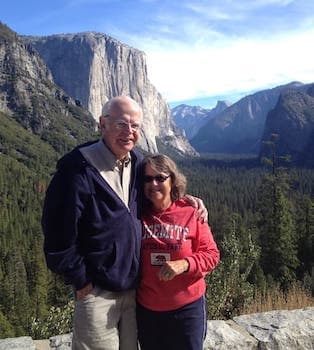
Curated with aloha by
Ted Mooney, P.E. RET
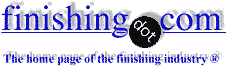
The authoritative public forum
for Metal Finishing 1989-2025
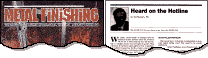
-----
Corrosion pits on 5005 H14 sheets after Alkaline Etch
2005
Good day all,
We are an anodizing shop and using as part of our process a caustic tank with the following data:
Free NaOH = 55 to 65 gr/l, Total NaOH = 130 gr/l, Temp = 135 F, we use an additive to prevent sludge formation and to give an even etching.
I have been using this without any problems for more than 20 years. However, during the couple last weeks, we have been experiencing a problem. When we etch for 15 minutes (5' × 5') 5005 H14 sheets, we observe a formation of microscopic corrosion pits all over the surface. Examination of the surface after etch and rinse shows pits white powder. After anodizng however, these pits become darker.
I am wondering if anyone had a similar experience and how it was dealt with. What kind of contaminant might cause corrosion on aluminum alloys in the alkaline etch.
PS: The sheets, look perfect prior to and after deoxidizing (initial step of the process)
Your answers and input are very much appreciated!
Regards,
anodizing shop - Verdun, QC, CANADA
1. Is there any Chloride in the solution, possibly as NaCl impurity in the cuustic?
2. Can you measure a galvanic voltage between the external load basket/bar and the tank?
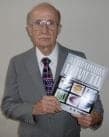
Robert H Probert
Robert H Probert Technical Services

Garner, North Carolina
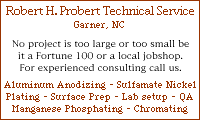
2005
2005
Hi all,
Thanks Robert for the answer.
Let me please answer your questions in reverse order.
2. as far as the galvanic voltage is concerned, we DO make sure that the tank as well as the heating/cooling coils are well grounded. We learnt this at our expense back in 1998. After making some maintenance work on the air scrubber, somehow our tank either lost a previously existing ground or gained some kind of positive voltage. After that the tank (made out of mild steel) was just dissolving at a high rate. This problem almost ruined us because it was not identified soon. We were making up a new caustic bath every 3-4 days. After getting enough Fe2+, F3+ in it no matter how much sulfide we added it was never enough. Luckily, the interior of the tank became shinier during the second week and that led us to understand the origin of the problem and cure it by making a good and permanent grounding on the tank.
1. Now, as of the first question relative to chloride contamination, the answer is as follows:
a) The certificate of analysis of the raw caustic did not show any evidence of excessive chloride (1.2% max, since it is a diaphragm caustic).
b) I am at loss in finding a fats and wet method to perform the test for chloride in this type of medium (very alkaline pH>14)
c) I am failing to see why would Cl- have any impact on aluminum in this rather aggressive medium towards aluminum of course.
In summary: I would appreciate any input as of a fast testing procedure for chlorides in alkaline media.
I reiterate my sincere thanks.
Regards,
- Verdun, Quebec, CANADA
2005
This might work. Take a 1 ml sample. Add 100 mL DI water and lower the pH to under 10 with nitric acid. This should take about 1 mL of
1N NaOH. Add 1 ml of K2CrO4 as an indicator.(20 grams in 980 mL of water for the stock solution--This will last a long time ,so consider a smaller amount). Titrate with 0.1N AgNO3. Endpoint is a rust colored orange red that will last for several
(30)seconds with agitation. Cl in oz/gal = mL x 4.727 x N (N in this case is 0.1)
- Navarre, Florida
First of two simultaneous responses --
OOPs, I meant 1 mL of nitric acid, nor NaOH.
James Watts- Navarre, Florida
2005
Second of two simultaneous responses --
1. Take a meter and measure the voltage between the work load and the tank. In the presence of chloride this will etch.
2. I recall the case when I serviced a nail plating facility in Mexico where barrels of nails were pickled in Hydrochloric acid then rinsed two times then dipped in caustic soda (which had been neutralized down to pH 1.0 by drag in), then right into the zinc plating tank. So much chloride had dragged right into the alkaline zinc plating tank that the steel anode baskets dissolved.
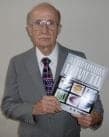
Robert H Probert
Robert H Probert Technical Services

Garner, North Carolina
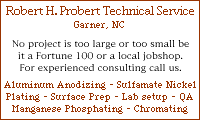
2005
Q, A, or Comment on THIS thread -or- Start a NEW Thread