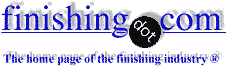
-----
Delay in the initiation of electroless plating
2005
One of our clients is doing electroless plating of steel components. It is an acidic hypophosphite reduced plating bath "self brewed" not a commercial bath. The components are high carbon steel
(1 wt.%).
When using freshly prepared electroless plating bath, the time for initial plating reaction is delayed. In some instances they have to wait for 6 hours. Once the plating reaction is initiated the plating proceeds without any problem. Even in subsequent loadings also there is no problem in the plating. Only with the freshly prepared solution this problem is occurring.
Temperature, pH and other process control parameters are monitored and found to be well within the range.
This problem is not noted when a dealing with a small volume bath solution and low loading. Now the bath volume and loading is increased to 3-3.5 kgs in 180 liters.
Freshly prepared phosphating baths require a break-in and usually some iron filing are added to the fresh bath. Is there anything like
"break-in" in electroless plating bath?
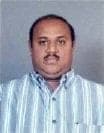
T.S.N. Sankara Narayanan
- Chennai, Tamilnadu, India
(ed.note: The good doctor offers a fascinating blog, "Advancement in Science" )
That is the problem with a homebrew, no tech service people to go to. It sure sounds like an excess of a stabilizer that is preventing the initiation of plating until temperature and time are burning off enough to allow plating to start. You could use a DC current for a few seconds to start the plating and see if it would continue by itself.
James Watts- Navarre, Florida
2005
2005
If it is taking minutes or hours for plating to begin, the adhesion of the coating to the part will be very very poor.
The long initiation period for the start of plating is probably due to an excessive amount of stabilizer (like lead, Thiourea
⇦ on
eBay
or
Amazon [affil links] , or iodate)in the bath. It is poisoning the reaction so that the part will not plate. Over time the stabilizer is absorbed onto the tank and parts and is lowered to a level where plating is possible.
Try reducing the stabilizer content of the bath. Also increasing the area of parts in the bath (bath loading) may help.
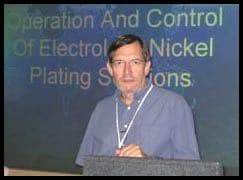
Ron Duncan [deceased]
- LaVergne, Tennessee
It is our sad duty to note Ron's passing on Dec. 15, 2006. A brief obituary opens Episode 13 of our Podcast.
Let's learn together, don't you think Mr. Narayanan? What stabilizers and complexors and how much of them is your customer using? What else is he adding to his brew?
Guillermo MarrufoMonterrey, NL, Mexico
2005
James is right. First of all, don't use homebrew EN. But if you must, then start with a DC current for a few minutes.


Sara Michaeli
Tel-Aviv-Yafo, Israel
2005
2005
In my opinion, there is nothing wrong about using a "home brew" formula, as long as the concentration parameters are maintained and controlled. I very much understand your position, since it is not feasible in some countries to find a factory made brew that is economical; that is our case.
I am sure your stabilizer content is too high. Please take into consideration that some of the constituents of the formulation, usually already contain some heavy metals. If you add a stabilizer and not take this into consideration, then the bath will be too slow.
I suggest, that after the previous cycles (cleaning) for you to introduce a steel part with a large surface area at low temperature
(say 70°C to 80°C), for at least 12 hours. Once you pull out the part check for the quality of the plating.
If you find skip or step plating, then you need to repeat the process. If not, then add the required amount of constituents to reach the required concentrations and carbon filter the bath for at least 12 hours.
This has worked for us.
Best regards,
- San Antonio de Los Altos, Edo. Miranda, Venezuela
Q, A, or Comment on THIS thread -or- Start a NEW Thread