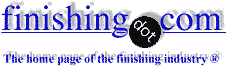
-----
Nickel Seal Verification
Q. We are having our black anodized outsourced to an anodizer. We are then taking the black anodized unit and filling it with epoxy/encapsulant. In the past we have seen that when our anodizers have used a nickel seal instead of a hot water seal the encapsulant does not stick to the anodize especially after thermal cycling. Is there a test to determine if the seal nickel acetate or hot water? Does anyone have any suggestions or options sealing the anodize and keeping the adhesion properties of the encapsulant?
Thanks for your help
- Tualatin, Oregon
2005
![]() |
A. EDAX (surface Xray) will identify nickel. For epoxy application you do not want to seal. Leave the seal off, but shorten the time between anodizing and epoxy application. ![]() Robert H Probert Robert H Probert Technical Services ![]() Garner, North Carolina ![]() A. I don't quite understand the question; do you want the epoxy/encapsulant to stick or not? It would seem your problem would be most easily solved by working with your anodizer to make sure that youalways get the same kind of seal and that it is the kind you want. Unless, you want a nickel acetate seal but don't want the epoxy/encapsulant to break free - in that case the question becomes harder. Jim GorsichCompton, California, USA |
Q. In response to the question "do you want the epoxy to stick or not?" We would like to epoxy to stick. We are not sure if our supplier is actually do what we ask them to do.
Recently I have been doing some research to answer my own question. Our supplier could be nickel sealing the product. On the other hand they could be performing he hot water seal but performing it to long.
The basic reaction is aluminum + water = Boehmite.
The longer the sealing time the more the fibrouse regions of Boehmite extend laterally into the more compact cell walls producing increases in the "filled pore" diameter and virtal disappearance of the pore structure. Therefore the epoxy will have less chances to adhere the anodize surface.
Thanks for all your help
- Tualatin, Oregon
A. We anodized hundreds of small boxes that had electronic components "potted" in them and never had a complaint with either hot water seal or the later nickel acetate seal. We may not have had a problem as we anodized at the highest amount of sulfuric acid and the coldest temperature allowed, used 20 volts for final voltage and had very very thick anodize for type II that was loved by all of our customers.
James Watts- Navarre, Florida
A. Okay, if you want the epoxy to stick, then follow Mr. Probert's advice - no seal and as short amount of time between anodizing and epoxying as possible.
Other things you might want to talk to your anodizer about would include inadvertently sealing the parts by using a hot water rinse or extended dyeing times - both baths would be heated enough to cause some sealing and possibly jeopordize your adhesion. We have a customer that has a similar process, and to finally minimize the amount of lots that the epoxy had trouble with we removed any heated baths from their processing instructions that we could, and shortened the dyeing length. It has seemed to solve the problem and we haven't had an issue in over a couple of years now.
Good luck.
Compton, California, USA
Q, A, or Comment on THIS thread -or- Start a NEW Thread