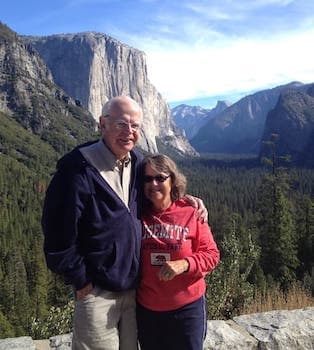
Curated with aloha by
Ted Mooney, P.E. RET
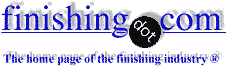
The authoritative public forum
for Metal Finishing 1989-2025
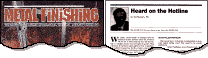
Thread 368/79
Chromating of Zinc-Nickel Plating: Q&A
Q. What is the formulation for hexavalent chromium coating for zinc nickel alloy plating.
Karim laput hamzah- Kepala batas, pinang, Malaysia
April 26, 2024
publicly reply to Karim laput hamzah
⇩ Related postings, oldest first ⇩
Q. Dear Sirs,
I want to know what is Zinc-Nickel (Clear) Trivalent Plating, and what is different between this and clear zinc plating only.
Please help me.
owner - Shenzhen, Guangdong, China
2005
publicly reply to Nick Poon
A. Hi, Nick.
Steel components are zinc plated for corrosion resistance, but the zinc plating itself is subject to early corrosion (white rust). To prevent white rust, zinc plated parts invariably receive a post treatment which traditionally was a hexavalent chromate conversion coating, either thin (clear), thicker (yellow), or thickest (olive green).
Because of concern over toxicity, and RoHS and WEEE standards, it is common today to employ trivalent chromates instead of the traditional toxic & carcinogenic hexavalent chromate post treatment. Most of these are inherently clear.
Zinc-nickel is an alloy plating (usually proprietary and available from the major plating process suppliers) that offers better corrosion resistance than plain zinc plating. The chromating process is somewhat different because the conversion reaction proceeds somewhat differently on the alloy. The proprietary supplier should be consulted regarding available colors, and presence or freedom from hexavalent compounds. Good luck.
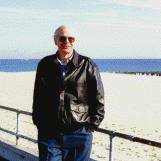
Ted Mooney, P.E.
Striving to live Aloha
finishing.com - Pine Beach, New Jersey
publicly reply to Ted Mooney
Zinc plating with chromate: What is the nature of the finish?
Q. When zinc chromate plating is applied to steel, the zinc is electrically deposited, and then the part is dipped in a chromate solution. What is the nature of the bond between the chromate and the zinc?
Dave Butkamolded rubber parts - Bridgeport, Connecticut, USA
2005
publicly reply to Dave Butka
for Shops, Specifiers & Engineers
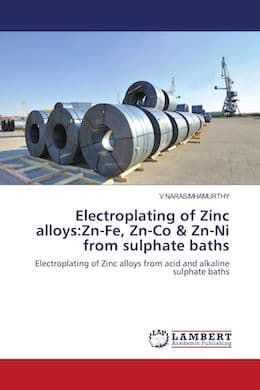
from eBay, AbeBooks, or Amazon
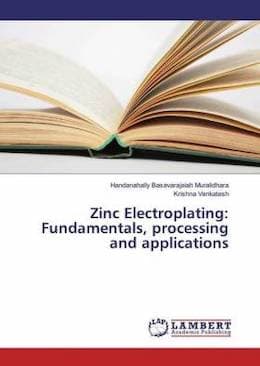
from eBay, AbeBooks, or Amazon
"Alkaline non-cyanide zinc plating with reuse of recovered chemicals" by Jacqueline M. Peden (1994)
from (U.S. EPA)
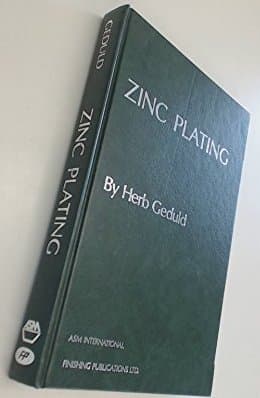
from eBay, AbeBooks, or Amazon
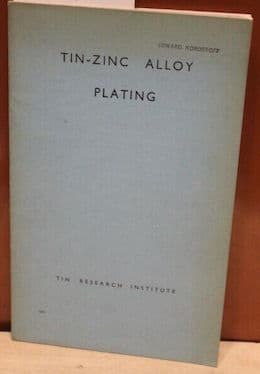
from eBay, or AbeBooks
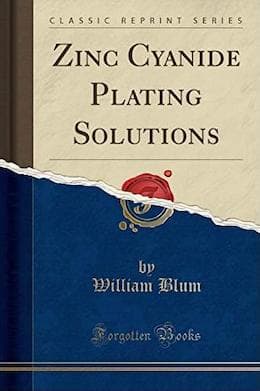
from eBay, AbeBooks, or Amazon
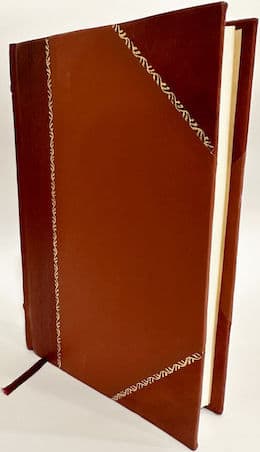
from eBay, AbeBooks, or Amazon
(as an Amazon Associate & eBay Partner, we earn from qualifying purchases)
A. Hi,
The film that is formed on the freshly plated zinc surface is a chemically formed one when the zinc metal dissolves in the chromate passivation solution. The Zinc chromate is a complex gel structure with zinc oxide and chromium oxide with water molecules. The hexavalent chromium present in the film is a corrosion inhibitor especially under high humidity conditions. The film gets stabilised after 24 hrs of aging. Until then the film is very soft and is susceptible to mechanical damage. The different colors that appear are due to the light incident on the bright zinc surface through a translucent chromate film of varying thickness. It is also called rainbow passivation or iridescent yellow passivation. The film loses its corrosion-resistant property when it is subjected to heating above 60 °C due to the loss of water molecules.Hope this information helps you.
