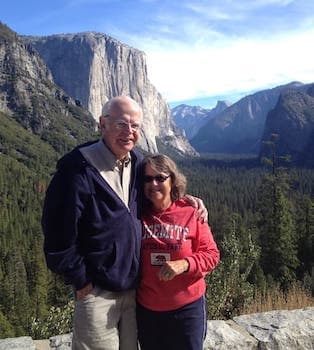
Curated with aloha by
Ted Mooney, P.E. RET
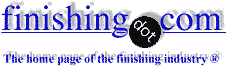
The authoritative public forum
for Metal Finishing 1989-2025
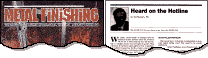
-----
Salt spray testing of hot black oxide parts

![]() ![]() ![]() ![]() ![]() ![]() |
Ed. note: This section of the dialog actually ended up not being about black oxide, so we have put it into a sidebar which can be skipped by readers interested in black oxide. After it's no longer a current topic which readers may be tracking we will move it to a "zinc & black chromate" thread. Q. My company's standard is no white rust at 24 hours and no red at 48 hours. hardware buyer - Clearfield, Utah January 10, 2022 A. Hello Heidi. The thing is, if this is a steel rivet that has been hot black oxided, it contains no metal that can/will form white rust (aluminum, zinc plating, etc.). So a spec with time to white rust would make no sense in that case :-( On the other hand if your black rivet is in fact not hot black oxided but is actually zinc plated and black chromated instead, it can certainly form white rust. Please try to tell us exactly what these black rivets are made of and what process steps blacken them. Luck & Regards, ![]() Ted Mooney, P.E. RET Striving to live Aloha finishing.com - Pine Beach, New Jersey January 2022 January 12, 2022 Q. The rivet is mild steel with black zinc coating, clear coat with wax.
Heidi Moulton [returning] A. Hello again Heidi. Zinc plating with black chromate is a very different finish than the hot black oxide discussed on this page. But 24 hours salt spray to white rust is a very relaxed specification. 96 hours, 192 hours, and even more is sometimes specified, even without wax or other clearcoat. I suspect that if you are not specifying the required plating thickness, or requiring plating to a particular spec like ASTM B633, that your platers are probably doing the minimum plating thickness they think they can get away with, like 0.00012-0.00015" thickness, which may be preventing the chromate from properly developing and offering the protection that it ought. That problem does look to me more like wax than white rust, but two thoughts: try to remove it with acetone ⇦ this on eBay or Amazon [affil links] Warning! highly Flammable! or other wax solvent, and ask the vendor to pull a few parts before the wax step. If you test them and they fail you'll know what you are seeing is not wax, if they do not fail then what you are seeing is only wax :-) Luck & Regards, ![]() Ted Mooney, P.E. RET Striving to live Aloha finishing.com - Pine Beach, New Jersey January 2022 February 3, 2013 Q. I purchase hardware fasteners for our company. We have always used a C6 coating on parts that require black zinc coating and we require a minimum surface protection of 48 hours in salt fog. This forum is fairly new to me so please excuse me if I misinterpret any information. We sell to big retailers that now require C3 trivalent. We have tested some new parts and they are failing at less than 24 hour in SF. We do call out ASTM standards for parts and must pass 48 hr but we have had two tests fail so far. I am thinking we are not calling this out correctly or it should be combined with a sealer or top coat of some kind. Can you tell me typically what works to get a C3 to go 48 hours in SF or more? - Clearfield, UT A. Hello Heidi. I am not familiar with "C6" or "C3" coating specifications, and assume this is just a shorthand for hexavalent chrome and trivalent chrome? When one switches from hexavalent chromate to trivalent chromate, yes, it is necessary to put a 'sealer' on after the chromate (except to my understanding when 'thick film' trivalent chromate is used) ... but this sealer would not be wax or other organic coating but the specific silicate, zirconium or other topcoat that is part of a symbiotic proprietary sequence specified by the supplier of the plating chemicals. I am surprised that any plating shop would not know of the need for this, so I suspect that you are having some communication difficulties with the shops. If you additionally want it waxed for some reason, that would come after the proprietary topcoat. A potential problem with not requiring compliance with an ASTM or other accepted specification is that such standards call out what comprises passing or failure. Without that how do you determine what comprises 'failure' in the salt spray test so that your vendor's inspectors and your inspectors and your customer's inspectors will agree? And how do you say whether your vendor's plating is thick enough, etc. You can write your own spec, or the plating shop can write theirs and you can accept it, but with no spec saying what comprises salt spray test pass/fail, and no other spec, things are loose enough that contract disputes may ensue :-) Luck & Regards, ![]() Ted Mooney, P.E. RET Striving to live Aloha finishing.com - Pine Beach, New Jersey January 2022
Q. What coating thickness should be requested if you want no surface change after 48 hours? That's not our exact spec required but I know it makes our engineers really happy when they see no change. Heidi Moulton- Clearfield Utah January 17, 2022 A. Hi again. ASTM B633 describes 4 thicknesses: 5µ for mild service, 8µ for moderate, 12-13µ for severe service; 25µ for very severe. A general problem that I have seen for years is that if you do not specify anything, plating shops will often apply only 3-4µ and call it 'commercial thickness' although they just mean no spec at all :-) I don't think you should have a problem getting 48 hours from 5µ with a good trivalent chromate and topcoat. Luck & Regards, ![]() Ted Mooney, P.E. RET Striving to live Aloha finishing.com - Pine Beach, New Jersey January 2022 |
⇩ Related postings, oldest first ⇩
Q. 1. My customer requests our blackened parts go for salt spray test, and they found white rust came out within one day.
