh, India
2005
2005
Hi Jeevan !
Heating tank to 100 °C ! That's HOT.
Have you considered any plastics? If, if, if what you say is true, then the only plastics which will take that temperature are the weldable fluorocarbons and PVDF.
PVDF would be my choice. Less cost. OK to l40 C. Even higher if constructed as a dual laminate. Superb acid resistance (but not on high alkalis).
This tank must MUST be made by a specialist dual laminate plastics fabricator.
Doubtless the tank will fume nicely ... so what duct materials to use? Initially, ie. close to the tank, I'd opt for PVC:FRP and then, away from the radiant heat, I'd switch over to good old PVC.
But sometimes I WONDER who specified stainless for your chemistry !
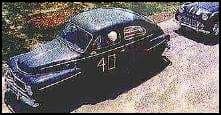
Freeman Newton [deceased]
(It is our sad duty to advise that Freeman passed away
April 21, 2012. R.I.P. old friend).
2005
I missed the use on the first time thru-- It is an bright dip tank.
SS is the normal recommended material. Use 316 LC (low carbon) for the tank and use 316 ELC (extra low carbon) for the filler rod.
Do not attempt to underfire heat the tank. Most people will use a double wall tank with insulation between the walls.
Life should be 2-3 years for a well constructed tank, possibly longer if it is very well built and maintained.
- Navarre, Florida
I think I agree with both Freeman Newton and James Watts on this one. I agree right down the line with James' spec for a metal tank on brite dip and its life expectancy. But I have to say that, as expensive as PVDF tanks are, they probably would be worth it if they work. Replacing a 316L double-walled tank every 3 years is an expensive proposition; and if you don't catch it in time, even more so.
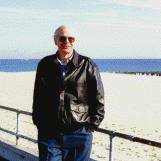
Ted Mooney, P.E.
Striving to live Aloha
finishing.com - Pine Beach, New Jersey
2005
Q, A, or Comment on THIS thread -or- Start a NEW Thread