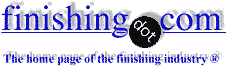
-----
Hard anodized aluminum wire as heater coil support
Q. All,
I'm interested in using a preformed, hard anodized aluminum wire (.002+) to support a resistance wire heater coil, where the stretched coil is threaded over the aluminum wire, which is then mechanically held in place. Visualize the aluminum wire in the shape of a light bulb exterior, with the coil occupying the bulge portion. The coil would be at least twice the diameter of the wire, therefore loose on the aluminum.
A typical heater coil might run brown to red hot, at temperatures as high as 1400 °F degrees, and carry voltage of 240 VAC, referred to the mechanical attachment point. There will be some natural relative motion, coil to wire, due to moderate vibration and the effects of coil shrinkage and growth when cycling from cold to hot. In qualifying vibration, think of something automotive, say the trunk of a car.
Assuming the wireform is either electro-polished after forming and prior to anodizing, or is blemish free after forming, can I expect at least 1000 volt breakdown and 30,000 hours of normal operation?
- Arden, North Carolina
2005
2005
A. Wow! 1400 °F ! Fine cracks start forming at about 80 to 100 °C (which is only 212 ° F). Cracking is caused by the low coefficient of expansion of the anodic film (Aluminum Oxide) which is approximately 0.2 times that of the underlying aluminuim metal. Additionally, the coating will dehydrate and also shrink. So you get cracking both way. And 2024 is worse.
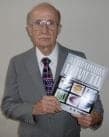
Robert H Probert
Robert H Probert Technical Services

Garner, North Carolina
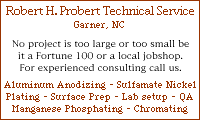
A. In addition to what Robert said, the melting point of pure aluminum is 1220 °F. Alloys will be higher, but it will not have the strength of a wet noodle at 1400 °F. Bad choice. Ceramic might work, but some of it is fragile and can be a pain to work with.
James Watts- Navarre, Florida
2005
Q, A, or Comment on THIS thread -or- Start a NEW Thread