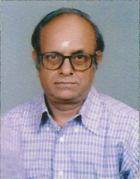
Subramanian Ramajayam
consultant - Bangalore, India
publicly reply to Subramanian Ramajayam
Q. Hi Subramanian,
Are you suggesting that if any zinc plated+passivated parts stored around 60 °C (with the high humidity), the corrosion-resisting property of the plated part will disappear and the part will start to corrode quickly?
We have some white/red corrosion problem with our yellow zinc plated & passivated nutserts inserted to 316L SS parts shipped from Malaysia where the parts are stored in a container a certain period of time (2 days to 1 week) after assembly. I assume that the temp inside the container may reach to 50 °C to 60 °C easily in summertime and that together with the high humidity may trigger the parts to corrode prematurely on the way back to Australia as per your theory?
Any comment(s) ?
- Brisbane, Qld, Australia
2005
publicly reply to Alex Kultur
A. Probably an issue in the plating.
There's many Hexavalent plated zinc bolts (such as in cars' engines), that get to that heat and higher that are 30 years old and the hex chromate is still present despite it being old and dirty.
- Western Australia
March 18, 2023
publicly reply to Boris Siljanoski
A. Hi,
I largely agree with Boris about the longevity of hex chromate finishes, but I would note that in an engine compartment the bolts tend to have a bit of oil on them and are largely protected from sun & rain. Plus, we have photos on line here of old parts which were zinc plated & chromated and are now brown; whether they were originally olive drab or yellow I don't know, but I don't think new chromate was ever brown, so I think some deterioration took place.
As for Alex's "white/red corrosion problem", zinc plated and chromated steel is not galvanically compatible with stainless steel; being connected in this way, the large surface area of the stainless steel will cause rapid corrosion of the zinc plated steel if it is wet, and I would suspect that parts not being bone dry is probably the specific "issue with the plating".
Luck & Regards,
Ted Mooney, P.E. RET
Striving to live Aloha
finishing.com - Pine Beach, New Jersey
publicly reply to Ted Mooney
Q. My question is about the corrosion resistance of the Trivalent Zinc -- i.e., salt spray versus Electroless Nickel or Cad. The salt spray requirement is 240 hrs @ 5% solution. The components are carbon steel and will be used in the Fire Protection industry. Complete coverage is a must and the sleeves must withstand crimping with no cracking or flaking of the plating. Also, are there other coatings on the market that will offer the above that are cost effective and environmentally friendly.
Mack McPeeters- Greensboro, North Carolina
2006
publicly reply to Mack McPeeters
A. Hi Mack. Cadmium is a cumulative toxin similar to mercury and lead and should not be used unless the situation is extraordinary and the combination of properties offered by it is essential.
Electroless nickel is a fine finish, but is neither malleable nor is it a sacrificial coating, and and it is much more expensive than zinc or zinc alloy plating .