2. The customer put the parts in air conditioned machining room; after 3 weeks, the white rust started appearing.
They reject my parts because it cannot pass the above mentioned test.
Are they performing a reasonable test?
Also, after antirust oil is removed from the surface, we found reddish rust, especially at the corners. The oil removing process is ULTRASONIC, 60 °C, using TCE.
What is the reddish rust, and how to prevent it?
automotive component manufacturer - MALAYSIA
2005
A. Please use lacquer coating process to protect the surface. Solution of lacquer coating (30% with 70% water v/v) can be purchased easily from any chemical supplier.
Above process can pass 24-hour salt spray test for sure. Anyway, need to know what is your requirement for salt spray test? 24-hour, 48-hour,
72-hour or 100-hour? We have another good solution for passing 100-hour salt spray test.
Good luck,
plating - KL, Malaysia
2005
Q. Kaka Ryuuichi,
My customer did not state the requirement, but they not allow any coating/spray/film on the part. Note: bare part with black oxide surface to go for spray test.
What is your suggestion if the part is brake piston, made of SUM24L?
- Melaka
2005
A. Hi NG. It sounds like a misunderstanding to me. It is well known that removing the oil from a black oxide finish reduces it to essentially zero corrosion resistance. It may flash rust before it even gets to the salt spray chamber :-)
SUM24L is, I believe equivalent to AISI 12L14; I believe it is very rust-prone.
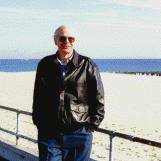
Ted Mooney, P.E.
Striving to live Aloha
finishing.com - Pine Beach, New Jersey
2005
![]() |
Q. Follow on to Ted Mooney's comments, with reference to MIL-DTL-13924
[⇦ this spec on DLA] para. 3.9, "...The black coating, of class 4 (300 series only), prior to the application of a preservative, shall show no signs of corrosion after 96 hours of exposure in the salt spray test..." - Singapore April 2, 2009 A. Hi, Zainal. Please note that NG & I were talking about steel parts whereas the section of the spec that you are quoting is talking about stainless steel. Black oxided steel parts have no corrosion protection without an oil or wax, but black oxided stainless steel parts are still stainless steel. Yes, a chromic rinse will help, but then you may run into RoHS issues, and you must of course follow the spec. Regards, ![]() Ted Mooney, P.E. Striving to live Aloha finishing.com - Pine Beach, New Jersey April , 2009 |
Q. Dear sir,
I have a similar issue on the black oxide steel parts - screw /bolts /nut which are heavily used in the assembly unit. However, we are facing the rusty issue the moment the product reaches oversea customer (by sea).
No doubt the parts with black oxide come in some oil, but upon handling, the oil layer may be reduced/removed. Should another anti-rust oil be able to solve the rust issue? Or any good oil /wax that can be applied/painted on the screw?
I have done Salt Spray Testing ASTM B117 on the incoming black oxide steel screws and after 24 hours it starts to show rust. What is the right testing hours for black oxide steel as salt spray test process may wipe out the wax/oil during the process.
I am stuck with the solution as what is the right salt spray test time to test and what is the best solution/chemical/wax/oil to prevent black oxide steel from rust.
- Penang, Malaysia
May 18, 2011
A. Hi, Hussain. There are two facts that need to be accepted to address your issue:
1. Black oxide has essentially no corrosion resistance at all. Without oil on it, it can flash rust in a couple of hours, maybe less.
2. Salt spray testing is not intended to predict survival time in real life. Rather it is a QA method designed to let you know if a process that was formerly working correctly has gone south and is out of control. (If you traditionally achieved xx hours of salt spray, and suddenly you achieve much less, something has changed on you).
When you attempt to use a salt spray test to try to predict the real-world anticipated life of an oil or wax, and ask how many hours to test it for, you are not going to solve the problem. The way forward is to pick a reputed corrosion resistant oil from a reliable supplier of black oxide chemistry, and prove to yourself and your customer that the treatment meets his real-world needs. Then you salt spray test it to determine how many hours this proven process should resist. Then you periodically salt spray test it, and a red flag goes up if the salt spray hours significantly decrease.
Shipping by sea is another matter, and will probably require special packaging. Good luck.
Regards,
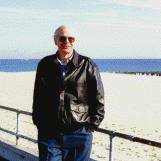
Ted Mooney, P.E.
Striving to live Aloha
finishing.com - Pine Beach, New Jersey
May 19, 2011
June 12, 2011
Thanks Ted.
In short the black oxide is a low corrosion resistance and salt spray test is not suitable and should not be used to determine the corrosive resistance as it is fact is low corrosive resistance.
As the shipment undergo weeks of shipment to the customer, the black oxide may not be the best plating solution to avoid such rusty issue upon receiving the parts,
Thanks
- Malaysia
Q, A, or Comment on THIS thread -or- Start a NEW Thread