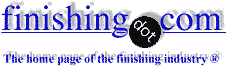
-----
Why always test the item from the center of the rack when plating
Let us say, we have an arrangement for chrome plating of Al alloy
(A356.2) wheels, where we have a single rack consisting of 3 rows of jigs & fixtures, with one wheel in each row. This single rack with 3 wheels would be plated at the same time. Let us number the wheels as wheel number 1, 2 & 3 sequentially. Wheels with number
1 & 3 are placed at the extreme end of the plating chamber and wheel with number 2 is placed between them. With this arrangement, the whole rack is now ready for plating by dipping all the three wheels in the solution simultaneously. Now the problem is, for laboratory testing, wheel number 2 is always asked for. Why ? Can somebody throw some light on this issue please ?
Regards,
Automotive - Visakhapatnam, Andhra Pradesh, India
2005
I've never heard of such a standard and until someone disabuses me of the notion I don't think it's a good idea.
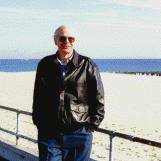
Ted Mooney, P.E.
Striving to live Aloha
finishing.com - Pine Beach, New Jersey
2005
Hello Mr Debdas,
There is no standard to this effect but it is good practice.
As current will take the path of least resistance when you plate, the parts towards the tank outer sides which are closer to the cathode power source, will tend to pick up more plating than the part in the center of the tank which will see a very mimimal drop in current. It all depends on how good your busbaring is.
Hence when aiming for a mimimum thickness in mass production, you have been advised to test the center part.
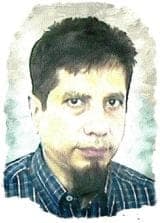
Khozem Vahaanwala
Saify Ind

Bengaluru, Karnataka, India
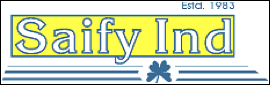
2005
Q, A, or Comment on THIS thread -or- Start a NEW Thread