A zinc alloy plating is probably good, and tin-zinc may be better than the alternatives when crimping is involved. 240 hours should not be a problem for a well applied proprietary zinc alloy plating with suggested proprietary chromates.
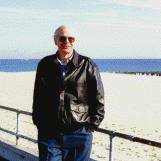
Ted Mooney, P.E.
Striving to live Aloha
finishing.com - Pine Beach, New Jersey
publicly reply to Ted Mooney
Q. In reference to Zn-Ni Trivalent Chrome plating: when or how does the toxic gas become dangerous? Is this during the plating process or is it simply during the handling of the parts at the end-user's location where the part would continuously emit a toxic gas?
Elizabeth Nerness- Windom, Minnesota
January 21, 2010
publicly reply to Elizabeth Nerness
A. What toxic gas is that, Elizabeth?!
Zinc-nickel plating with trivalent chromate conversion coating emits no toxic gas at any time. It is possible that a couple of different things might be confusing to you.
If the chromate conversion coating plating were the more old-fashioned hexavalent chromate, that thin "gel" on the parts might be considered carcinogenic -- although billions of components of all types were hexavalent chromate conversion coated for decades, including the overwhelming majority of the world's screws, washers, nuts and bolts. Due to source reduction efforts, RoHS, etc., hexavalent chromating is rapidly becoming rare, and the replacement technology, trivalent chromate, is not considered carcinogenic -- in fact, trivalent chromium percolinate is sold as a supplement in health food stores.
Chrome plating (as opposed to chromate conversion coating on top of other platings like zinc-nickel) is usually conducted in a bath of chromic acid. The process generates a great deal of hydrogen gas bubbles, which can (if not properly managed) convey tiny droplets of the chromic acid into the air during the plating process, similar to how champagne or ginger ale bubbles can carry those products into the air. This chromic acid solution is toxic and carcinogenic, and proper fume suppressants and/or ventilation and fume scrubbing systems are required to capture those droplets. Once a chrome plated surface is rinsed, it presents no dangers to the end user.
Get back to us if this was unclear.
Regards,
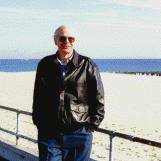
Ted Mooney, P.E.
Striving to live Aloha
finishing.com - Pine Beach, New Jersey
publicly reply to Ted Mooney
Q. Thank you for your response!
So in summary, the Hexavalent plating is dangerous to people in and around these parts such as an automobile? Or is it only overemphasized and not really a problem?
Regards
- Windom, Minnesota
publicly reply to Elizabeth Nerness
A. Hi, Elizabeth. You're playing your cards close to the vest. I still don't know what you mean by "hexavalent plating" (chromium electroplating vs. hexavalent chromate conversion coating on zinc-nickel plating), or where you are trying to go. Please tell me what you're trying to determine and why, and hopefully I can respond more directly and less confusingly.
There are potential dangers everywhere, but if we weigh the danger of unreliable automobiles when proper corrosion-resistant finishes are not applied, against the minor concern of someone potentially touching hexavalent chromated automobile parts (which surfaces people have been touching for 60 years or more), there is no comparison. But yes, the world is trying to move away from hexavalent chromate conversion coatings, replacing them with trivalent chromate conversion coatings because they are less toxic.
Regards,
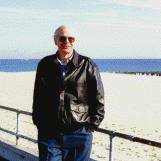
Ted Mooney, P.E.
Striving to live Aloha
finishing.com - Pine Beach, New Jersey
publicly reply to Ted Mooney
Q. Hi Ted,
I'm sorry for the confusion. Please allow me to start over.
We have a product in which we are told that the metal parts need to have a "coating of Zinc-Nickel electrolytically deposited on our ferrous metal surfaces from alkaline baths where corrosion protection treatment is required." "A supplementary hexavalent chromium free coating and/or trivalent chrome may be applied."
1. Does this mean that the Hexavalent chromium free coating offers the same protection from corrosion & from being a danger to people as the Trivalent chrome does?
2. Is the Hexavalent chromium free coating basically a Zinc-Nickel plate with a topcoat?
3. Are the costs of both of the platings (hexavalent chromium free coating and trivalent chrome) very similar? Or is the trivalent chrome process a substantially higher cost? Thank you!
Elizabeth
- Windom, Minnesota
publicly reply to Elizabeth Nerness
A. Thanks, Elizabeth; I understand!
Zinc-nickel plating, like plain zinc plating or other alloys of zinc, requires a supplementary post-treatment to prevent tarnishing, white rust, and early corrosion. In the old days, hexavalent chromate conversion coating was the post-ytreatment of choice.
