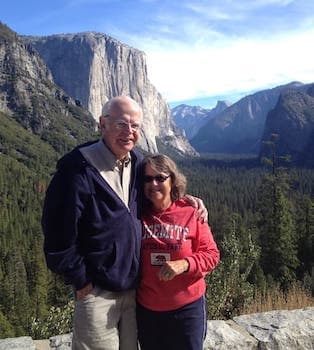
Curated with aloha by
Ted Mooney, P.E. RET
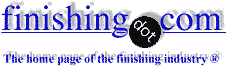
The authoritative public forum
for Metal Finishing 1989-2025
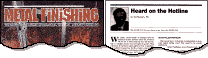
-----
Recovery of chromium from plating effluent and sludge
Q. I would like to know what is the best and suggested method for the recovery of chromium from plating effluent containing 500 mg/L chromium, chlorides and sulphates, TDS 20 g/L, pH: 8.5 and sludge containing 5-10 % chromium.
Is ion-exchange route is the preferred route for the recovery of chromium to useful and value added chemicals. If so, which one would be preferred and parameters to be adopted for its recovery with major intereferences.
Looking forward your expert opinion and suggestion!
Research Associate - Chennai, Tamil Nadu, India
2005
A. 'Expert opinion' has a specific legal meaning and you cannot get an expert opinion in response to an internet posting, Mr. Raghavan; but I (and hopefully others) will offer suggestions. Chromic acid is so abusive to organic materials that ion exchange is of limited value and only in low concentration. Note that, contrary to intuition, chrome is captured on anion resin rather than cation resin because it is CrO4-- that you are after. This approach is useful only on the plating effluent, not on sludges after reduction and precipitation.
In my experience evaporation of the rinse waters is the most practical approach, never allowing chlorides into the loop, and removing iron and trivalent chrome with porous pots. Once the chrome is in a reduced and precipitated sludge I believe that only the thermal methods associated with refineries will be able to deal with it.
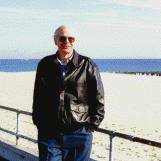
Ted Mooney, P.E.
Striving to live Aloha
finishing.com - Pine Beach, New Jersey
2005
A. In continuations to the above postings I suggest if thermal evaporation is the only viable option for rinse chemicals recovery, it is better that the rinse is subjected to RO system for concentration. The volume can be brought down to 30% and the extracted water of 70% canbe reused for rinsing. This 30% can be evaported and we can reuse both water and chemicals. Hope this helps.
Aravind A Narayan- Coimbatore, Tamilnadu, India
2006
Q. I am installing a brand new Decorative Chrome Plating Line, and I am considering to install on it a recovery chrome solution station. Can you please suggest to me what kind of equipment do I need to Install?
RENATO VILLASEACORPlating shop - Quer´taro, Mexico
May 1, 2013
A. The easiest and best way for you to recover the chromium and put it back in the plating tank is to have multiple rinses and to use evaporation to reconcentrate back to plating bath strength.
However, you will need to use DI or RO water for make-up to the rinses that go to the evaporator in order to prevent a salt build-up in the bath.
consultant - Cleveland Heights, Ohio
A. Mr Kirman has sound advice, as usual.
I would add that the issue of the build-up of contaminants needs to be addressed. Chloride is a common one, because it's a major constituent of the Ni plating that precedes the chroming step. It's also very troublesome; it acts as an unpredictable catalyst (as F- and SO4-- do) and it is quite difficult to remove.
My suggestion would be to install in the concentrate tank something called a "porous pot purifier." The catholyte, within the pot, will become enriched with trivalent chromium and various tramp cationic contaminants (the "pot" is an inorganic ion selective membrane) and will prevent them from building up. At the anode, Cl- will be oxidized to Cl2, and go up the chimney.
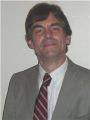
Dave Wichern
Consultant - The Bronx, New York
May 8, 2013
Q, A, or Comment on THIS thread -or- Start a NEW Thread