After RoHS regulations and other concerns about the toxicity of hexavalent chromates, and intense development efforts, the choice for the last 5-10 years has been to use a trivalent chromate conversion coating (which might also be called a hexavalent-free chromate). These trivalent chromate coatings, when done with a supplementary topcoat after them, are now as corrosion resistant as the old hexavalent chromate coatings, maybe even marginally more so. Yes, this new generation of trivalent chromates plus top coats is a bit more expensive than the old hexavalent chromates, but not greatly so, and the question is moot because that's all you'll be able to find in the future anyway.
There is talk of conversion coatings with no chromate at all, not even trivalent chromate, but they are probably not a robust and practical solution at this point.
Regards,
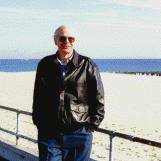
Ted Mooney, P.E.
Striving to live Aloha
finishing.com - Pine Beach, New Jersey
January 24, 2010
publicly reply to Ted Mooney
Q. We currently Cyanide Cad plate for the aerospace industry. Our line consists of the following process tanks (850 gal cap):
1 soak clean
2 alkaline clean
3 HCl pickle
4 Nickel strike (if required)
5 CN Cad plate
6 neutralize
7 yellow chromate
We have counterflow rinse between each process tank. We have no electroclean tank.
Within the next 10 to 12 months we plan to add Non-Cyanide Zinc and Zinc/Nickel plating processes. Because of space limitations we would like to do this with as few additional tanks as possible.
For our pre-plate cleaning cycle, will we need to add an electroclean tank?
For the post-plate yellow chromate conversion coating, Will we require three different yellow tanks or will one formulation handle all three processes?
Thanks
Lab/Facilities Mgr - Denton, Texas, USA
April 24, 2010
publicly reply to Lee Blanton
A. Hi Lee. Cyanide is a great cleaner, so electrocleaning was probably not mandatory for your cadmium plating process, but it's pretty much required for non-cyanide plating. Your step "2" can perhaps be converted to electrocleaning.
I doubt that you will find a chromate that can be used on more than one plating let alone all three :-(
Luck & Regards,
Ted Mooney, P.E. RET
Striving to live Aloha
finishing.com - Pine Beach, New Jersey
publicly reply to Ted Mooney
A. You are doing work for the aerospace industry, so I guarantee it that your aerospace customer(s) has a specification that you need to comply with. That specification(s) tells you exactly which solutions are approved for your use, what order they need to be performed in, and what the concentration should be run at. You really will have very little choice in the matter.
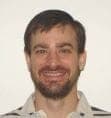
Jon Barrows, MSF, EHSSC
Independence, Missouri
April 30, 2010
publicly reply to Jon Barrows
Q. I am wondering about the plating that is on fasteners (bolts nuts, screws) you can buy at most hardware stores. The bags and boxes say zinc plated, but my guess is that they are more likely trivalent chromated coatings. My question is how temperature resistant are these coatings. Will they fume off at less than 750 °F. My understanding is, no, since the boiling point of the zinc chromate is way higher than that. I want to use these fasteners inside my bbq grills, and I can't seem to get a straight answer anywhere I look. No food would be in contact with any of these fasteners ... just charcoal, and some other metals, such as the edge of a steel walled drum.
Thanks,
Dave
- Rochester, Minnesota
June 22, 2011
publicly reply to David Trotter
A. Hi, Dave. Zinc plating is the least expensive plating, so, in the absence of specs -- i.e., just buying hardware off a shelf -- it's probably zinc plated. Zinc plating requires a chromate conversion coating or it would get white rust almost immediately. Traditionally, this was based on hexavalent chrome because it is inexpensive, extremely reliable, and highly corrosion resistant. But trivalent chromating has become more popular in recent years due to European RoHS and automotive requirements, and technical improvements which increased its corrosion resistance. These days much hardware now receives trivalent chromate, but to assume that a given box in the hardware store has trivalent chromate would probably be a leap. A few years from now it will probably be a safe bet.
To my knowledge there are no specific laws stating what hardware you are allowed to design into your line of BBQ grills (except that if they are sold in Europe they probably can't have hexavalent chromate conversion coating).
These days I would not use anything with hexavalent chromates.
Millions of people get food poisoning every year from the food they put on their grill; sometimes it's very severe. Contrariwise, I don't think there is any evidence that zinc plated, chromate conversion coated assembly hardware in a BBQ grill has ever endangered anyone. I'm not saying that no epidemiologist should look into the subject, but I don't think that any ever has. And I think that those of us who are charged with coming up with designs in a world of finite resources and where every possible construction material has downsides and potential dangers, can lean on pragmatism.
It's fine to seek a straight answer, but you won't find a world with no shades of gray, no differing circumstances, and no second guessing ... and my take is that zinc plated and chromated fasteners are fine. They will not withstand 750 °F, they will rust, but are used nonetheless. If the design can bear the cost, stainless fasteners would be better.
Regards,
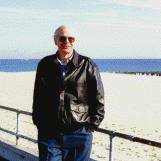
Ted Mooney, P.E.
Striving to live Aloha
finishing.com - Pine Beach, New Jersey
publicly reply to Ted Mooney
Q. Hi, my name is sudharshan from Bangalore, India. I have a problem in zinc nickel trivalent plating. We are doing Zn-Ni plating with clear passivation. After the clear passivation the components gets some yellow shades also with clear appearance, why is that? What may be the problem? Please tell the answer in a practical way. Thank you.
Sudharshan VelusamySurtec chemicals - Bangalore, India
February 21, 2019
publicly reply to Sudharshan Velusamy
A. Hi Sudharshan. Please send some clear photos of the problem to mooney@finishing.com for inclusion here.. Unfortunately, trying to clearly understand what something looks like from a brief description is problematic. Could be a stain, a reaction, a discoloration in the process chemical, a thin-film interference/iridescence pattern; trying to ascertain the possible causes of such an unknown appearance is moving towards hopeless :-(
Please tell us whether the zinc-nickel plating process is acid or alkaline, barrel or rack, and a purchased proprietary or home-brew. Thanks!
Regards,
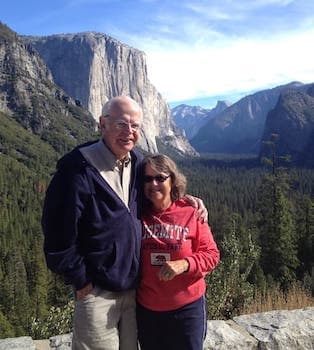
Ted Mooney, P.E. RET
Striving to live Aloha
finishing.com - Pine Beach, New Jersey
February 2019
publicly reply to Ted Mooney
Q. Alkaline zn/ni trivalent barrel plating ...
Surtec chemicals - Bangalore, India
February 24, 2019
publicly reply to Sudharshan Velusamy
Q. How thick is Clear Trivalent Chromate coating? I have a customer requesting a part be Clear Trivalent Chromate coated. It has a note on the drawing that all dimensions apply after plating. Normally I wouldn't care but I have a bore that is +/-.0005" so I could easily be undersize once the part is plated.
Thank you for your help.
- Cincinnati, Ohio
January 8, 2021
publicly reply to Tim Strasser
A. Hi Tim. I don't actually know the answer, and it probably depends on what proprietary trivalent chromate and what proprietary sealer are used. But chromate coatings are thin, and one way of answering is that I think you'll find the variation in the zinc-nickel plating thickness to be much larger and harder to control, such that the chromate thickness will be roundoff error. What is the spec for zinc-nickel plating thickness?
If I misunderstood the question, or you're not understanding me, please get back to us and we'll get it sorted out.
Luck & Regards,
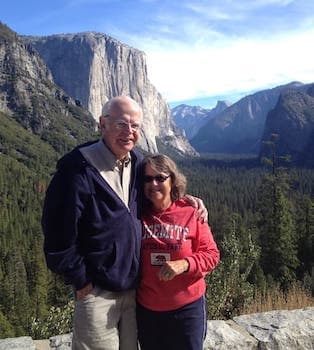
Ted Mooney, P.E. RET
Striving to live Aloha
finishing.com - Pine Beach, New Jersey
publicly reply to Ted Mooney
A. The thickest trivalent passivates are about 900 nanometers. 0.0005" is 12,700 nanometers. As Meher Baba said (so did Bobby McFerrin) "Don't worry, be happy."
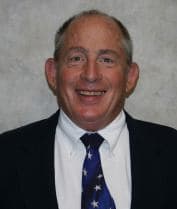
Tom Rochester
CTO - Jackson, Michigan, USA
Plating Systems & Technologies, Inc.

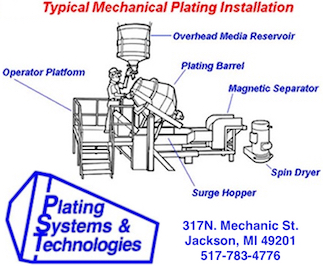
publicly reply to Tom Rochester
Q, A, or Comment on THIS thread -or- Start a NEW Thread